The following background on building energy modeling (BEM) will provide a foundation before learning the essentials of EnergyPlus. If you are already familiar with BEM, you may wish to skip to Section 1.4 describing the EnergyPlus QuickStart Guide.
According to the BEM Library:
“Building Energy Modeling (BEM) is the practice of using computer-based simulation software to perform a detailed analysis of a building’s energy use and energy-using systems. The simulation software works by enacting a mathematical model that provides an approximate representation of the building. BEM includes whole-building simulation as well as detailed component analysis utilizing specialized software tools that address specific concerns, such as moisture transfer through building materials, daylighting, indoor air quality, natural ventilation, and occupant comfort. BEM offers an alternative approach that encourages customized, integrated design solutions, which offer deeper savings. Using BEM to compare energy-efficiency options directs design decisions prior to construction. It also guides existing building projects to optimize operation or explore retrofit opportunities."
Some other terms that are used to describe the same topic are:
Somewhat confusing, the term “model” can refer to both the specific building being described and analyzed as well as referencing the software for implementing a specific component of the building such as a wall or chiller.
To learn more about building energy modeling consider reviewing the following resources:
Building energy modeling is necessary to understand the overall energy consumption in buildings, because, the energy flows in buildings can be very complicated. The heat flow through walls is determined not just by the area and the temperatures, but the mass characteristics of the walls may result in heat flowing out of a wall several hours after it has flowed in. The constantly changing temperature on the outside of the wall and the less frequent but often large step changes in thermostat setpoints between day and night operation for the inside of the building make the direction of the heat flow vary over time. Solar energy is absorbed on the exterior wall and roof surfaces as well as entering windows. The intensity of solar energy varies by the sun position for each period of time over the day and over the year. Heat sources within the building including people, office and other equipment, and lighting include both heat that immediately impacts the air within (convective heat) and heat that is absorbed by the surfaces and released slowly over time (radiant heat). Lighting may be controlled by a sensor that turns it on or off or changes its intensity based on the amount of natural daylight that is entering the space through windows and skylights making the heat generated from the lighting system change over time. Air conditioning and heating systems come in a huge number of configurations, and each one can be used with many different control configurations based on the temperature or other conditions within each space in the building, and ultimately their operation accounts for a large portion of the energy consumed in a building. For these reasons and more, what might first appear as something that can be calculated with just a few formulas in a spreadsheet is instead a software program and, in the case of EnergyPlus, with over 500,000 lines of code.
Questions that BEM can answer[LINK]
The most common questions that BEM can answer are:
If my building was made or operated differently, how would the required equpment capacity and energy consumption change?
Does my building comply with a building energy code or standard?
What kind of rating or how many points can I get in an environmental certification program?
Is my building operating as it was designed to?
What is a good target for energy consumption for my building?
These questions and more can occur at different times during the life-cycle of a building, from before schematic design all the way through the rest of the design process, and into the operation of the building
The Design Process and BEM[LINK]
Building energy modeling can be used throughout the design process for a new building or when considering updates to existing buildings. It can also be used later in the life-cycle of a building related to comparing actual operation of the building with the predicted operation. ASHRAE Standard 209 titled “Energy Simulation Aided Design for Buildings Except Low-Rise Residential Buildings” is a critical document in how to apply building energy modeling. It describes a methodology to apply building energy modeling to the design and was created to define reliable and consistent procedures that advance the use of timely energy modeling to quantify the impact of design decisions at the point in time which they are made. The standard includes different “Modeling Cycles” for different stages of using building energy modeling during the life-cycle of the building:
Modeling Cycle #1 – Simple Box Modeling
Modeling Cycle #2 – Conceptual Design Modeling
Modeling Cycle #3 – Load Reduction Modeling
Modeling Cycle #4 – HVAC System Selection Modeling
Modeling Cycle #5 – Design Refinement
Modeling Cycle #6 – Design Integration and Optimization
Modeling Cycle #7 – Energy Simulated-Aided Value Engineering
Modeling Cycle #8 – As-Designed Energy Performance
Modeling Cycle #9 – Change Orders
Modeling Cycle #10 – As-Built Energy Performance
Modeling Cycle #11 – Postoccupancy Energy Comparison
In addition, it has information about how to integrate climate and site analysis, benchmarking, energy charrettes (a meeting of the stakeholders to discuss goals and design strategies) and the energy performance goals of the owners project requirements into the design process when using building energy modeling.
EnergyPlus QuickStart Guide[LINK]
Don’t be intimidated by the apparent complexity of EnergyPlus; you can get started using EnergyPlus quickly using the QuickStart Guide which is part of the documentation. It shows you how you can use just an input file and some output files to start seeing results quickly. The building description, the detecting and solving of errors, and the most common primary outputs are found in the IDF input file, the Table.HTML output file and the .ERR diagnostics file. Starting with these three files and branching out to others as needed is a good strategy for learning EnergyPlus.
EnergyPlus Capabilities[LINK]
According to the energyplus.net web site (as of January 2019):
“EnergyPlus is a whole building energy simulation program that engineers, architects, and researchers use to model both energy consumption—for heating, cooling, ventilation, lighting and plug and process loads—and water use in buildings. Some of the notable features and capabilities of EnergyPlus include:
Integrated, simultaneous solution of thermal zone conditions and HVAC system response that does not assume that the HVAC system can meet zone loads and can simulate un-conditioned and under-conditioned spaces.
Heat balance-based solution of radiant and convective effects that produce surface temperatures, thermal comfort, and condensation calculations.
Sub-hourly, user-definable time steps for interaction between thermal zones and the environment; with automatically varied time steps for interactions between thermal zones and HVAC systems. These allow EnergyPlus to model systems with fast dynamics while also trading off simulation speed for precision.
Combined heat and mass transfer model that accounts for air movement between zones.
Advanced fenestration models including controllable window blinds, electrochromic glazings, and layer-by-layer heat balances that calculate solar energy absorbed by window panes.
Illuminance and glare calculations for reporting visual comfort and driving lighting controls.
Component-based HVAC that supports both standard and novel system configurations.
A large number of built-in HVAC and lighting control strategies and an extensible runtime scripting system for user-defined control.
Functional Mockup Interface import and export for co-simulation with other engines.
Standard summary and detailed output reports as well as user definable reports with selectable time-resolution from annual to sub-hourly, all with energy source multipliers."
In addition:
ASCII text-based weather, input, and output files that include hourly or sub-hourly environmental conditions, and standard and user definable reports, respectively.
Transient heat conduction through building elements such as walls, roofs, floors, etc. using conduction transfer functions.
Thermal comfort models based on activity, inside dry-bulb temperature, humidity, etc.
Anisotropic sky model for improved calculation of diffuse solar on tilted surfaces.
Atmospheric pollution calculations that predict CO2, SOx, NOx, CO, particulate matter, and hydrocarbon production for both on-site and remote energy conversion.
EnergyPlus can be used for for building load calculations and sizing equipment and uses the heat balance method recommended in the ASHRAE Handbook Fundamentals. Proper sizing of equipment without oversizing, generally saves energy as the equipment is operated nearer to optimal loads.
EnergyPlus runs on Windows, MacOS, and Linux computers.
Integration of Loads, Systems, and Plants: One of the strong points of EnergyPlus is the integration of all aspects of the simulation—loads, systems, and plants. System and plant output are allowed to directly impact the building thermal response rather than calculating all loads first, then simulating systems and plants. The simulation is coupled allowing the designer to more accurately investigate the effect of undersizing fans and equipment and what impact that might have on the thermal comfort of occupants within the building.
EnergyPlus is an Open Source program so all the source code is available to inspect and modify. If you are interested in how calculations are performed and the Engineering Reference does not provide enough details to you, you can review the source code itself. Instructions to build the code (compile the source code into an executable application) are available in the source code repository wiki if you see something that needs to be enhanced or fixed, please also see the contribution policy.
Brief History[LINK]
EnergyPlus has been under development since 1997 and was first released in 2001. EnergyPlus has its roots in both the BLAST and DOE–2 programs. BLAST (Building Loads Analysis and System Thermodynamics) and DOE–2 were both developed and released in the late 1970s and early 1980s as energy and load simulation tools. BLAST was developed by the Construction Engineering Research Laboratory (CERL) and the University of Illinois while DOE-2 was developed by Berkeley Lab and many others. Their intended audience is a design engineer or architect that wishes to size appropriate HVAC equipment, develop retrofit studies for life cycling cost analyses, optimize energy performance, etc. Born out of concerns driven by the energy crisis of the early 1970s and recognition that building energy consumption is a major component of the American energy usage statistics, the two programs attempted to solve the same problem from two slightly different perspectives. In the late 1990s, concern about limitations of both BLAST and DOE-2 as well as difficulty in maintaining the old code bases prompted combining the development efforts for a new program called EnergyPlus. EnergyPlus was originally written in Fortran, in 2014 it was converted to C++. It was developed as a simulation engine, and many graphical user interfaces utilize it.
Documentation[LINK]
The EnergyPlus documentation is currently included in the installation in the “Documentation” folder as PDFs. It is also available as PDFs online and from third parties that have generated HTML documentation from the source. Using search in the documentation is critical to finding the information needed. Some of the documentation PDFs are very large, so searching is a good way to find specific information about a topic or an input object. The documentation includes:
QuickStart Guide: Contains a brief high-level overview of EnergyPlus and get you up and running quickly with the program
Input Output Reference: Contains a thorough description of the various input and output files related to EnergyPlus, the format of these files, and how the files interact and interrelate.
Output Details and Examples: Contains details on output from EnergyPlus. It also addresses the reference data sets that are included.
Auxiliary Programs: Contains information for the auxiliary programs that are part of the EnergyPlus package. For example, this document contains the user manual for the Weather Converter program, descriptions on using Ground Heat Transfer auxiliary programs with EnergyPlus, and other assorted topics.
Engineering Reference: Provides more in-depth knowledge into the theoretical basis behind the various calculations contained in the program including algorithm descriptions.
Application Guide for EMS: Provides an in-depth look at the Energy Management System (EMS) feature which provides a way to develop custom control and modeling routines.
External Interface(s) Application Guide: Contains information specific to using the external interface feature of EnergyPlus to connect other simulation systems.
Plant Application Guide: Details the methods for simulating chilled and hot water plant systems within EnergyPlus.
Using EnergyPlus for Compliance Guide: Contains information specific to using EnergyPlus in compliance and standard rating systems.
Tips & Tricks for Using EnergyPlus: Contains short tips and tricks for using various parts of EnergyPlus.
Example Files[LINK]
Many hundreds of example files come with EnergyPlus, and they are in the ExampleFiles folder from the installation. The \ExampleFiles\ExampleFiles.html lists each one and includes the name, a description (scroll all the way to the right) and lots of information such as the floor area and whether certain types of input objects are included in the file. Often searching through this file is a good way to find the proper example file to learn about a feature. Another method is the \ExampleFiles\ExampleFiles-ObjectsLink.html file which lists every type of input object that EnergyPlus uses and then the first three files that use that input object. It is possible that many other files also use a particular input object so if the first three files do not help, a text search of files in the ExampleFiles folder may find more.
The EnergyPlus Ecosystem[LINK]
Current Interfaces[LINK]
EnergyPlus is often used directly using the text file input (IDF or epJSON) and various output file formats along with the utilities that come with the installation package. More information on that can be found in section 3. In addition, EnergyPlus is often the simulation engine for graphical user interfaces. To see a list, see the BEST (Building Energy Software Tools) Directory that is operated by IBPSA-USA.
Approaches to Implement Measures[LINK]
In the terminology used within the building energy modeling industry “measures,” sometimes called energy conservation measures (ECMs) or energy efficiency measures (EEMs), are when alternative configurations of a building are considered and simulated and compared with the original building model. Measures include added wall or roof insulation, lower internal lighting power, higher efficiency heating and cooling equipment, and many others. When using EnergyPlus within a graphical user interface, that interface often provides a way to implement various measures. When not working within a graphical user interface, users have several options for implementing measures.
For a specific building input file, a copy of the input file can be made and then modified to reflect the measure. This is an easy approach initially, but since the original building model might change, it means making the change in the file that reflects the measure. When many measures are being considered, this duplicative editing can be inefficient and prone to errors. In addition, the measure cannot be easily applied to a different building energy model without again editing another set of files duplicating the original effort. Due to this, it is very common for some type of scripting to be used so that measures can be applied to the original building model and other models of other buildings reliably and quickly. Scripting in this approach means to apply some type of programming language to the task of modifying files.
EnergyPlus includes, with the installation package, two methods of implementing measures EP-Macro and the ParametricPreprocessor. EP-Macro is similar to the C language pre-processor and allows for portions of the file to be included or excluded, portions of other files to be included when desired, and for specific entries that are normally fixed values to change programmatically. EP-Macro is documented in the AuxiliaryPrograms documentation. A file with lines starting “##” or with the “imf” file extension is likely to be a file using EP-Macro commands.
The EnergyPlus ParametricPreprocessor uses special input objects in EnergyPlus to set values for any field in any other input object for a series of simple options. This is briefly described in the AuxiliaryPrograms documentation, and more details are present in the InputOutputReference under the section on “Parametric Objects.” The ParametricPreprocessor approach is very straight forward, however it has limits in the flexibility that it provides. It is suitable for implementing measures related to internal loads, constructions, and simple efficiency changes but is probably not the appropriate tool for more complicated measures.
A paper that describes various other approaches to scripting was written during the 2018 ASHRAE/IBPSA-USA Building Performance Conference and SimBuild.
When just implementing a simple measure or even a series of measures is not enough, a parametric analysis tool may be appropriate. These tools allow the exploration throughout the range of variables (such as the thickness of insulation in the roof or the efficiency of a boiler) to see the impacts of optimization. While many of the approaches used to implement measures described previously may also be used for parametric analysis, a few specific tools have been developed. To see a list, see the BEST (Building Energy Software Tools) Directory that is operated by IBPSA-USA.
Weather Files[LINK]
Weather files are available for many locations throughout the world. Finding the right file that represents the weather in your specific location can sometimes be a challenge. Often the closest weather location is the best one to choose, but sometimes a site that is further away may actually have the most similar weather. This is especially the case in terrain that varies in elevation or when near large bodies of water. Many weather files are available from both public and private sources. The EnergyPlus weather file web site has many weather files with sources described. That web site also has a page with links to many other sites that provide weather files. The modeler must also choose between using a typical year weather files or an actual year file. Typical year files, such as TMY3 and IWEC are representative of long-term weather compiled from 20-30 years of data. Actual year files contain a specific year of weather data and generally used for calibration or verification studies where the simulation results are compared to actual utility bills or other measured data.
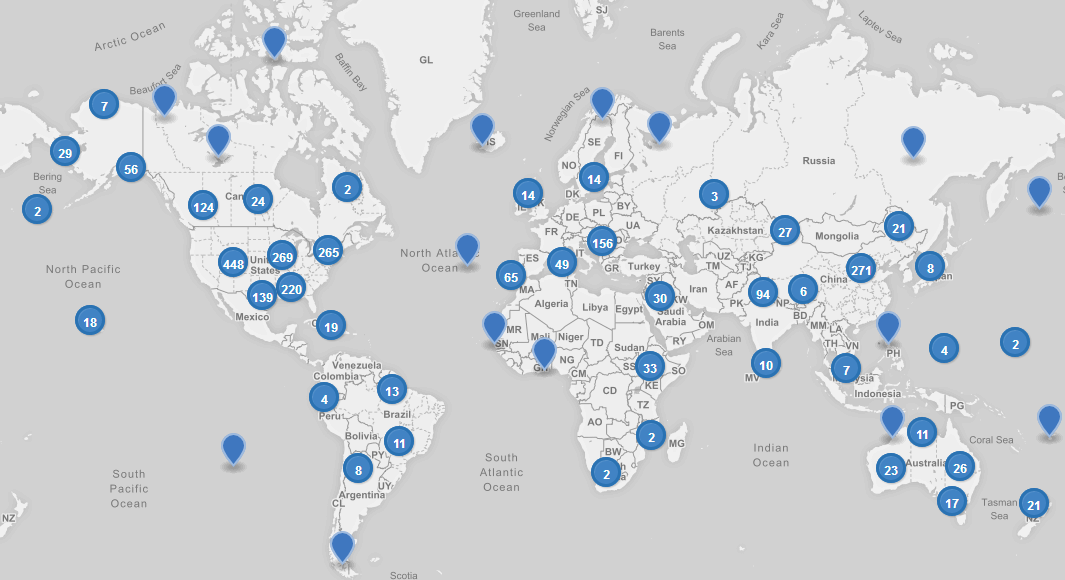
Co-Simulation and Linked Software[LINK]
The modelling of multi-domain, multi-physics, and multi-time scale systems such as buildings is a challenge for building energy modelling and simulation tools. In certain circumstances, it may be better for modelling such systems to split the systems into multiple sub-systems, model the individual sub-systems in the language or tool which is best suited for the system’s domain, and use a master algorithm to link the sub-systems for a so called “co-simulation.” In a nutshell, co-simulation consists of the theory and techniques that enable the simulation of a coupled system through the composition of simulators. Each simulator is an input-output mock-up of a constituent system, developed and provided by the team that is responsible for the sub-system. The coupling of the sub-systems is performed by a master algorithm which is responsible for linking the sub-systems at run-time for data-exchange. EnergyPlus implements three mechanisms to support co-simulation.
EnergyPlus implements the Building Controls Virtual Test Bed ( BCVTB) API. This API leverages the BCVTB to enable the co-simulation of EnergyPlus with various simulation programs such as TRNSYS, ESP-r, Radiance, or DYMOLA.
EnergyPlus provides an interface which allows it to import, link, and exchange data with simulation models which implement the Functional Mock-up Interface (FMI) for co-simulation. Such models are called Functional Mock-up Units (FMUs). This feature allows for instance the integration and testing of Simulink or Modelica-based control algorithms which may not exist in EnergyPlus.
EnergyPlus itself can be exported as an FMU which implements the FMI for co-simulation. Such FMU can then be imported into any simulation engine which implements the FMI import interface for co-simulation. This feature is relevant for applications such as the development of building controls. For example, the building envelope of EnergyPlus may be exported as an FMU which in turn will be imported in a tool which is best suited for control development. In this use case, the FMU will be used as a boundary condition for control’s development.
Several resources are available for getting help when using EnergyPlus:
Please do not post questions as issues on the EnergyPlus Github website. Of course, if you are using a graphical user interface with EnergyPlus, the vendor will provide direct support.
After reviewing this document and other pertinent documents that come with EnergyPlus like the InputOutputReference, if additional training is required, several sources are available:
In addition, if you are using a graphical user interface, the vendor probably also provides training.
Using EnergyPlus[LINK]
Installing EnergyPlus[LINK]
Please see the EnergyPlus QuickStart Guide for instructions on how to install EnergyPlus for your system.
Running EnergyPlus[LINK]
EnergyPlus is a simulation engine, so it was designed to be an element within a graphical user interface. However, it can be run standalone without such an interface. There are several options for performing a simulation with EnergyPlus:
Graphical user interface
Command line
EP-Launch
In each case, a building model will be simulated in combination with a weather file for the appropriate building location.
Graphical User Interface[LINK]
When running an EnergyPlus simulation within a graphical user interface, the exact method will vary depending on the specific program being used. You should read the documentation for that software to understand how to perform a simulation. In all cases, the interface will ultimately generate an EnergyPlus idf or epjson input file, execute the EnergyPlus simulation, and read the EnergyPlus output files to present results.
EnergyPlus can be used as a command line tool within a Terminal window in Linux or MacOS or with the CMD prompt or PowerShell window under Windows. Basic usage using the command line approach is well documented in the QuickStart Guide. To learn more about the command line mode, you can type:
energyplus --help
when in the EnergyPlus folder. This will give the following display of options:
EnergyPlus, Version 9.0.1-bb7ca4f0da
Usage: energyplus [options] [input-file]
Options:
-a, --annual Force annual simulation
-c, --convert Output IDF->epJSON or epJSON->IDF, dependent on
input file type
-d, --output-directory ARG Output directory path (default: current
directory)
-D, --design-day Force design-day-only simulation
-h, --help Display help information
-i, --idd ARG Input data dictionary path (default: Energy+.idd
in executable directory)
-m, --epmacro Run EPMacro prior to simulation
-p, --output-prefix ARG Prefix for output file names (default: eplus)
-r, --readvars Run ReadVarsESO after simulation
-s, --output-suffix ARG Suffix style for output file names (default: L)
L: Legacy (e.g., eplustbl.csv)
C: Capital (e.g., eplusTable.csv)
D: Dash (e.g., eplus-table.csv)
-v, --version Display version information
-w, --weather ARG Weather file path (default: in.epw in current
directory)
-x, --expandobjects Run ExpandObjects prior to simulation
Example: energyplus -w weather.epw -r input.idf
EnergyPlus can be run by specifying a number of options followed by the path to the input file. The file itself is usually in IDF (Input Data File) format or epJSON format, but it may also be in IMF (Input Macro File) format to be run with EPMacro using the –epmacro option. Each option has a short form (a single-character preceded by a single dash, e.g., -h) and a long form (a more descriptive string of characters preceded by double dashes, e.g., –help). Several of these options are commonly used including the weather, output-prefix, expandobjects, and readvars options. The following are some examples of using the command line options.
Pre-processing using EPMacro and ExpandObjects:
energyplus -w weather.epw -m -x input.imf
Forcing design-day only simulations:
energyplus -D input.idf
Giving all output files the prefix being the same as the input file (building.idf) and placing them in a directory called output:
energyplus -w weather -p building -d output building.idf
If no arguments are passed on the command line, EnergyPlus expects the input and weather files to be located in the current working directory and name in.idf (or in.epjson) and in.epw respectively.
For users that want a simple way of selecting files and running EnergyPlus, EP-Launch provides this and more. In addition, EP-Launch can help open a text editor for the input and output files, open a spreadsheet for the result files, a web browser for the tabular results file, and start up a viewer for the selected drawing file. There are two different versions of EP-Launch currently part of the EnergyPlus system.
The main screen of EP-Launch 2 is shown below:
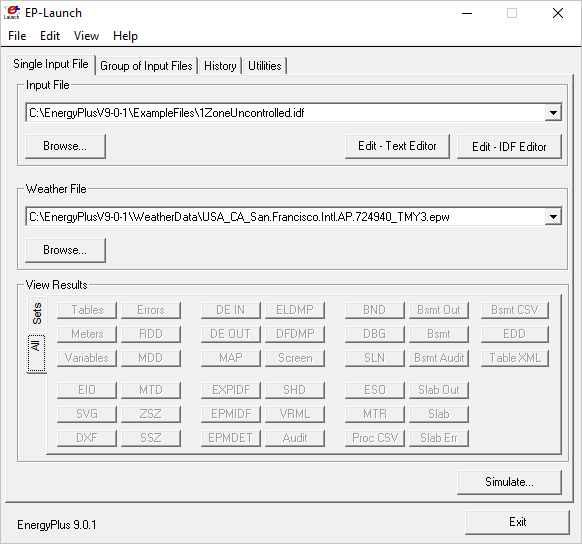
It is a Windows program only. EP-Launch 2 is included in the EnergyPlus installation package when installing on Windows, so no additional steps are needed to run it. It is located in the main “root” folder of EnergyPlus, usually, a folder named EnergyPlusVx-x-x, where the x’s are the version number.
In 2018, EP-Launch 3 was developed, and its main screen is shown below:
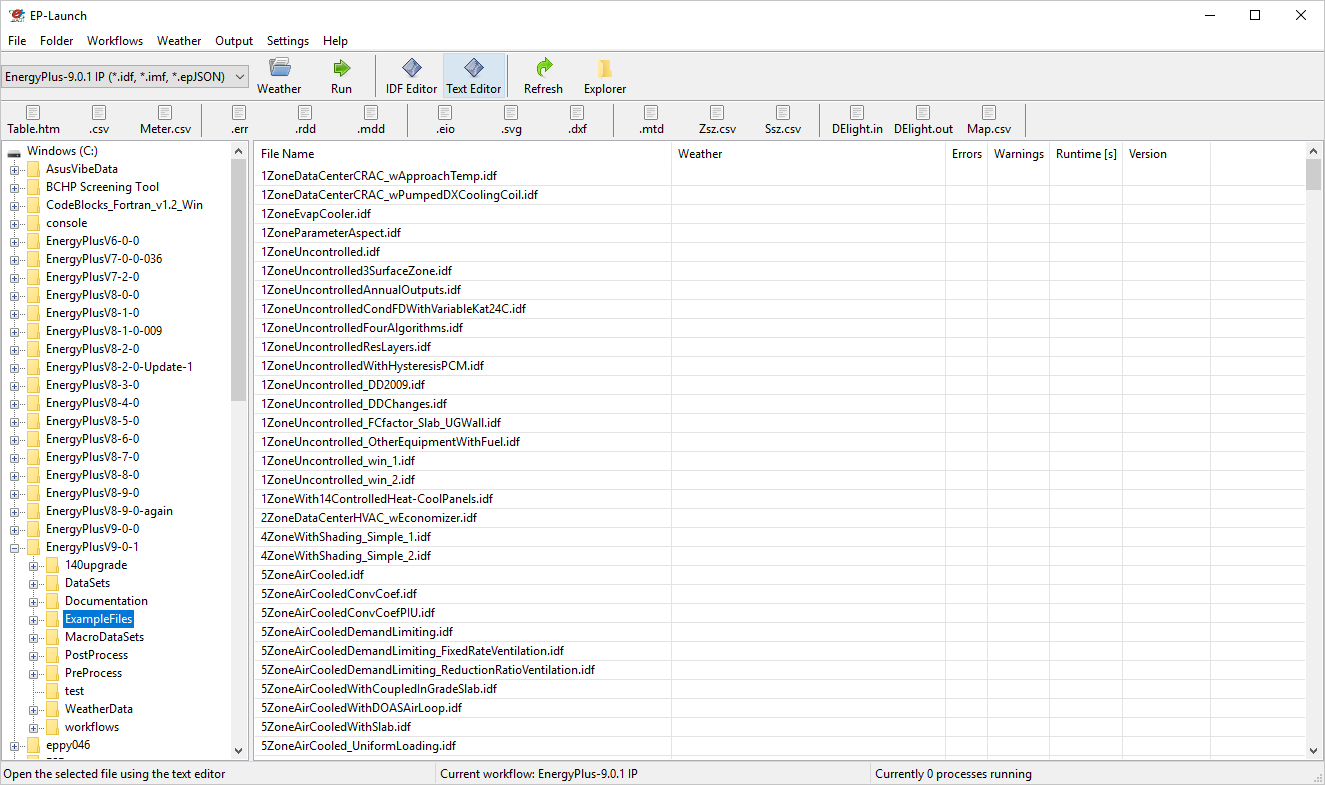
EP-Launch 3 is not part of the EnergyPlus installation package and needs to be installed separately. It is also open source and is available from GitHub, and it is documented on readthedocs or in the docs folder on GitHub. EP-Launch 3 works on Windows, MacOS, and Linux systems and is written in Python.
While both EP-Launch 2 and EP-Launch 3 do many of the same functions, the interface is quite different. For now, EP-Launch 2 allows groups of files to be run together and has access to some utilities that the newer version does not. EP-Launch 3 works across multiple platforms and is a built from the ground up to be flexible and extensible so that individuals can make their own workflows that run whatever programs they need to run.
IDF and JSON syntax[LINK]
EnergyPlus has two different input file formats that can be used to describe the building and system that is simulated. The file extensions for the two formats are IDF and epJSON. For both input files, the numeric inputs are in SI units (International System of Units often called metric units).
The legacy file format is a text-based format that describes each input object in series. Each input object starts with the type of input object, and each value for each field follows in strict order separated by commas. The end of the input object is indicated by a semi-colon. Comments are indicated by an exclamation point “!” and anything after this is ignored by EnergyPlus. Commonly, an input object is spread over many lines in the file with one value for each field per line. The names of each field are not required but are usually shown after the value and the comma or semicolon as a special comment using “!-” as an indicator. The input objects can be in any order. An example of an input object in an IDF file is shown below:
Building,
Simple One Zone, !- Name
0, !- North Axis {deg}
Suburbs, !- Terrain
0.04, !- Loads Convergence Tolerance Value
0.004, !- Temperature Convergence Tolerance Value {deltaC}
MinimalShadowing, !- Solar Distribution
30, !- Maximum Number of Warmup Days
6; !- Minimum Number of Warmup Days
The details of this example input object are not important, but the use of commas, exclamation points, and the closing semi-colon are important. The IDF format is currently the most commonly used format throughout the EnergyPlus ecosystem of utilities and GUIs. The list of possible input objects and fields is documented in the Energy+.idd file.
A variation on the IDF file format is the IMF file format which includes macros that can be used for parametric analysis or file management called EP-Macros. To learn more about macros see the Input Macros chapter of the AuxiliaryPrograms document.
A new file format based on the industry standard JSON format most often used to transmit data to and from web servers and web-browser based applications. It is a text-based file format. The JSON format has wide usage across many industries and is supported in just about every modern programming language. It is a field-value style format using brackets and colons to indicate the hierarchy and commas to separate each field and value pair. The input objects must appear grouped by the type of input object. The list of possible input objects and fields is documented in the Energy+.schema.epJSON file which uses json-schema. The same input object shown above in IDF format is shown below in epJSON format:
{
"Building": {
"Simple One Zone: {
"idf_max_extensible_fields": 0,
"idf_max_fields": 8,
"idf_order": 3,
"loads_convergence_tolerance_value": 0.04,
"maximum_number_of_warmup_days": 30,
"minimum_number_of_warmup_days": 6,
"north_axis": 0,
"solar_distribution": "MinimalShadowing",
"temperature_convergence_tolerance_value": 0.004,
"terrain": "Suburbs"
}
}
}
While the IDF and epJSON file formats are quite different, they contain the same information, and either may be used. In general, if producing EnergyPlus input files using a programming language, the epJSON format might make more sense while, at this point, if producing IDF files using a GUI, they are likely to use the IDF format. EnergyPlus, when used on the command line, can convert from IDF to epJSON and from epJSON to IDF using the -c or –convert option.
Since both the IDF and epJSON file formats are text formats, a simple text editor may be used to edit them. Even if not regularly used, a good text editor is an important application to have when working with EnergyPlus. There are many different text editors, and a few have special features related to the IDF format such as syntax highlighting including Atom, Notepad++, and UltraEdit.
Another editing choice for IDF file is the IDF Editor which comes with EnergyPlus in the \PreProcess\IDFEditor directory and can be run directly or from EP-Launch. It is a Windows-only program and was not designed to run on Linux or MacOS. It is specially designed for editing IDF files and includes many features to simplify the process. It performs unit conversions so either SI (metric) or IP (inch-pound) units can be used for editing but the IDF file is always saved in SI units. It can initialize an input object using the default values and has indications when values outside the acceptable range are used. The main screen of the IDF editor is shown below. Full details of the IDF Editor can be found in the Auxiliary Programs document under the “Creating Input Files” section.
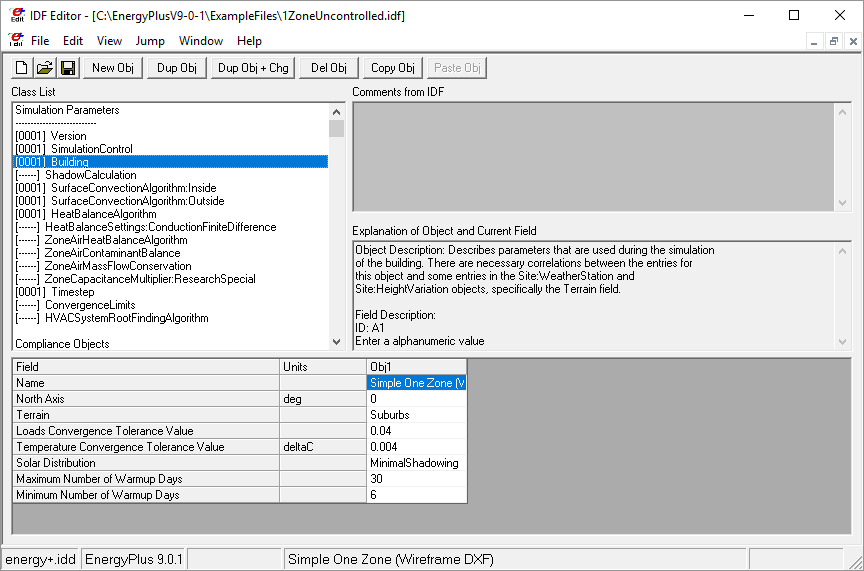
Run-Check-Edit Repeat[LINK]
For most building energy modeling projects, whether assisting in early design, refining a design, selecting a control method, or calibrating an existing building, the use of EnergyPlus will be part of a repeating process. The process will probably be in the form of:
Don’t expect that an initial model is ever correct; it is probably not. Initially, errors are likely to exist. The .ERR file should be the first file checked each time EnergyPlus is run. The .ERR file has several levels of messages:
A Fatal error means that EnergyPlus has stopped during the simulation and the input file needs to be fixed before the simulation can be run to completion. Fatal errors should be the first thing fixed. Some Fatal messages reference previous Severe messages so in that case those should be fixed. Since the entire simulation was not performed, it is likely that once the fatal errors are fixed that new Severe and Warning messages will be shown. After all Fatal messages are eliminated, you should work on Severe messages; they should also be fixed. Finally, Warning messages should be reviewed. Often Warning messages are informative and point out unusual configurations, conditions, or choices. If what is being described by the Warning message is as intended, then the Warning message can be ignored. More often, the Warning message points out something that is not as intended and should be fixed or addressed. Since the .ERR file is a text file; you can usually keep it open in a text editor program. Many (but not all) text editor programs will detect that the .ERR file has been updated after each EnergyPlus simulation and lets you load the most recent version.
The next files to be examined are ones that show output results from the simulation. Either the tabular output file (usually an HTML file see Output:Table:SummaryReports and OutputControl:Table:Style) or CSV file (see Output:Variable and Output:Meter) should be examined depending on what you want to look at. Upon examination of the output results, it is very likely that an aspect of the building and its systems are not behaving as expected. For example, the Annual Building Utility Performance Summary report contains a subtable titled Comfort and Setpoint Not Met Summary. If an annual simulation has 100s or 1000s of hours of setpoint not met, then the HVAC system is undersized, or the controls are not working as expected. With an input file representing many thousands of assumptions, some assumptions made by you or as a default of EnergyPlus are likely to be incorrect. Revising the EnergyPlus input file to address this may cause new issues to be shown in the .ERR file so it should always be examined after each change.
To speed the process of running the simulations, you may want only to run a design day (see SimulationControl and SizingPeriod:DesignDay) or a subset of the year (see RunPeriod) while developing and debugging the inputs. This approach speeds up the simulation time itself, and if used, please remember to recheck the .ERR file when running an annual simulation for the first time.
The following sections highlight some key concepts in EnergyPlus
Everything Included[LINK]
One principal that EnergyPlus uses is that (almost) everything is specified in the input file. This means that instead of referencing an external library for materials, schedules, equipment performance, etc., the input objects that fully describe those items should be included directly in the input file. In addition, each input object contains a list of values for every field that needs one. The DataSets folder distributed with EnergyPlus contains these kinds of details and to use them, the input objects should be copied into the input file that you are developing. This approach does make the file include more specification than you might be used to, and typically results in a large input file, but you will have the assurance of knowing that all the inputs related to your building are in the input file you have developed. There are a few exceptions where external data is referenced such as with Schedule:File input objects.
Wall Thickness[LINK]
Exterior and interior walls in real buildings have a thickness as specified on building plans by detailed cross-sections. For EnergyPlus, the Construction input object is made up of a list of names for the Material input objects that make up the wall or roof or floor. Each material input object has a thickness along with the conductivity, density, specific heat and other factors. These thicknesses should match the thicknesses shown in the detailed cross-sections. But when it comes to specifying the walls themselves in three-dimensional space, the walls should be entered assuming zero thickness. Once each surface has been placed, changing the material thickness will have no impact on zone volume, ceiling height, floor area, shading, or daylighting. For most modern buildings the choice of where to locate the wall: inside vs. outside vs. centerline should have little impact on results, so many modelers just pick one and let the volumes be slightly off. Using centerlines throughout the model splits the difference. Or some modelers use outer edges for exterior walls and then use centerlines for interior walls. If you are modeling a very thick wall, such as an old stone building, then you also have thermal mass considerations. If you use the outside edges there will be too much mass, inside will be too little. Again, centerline will split the difference and will be very close to the correct amount of thermal mass (possibly losing some corner mass).
Zones Are Not the Same as Rooms[LINK]
A zone, sometimes called a “thermal zone,” is a theoretical construct that usually describes a group of rooms that can be treated as a single thermal entity. A zone typically includes multiple rooms. Often a zone can be seen as a group of rooms that share a single thermostat. In the case of many similar rooms with the same thermal and operating characteristics, even if many different thermostats are used, they may still be grouped into a single zone in EnergyPlus.
One Construction Per Surface[LINK]
Only one type of construction can be associated with each surface so if the top half of a wall is made up of a different construction than the bottom half of the wall, the top half and the bottom half each need to be represented as separate surfaces.
Available Outputs Created by First Simulation[LINK]
Since EnergyPlus creates a custom list of possible output variables during each simulation, you need to perform a simulation first before you can see them. To create the list use the Output:VariableDictionary input object and then check the .RDD and .MDD files that are created. Select the outputs you want and specify them in the input file.
Always Plan Ahead[LINK]
Some preliminary steps will facilitate the construction of your input file. EnergyPlus requires some information in specified, externally available formats; other information may require some lead time to obtain. The following checklist should be completed before you start to construct your input file.
Obtain location and design climate information for the city in which your building is located. If possible, use one of the weather files available for your weather period run.
Obtain sufficient building construction information to allow specification of overall building geometry and surface constructions (including exterior walls, interior walls, partitions, floors, ceilings, roofs, windows, and doors).
Obtain sufficient building use information to allow specification of the lighting and other equipment (e.g., electric, gas, etc.) and the number of people in each area of the building.
Obtain sufficient building thermostatic control information to allow specification of the temperature control strategy for each area of the building.
Obtain sufficient HVAC operation information to allow specification and scheduling of the fan systems.
Obtain sufficient central plant information to allow specification and scheduling of the boilers, chillers and other plant equipment.
Obtain utility tariff information when expressing the results as costs.
Obtain component cost information when performing life-cycle costs.
What Are All These Folders?[LINK]
The installation of EnergyPlus includes many different files in different folders:

Many of these folders include valuable resources for using and learning EnergyPlus.
The main folder includes the EnergyPlus executable which can be used on the command line and EP-Launch 2, a program that makes it easier to use EnergyPlus and the Energy+.IDD that describes each possible EnergyPlus input object and the default, minimum, maximum, and options for each field within each input object.
The Documentation folder includes this document as well as the InputOutputReference, EngineeringReference, AuxiliaryPrograms, OutputDetailsAndExamples which are very important to understand. If you haven’t looked through the documentation yet, take a few minutes and get familiar with it.
The DataSets and MacroDataSets folders include files containing libraries of input objects that may be useful in constructing your own input files. The ASHRAE_2005_HOF_Materials.idf and WindowConstructs.idf files, for example, will help with defining walls and windows.
The ExampleFiles folder includes a huge number of example files that are indexed in the two HTML files in that folder or can be searched through using most text editors.
The Preprocess and PostProcess folders include many utilities that can be used directly or as part of EP-Launch that can aid in the setting up input files or extracting or converting results. The WeatherData folder includes a small sample of the many weather files that are available. For other weather files, please see the previous section on 2.4.
What Are All These Output Files?[LINK]
When running EnergyPlus using EP-Launch or from the command line, depending on the options selected, many different output files may be generated. The file extensions and file suffixes (added to the original file name prior to the file extension are shown below:
ERR – list of errors and warnings
TABLE.HTML, TABLE.TXT, TABLE.TAB, TABLE.CSV, TABLE.XML – tabulated report of the bin and monthly data in HTML, space delimited, tab delimited, comma delimited, or XML format. This is one of the primary otuput files.
CSV, TAB, or TXT – time series output from the Output:Variable input object in a comma, tab, or space delimited format (generated by the ReadVarsESO postprocessor)
METER.CSV, METER.TAB, or METER.CSV File – time series output from the Output:Meter input object in a comma, tab, or space delimited format (generated by the ReadVarsESO postprocessor)
SQL - sqlite3 output database format
EIO – additional EnergyPlus results
RDD – list of output variables available from the run
MDD – list of output meters available from the run
MTD – list of meter component variables
DXF – drawing file in AutoCAD DXF format
AUDIT – input file echo with input processor errors and warnings
BND – HVAC system node and component connection details
DBG – output from the debug command
EDD – Energy Management System details
END - a single line synopsis of the simulation
EPMIDF – clean idf file after EP-Macro processing
EPMDET – EP-Macro detailed output with errors and warnings
ESO – raw Output:Variable output before processing into CSV, TAB, or TXT files
MTR – raw Output:Meter output before processing into CSV, TAB, or TXT files
SHD – output related to shading
SLN – output from “report, surfaces, lines”
SSZ – system sizing details in a comma, tab, or space delimited format
ZSZ – zone sizing details in a comma, tab, or space delimited format
MAP – daylighting illuminance map
DFS - daylighting factors report
Screen.CSV - window screen transmittance map report
RVAUDIT - output from the ReadVarsESO post-processing program
SVG - HVAC Diagram related to the arrangement of HVAC components
SCI - surface cost information report
WRL – drawing file in VRML (Virtual Reality Markup Language) format
Delight IN - DElight input generated from EnergyPlus processed input
Delight OUT – Detailed DElight output
Delight ELDMP – DElight reference point illuminance per time step
Delight DFDMP – DElight warning and error messages
EXPIDF – Expanded IDF when using HVACTemplate input objects
Group Error – combined error files for a group run
VCpErr – Transition program error file
Proc.CSV – Simple statistics generated from CSVProc
Most of these output files are documented in the Output Files chapter of the OutputDetailsAndExamples document.
Don’t be intimidated by the long list of files; you can do a lot in EnergyPlus with just the IDF input file, the TABLE.HTML file, and the ERR file. The building description, the detecting and solving of errors, and the most common primary outputs are found between these three files. Starting with these three files and branching out to others as needed is a good strategy for using EnergyPlus.
Versions and Updating[LINK]
EnergyPlus version updates are released generally twice per year in March and September. Each version of EnergyPlus is installed to a unique folder, so it is possible, and recommended, to keep older versions in place when adding a new one. This is very helpful if you need to go back and make a change to an older project and don’t want to introduce version-related changes in results. When using the IDF input file format with EnergyPlus, each release is likely to have small changes to the file format. Included with EnergyPlus are a number of ways to update files so that they are compatible with the release. Each method ultimately uses the TransitionVx-x-x-ToVx-x-x.exe files that are located in the Preprocess\IDFVersionUpdater folder. The ways to update your IDF files are:
- IDFVersionUpdater program (shown below) is included in the installation and works on multiple platforms. It is located in the Preprocess\IDFVersionUpdater folder. It can convert from EnergyPlus 7.2 to the most recent version, and even older versions can be converted if the proper files are downloaded from the helpdesk. It can also update a group of files. It is documented in the Chapter titled “Using Older Version Input Files - Transition” in the AuxiliaryPrograms document.
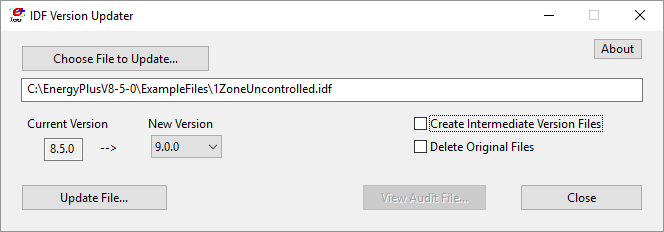
EP-Launch 2 - The Windows-only program that comes with the EnergyPlus installation can update a single file from the just previous version of EnergyPlus by using the File…Transition command.
EP-Launch 3 - The program for Windows, Linux, and MacOS can update a single file across multiple versions using the Transition workflow.
Command line Transition - This allows updating files using the command line such as the Terminal for MacOS and Linux or the CMD or PowerShell for Windows. It is documented in the Chapter titled “Using Older Version Input Files - Transition” in the AuxiliaryPrograms document.
Errors and How to Fix Them[LINK]
As described in the section dealing with errors described in the ERR file are part of creating files with EnergyPlus. Resolving errors is something that both new and very experienced users have to do. Most of the error message itself, if carefully reviewed will point to the problem. Some error messages will also reference earlier messages that should also be checked. A careful review of the ERR file and the input file will often reveal solutions to the most common errors. Also, see the section.
EnergyPlus uses snippets of IDF files to create the library of data that may be useful for you. Two folders are created upon installation: DataSets – which contains IDF snippets and MacroDataSets – which also contain IDF snippets but are in a form such that they can be easily used with the EPMacro program. Another data set are DDY files that acompany each EPW weather file. The DDY files include several varieties of the corresponding design day data for each weather file location.
Other Useful Utility Programs[LINK]
The EnergyPlus install includes a variety of tools to help with various aspects of converting data or displaying information to help with using EnergyPlus
Coefficient Curve Generation - The CoeffConv and CoeffConv utility programs can be used to convert DOE-2 temperature dependent curves (Fahrenheit) to EnergyPlus temperature curves (Celsius). These programs are described in the Auxiliary Programs document.
HVAC Performance Curve Fit Tool - The CurveFitTool.xlsm spreadsheet generates performance curves for a set of tabular data as typically supply by manufacturers
HVAC-Diagram - Another post-processing program is the HVAC-Diagram application. It reads one of the EnergyPlus output files (eplusout.bnd) and produces a Scalable Vector Graphics (SVG) file. Many web browsers and other drawing programs can open SVG files. This utility runs automatically with EP-Launch. More information on the HVAC Diagram program is found in the Auxiliary Programs document.
convertESOMTR - This simple post-processing program can be used seamlessly with EP-Launch to provide IP (inch-pound) unit output files rather than SI units. This program is described more fully in the Auxiliary Programs document.
WeatherConverter - Used to convert epw to csv format with column headings to inspection of the data.
The following sections provide an overview of the input objects based on groups described in the energy+.idd file and the InputOutputReference. The sections give you a taste of the capabilities and may help guide you to further investigation on how to model your building or a specific energy efficiency measure.
Simulation Parameters[LINK]
EnergyPlus includes a group of input objects used to set general parameters related to how the simulation is performed. Some of these input objects are controlling different options that are allowed within EnergyPlus such as the selection of algorithms to use or parameters related to how an algorithm is used. For a new modeler, these input objects should be included with their default field values. Later when additional control is necessary to model a specific type of measure, the field values can be re-evaluated. The following input object allows you to control how you want the simulation to be performed. The input objects should appear in your file and appear in almost all of the example files:
-
SimulationControl - controls if the simulation is run for the weather file period and if sizing calculations are performed. You should become familiar with this input object since you may find it one that you frequently change during the Run-Check-Edit cycle.
Two other input objects should appear in your input file and are included in almost all example files:
Version - indicates what version of EnergyPlus is being used.
Building - includes fields for the name of the building, and the angle of the entire building compared to true north, as well as parameters related to the simulation that, in general, should be allowed to default.
For a new modeler, the following input objects may be omitted. They can be added later for special cases althought they and appear in almost all of the example files:
Timestep - the number of timesteps each hour and usually set to 6.
HeatBalanceAlgorithm - selects the algorithm used for simulating heat and moisture transfer through the surfaces of the building and usually set to ConductionTransferFunction.
SurfaceConvectionAlgorithm:Inside - selects the algorithm used for the inside face of the building surfaces and is usually set to TARP.
SurfaceConvectionAlgorithm:Outside - selects the algorithm used for the outside face of the building surfaces between interior and exterior conditions and is usually set to DOE-2.
These input objects and more are further explained in the InputOutputReference under the heading “Group-Simulation Parameters.”
Location and Climate[LINK]
Many of the fields in the group of input objects related to location, climate, and the weather file are ones that will be set once for each specific project.
Site:Location - describes the name, latitude, longitude and other parameters related to the location of the building. When using a weather file, the values from the weather file will be used instead. Predefined location objects may be found in the DDY file that accompanies most epw weather files.
SizingPeriod:DesignDay - the high and low temperature and humidities describing a design day that is used for sizing equipment. Two (or more) instances of this input object are frequently in a file, one for heating and one for cooling. The DDY file that comes with the weather file should include input objects that may be used here.
RunPeriod - the start and stop dates of the simulation and often set to the full year. When debugging a file, a shorter period of time can be used to speed up the simulation portion of the Run-Check-Edit cycle.
RunPeriodControl:SpecialDays - allows specfication of holidays and a good example can be seen in 5ZoneCostEst.idf.
RunPeriodControl:DaylightSavingTime - allows the specification of the start and ending period for daylight savings time. This will impact when schedules operate but please note that output reporting timesteps are always shown in standard time so schedules will shift an hour in the output when daylight savings time is active. A good example can be seen in 5ZoneCostEst.idf.
Site:GroundTemperature:BuildingSurface - for one of the ground temperature algorithms, specifies the average temperature for each month of the year. This temperature is applied directly to the outside face of surfaces which use the Ground outside boundary conditions. See Ground Heat Transfer in EnergyPlus in the Auxiliary Programs document for information about preprocessors. There are also other more integrated ground heat transfer options, see Site:GroundDomain:* and Foundation:Kiva.
Site:WaterMainsTemperature - input for the water temperatures supplied to the building from underground water mains and should be specified whenever water heaters are described. A good example can be seen in 5ZoneVAV-ChilledWaterStorage-Mixed.idf. If not specified, some default assumptions are used for the water temperature supplied to the building.
Other input objects in this group can help perform sizing using the weather file, override the sky temperature, impact the variation of outdoor conditions with building height (especially important for tall buildings), work with ground temperatures and ground heat transfer, override the precipitation in weather files, specify the irrigation for a green roof, and some advanced properties related to the light spectrum for window performance. These input objects and more are further explained in the InputOutputReference under the heading “Group-Location and Climate.”
Many aspects of building operation are characterized by timing whether it is the hours that a building is occupied or when the control systems are in various modes. Due to this, specifying when something occurs using the Schedule input objects becomes one of the most common things to do. It is important to coordinate schedules properly. The operation of office equipment in a space usually corresponds to occupancy of that space as does the thermostat set points and fan operation. Because schedules are such a key input for so many features of a building, a great deal of flexibility exists in EnergyPlus to specify them.
Schedule:Compact - The most commonly used method of specifying schedules and uses “Through” and “For” to reduce the amount of input required.
ScheduleTypeLimits - Every schedule input object includes a field that helps validate the limiting values for the schedule, and this input object describes the upper and lower limit.
Schedule:Constant - If the value of the schedule is the same every hour of the year, this input object is the easiest way to specify that value.
Schedule:File - At times, data is available from a building being monitored or for factors that change throughout the year. This input object allows a column of data from an external file to be referenced as the values of the schedule. A variation of this input object allows input specifically for shading.
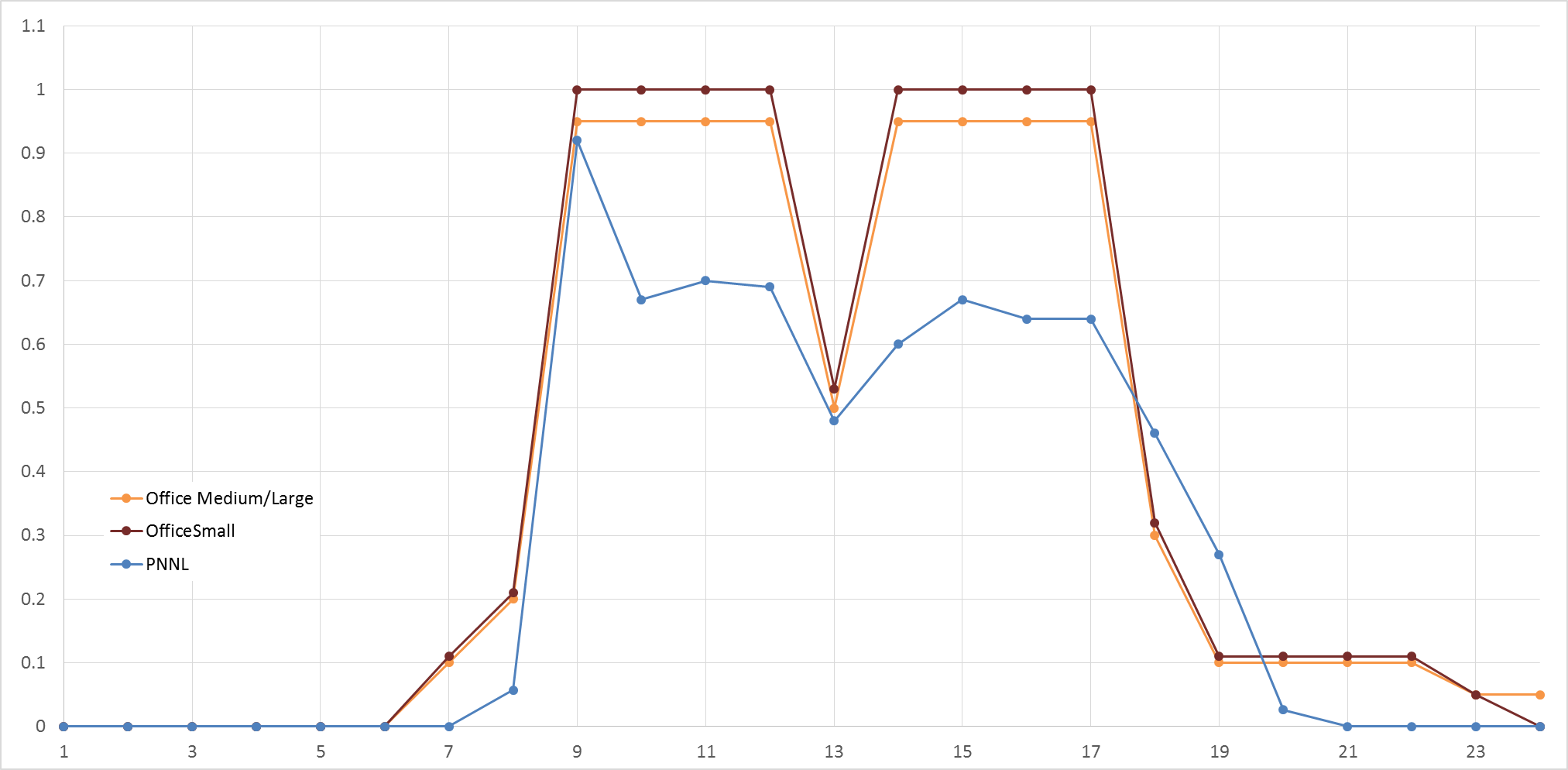
Other input objects in this input group allow specification of schedule values to be in different formats. These input objects and more are further explained in the InputOutputReference under the heading “Group-Schedules.”
Surface Construction Elements[LINK]
Specifying the physical properties of the building envelope is something every building model includes. The input objects in this group allow the specification of the different layers that make up exterior and interior walls, roofs, floors, windows, and skylights as well as the order of the materials in these surfaces. A large number of input objects appear in this group since there are many special features that need to be modeled for certain energy efficiency measures. The following is a list of only the most commonly used input objects.
Material - the most common input object to describe the materials used in opaque constructions in walls, roofs, and floors and includes inputs for the thickness, conductivity, density, and specific heat as well as absorptances. See examples in ASHRAE_2005_HOF_Materials.idf located in the DataSets folder.
Material:NoMass - used when the material only has thermal resistance and little thermal mass such as insulation. It should not be used to describe materials that do have significant thermal mass.
Material:AirGap - used to describe when walls or roofs have an air gap. Note, this is modeled as a fixed resistance (with no internal convection or radiant transfer), and it cannot be used for windows.
WindowMaterial:Glazing - describes the material used in the glass (or other transparent material) portion of the fenestration (windows and skylights). See WindowGlassMaterials.idf in the DataSets folder for examples.
WindowMaterial:Gas - the type of gas used between layers of glass in windows and skylights has a significant impact on the heat transfer performance. See WindowGasMaterials.idf in the DataSets folder for examples.
Construction - a list of materials (any from the list above plus others) in order from the outside to the inside making up the wall, roof, floor, window or skylight. Every input file will have several of these input objects. Examples of constructions for walls, roofs, and floors can be found in ASHRAE_2005_HOF_Materials.idf located in the DataSets folder while examples for windows and skylights can be found in WindowConstructs.idf in the same folder.
WindowMaterial:SimpleGlazingSystem - the best way to describe a window is with a construction input object that references WindowMaterial:Glazing and WindowMaterial:Gas input objects but if all you have is the U-Factor and Solar Heat Gain Coefficient (SHGC) they can be specified in this input object.
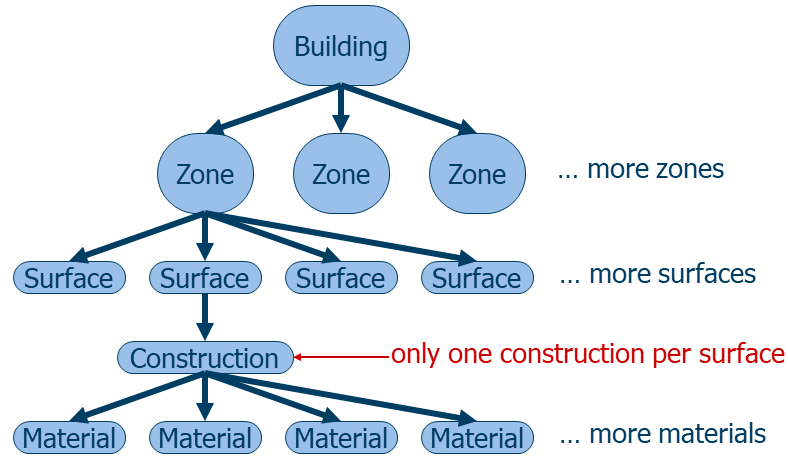
A large variety of input objects in this group are not as commonly used but are key to modeling specific types of walls and windows so if what you are trying to model does not fall into the neat categories for the input objects described so far, there is still a good chance that EnergyPlus has an input object that will work. These other input objects include ones for walls and roof that can be used when modeling combined heat and moisture transfer, modeling materials which undergo a phase change to store heat in the wall or when the material properties change with temperature, when the material allows infrared radiation to flow through it, when modeling green (vegetated) roofs, for simplified C- or F-factor modeling, or when the wall includes resistance or hydronic tubing to provide heat. The other input objects to describe windows and skylights include input objects that can be used to describe thermochromic and electrochromic glazing, mixtures of gases between layers of glass, vacuum glazing, movable portions of the window assembly such as shades and blinds and screens, alternative ways of specifying fenestration such as equivalent layers or refraction extinction method or ASHWAT model or from a WINDOW program export/data file or specifying wavelength-by-wavelength properties.
The input objects described in this section are further explained in the InputOutputReference under the heading “Group-Surface Construction Elements.”
Thermal Zones and Surfaces[LINK]
The physical aspects of the building such as the walls, roof, and windows, is one of the most important and often challenging aspects of creating a building energy model. In EnergyPlus, the surfaces define the geometry of each zone and thus for the entire building. For many, a graphical user interface will be used to help define the geometric aspects of the building energy model, and many of the input objects described in this section will be directly created by that interface program. It is still important to understand some of the details for these input objects because it is likely that you will be reviewing them as part of debugging error messages. EnergyPlus uses the three dimensional position of each corner of a surface to define the position and orientation of that surface so for a typical rectangular wall that represents 12 numbers and for a typical building with hundreds of surfaces that means thousands of numbers are used to define the geometry of a building so you can see why using an interface is so common.
EnergyPlus uses a right-hand coordinate system as shown in Figure X with three dimensions. The X-axis points east, the Y-axis points north, and the Z-axis points up.
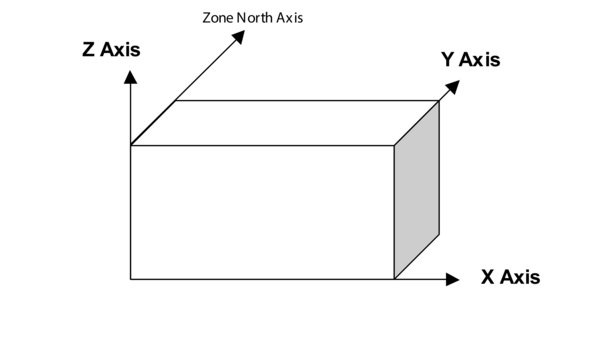
Zone - defines the name of the thermal zone as well as the ceiling height, floor area, and volume. For most zones that are fully enclosed these three entries can be calculated automatically be EnergyPlus and do not need to be entered. A zone multiplier allows a single zone to represent many identical zones (such as all the enclosed offices on one side of a building). The name of the zone will be referenced in many places in the input file so it should be clear what it is describing. When defining a zone, it is important for the entire area to be thermally similar both in heat being transferred through exterior walls as well as interior heat gains. But using as few zones as possible (and thus as few surfaces) also can result in faster simulations, so there is no reason to slow down the simulation just so two (or more) essentially identical areas are each simulated. The coordinates can be just set to zero if the world coordinate system is used (see GlobalGeometryRules below).
BuildingSurface:Detailed - lists the three-dimensional coordinates that define each corner as well as referencing the zone that the surface is attached to and the construction of the wall (list of materials). This input object supports any shape surface with three or more corners (vertices). In addition, this input object defines what is on the other side of the surface from the zone, whether that is outside, another zone in the building, or the ground. Other inputs indicate if the outside of the surface is exposed to the sun or the wind.
FenestrationSurface:Detailed - describes windows, doors, and special daylighting tubes and it references the wall that it is part of. It also requires the specification of vertices (usually four but three is also allowed) to describe the corners of the window or door as well as the construction which, in this case, is generally the layers of glass and the gas fill between the layers. It has a field for a multiplier although usually the multiplier is set to one since the position of windows matters to many of the algorithms used. In order to describe the frame of the window and any dividers that it might have, a separate input object (WindowProperty:FrameAndDivider) may be included and referenced. A good example file is WindowsTests.idf. To understand how to model the many options for windows, a section and a table in the Input Output Reference called “Window Modeling Options" should be examined.
Casting shadows on the building, especially onto windows, can significantly impact the energy use of a building, and EnergyPlus includes several input objects to model this effect. The largest impact of shading surfaces is to reduce solar gain through windows that are shaded. There are two kinds of shading surfaces in EnergyPlus, detached and attached. A detached shading surface, such as a tree or neighboring building, is not connected to the building. An attached shading surface is typically an overhang or fin that is attached to a particular base surface of the building, usually a wall; attached shading surfaces are usually designed to shade specific windows.
Shading:Site:Detailed - describes something near but not attached to the building that casts a shadow on the building such as nearby buildings or mountains and includes the vertex of one corner as well as the length and width. For deciduous trees, and other situations that shading changes over time, the schedule for the transmittance can vary, otherwise, it should always be set to zero or leave the schedule name blank.
Shading:Zone:Detailed - describes an attachment to the building that casts a shadow such as an overhang or fin. It also includes a reference to a transmittance schedule. The wall that the fin or overhang is attached to is also specified.
If using relative coordinates (see GlobalGeometryRules), you may also want to use the Shading:Building:Detailed input object since it will “rotate” with the building. Typically, Shading:Site:Detailed is used for things that are fixed at the site and don’t move with building rotation. Shading:Building:Detailed is for larger structures like a parking garage or canopy which aren’t associated with a specific zone but would likely rotate with the building.
EnergyPlus includes a bunch of variations on these basic surface input objects that map to a closer representation of real surfaces in buildings. These input objects are effectively just different ways to represent the same information as the BuildingSurface:Detailed, FenestrationSurface:Detailed, and Shading:Zone:Detailed input objects. These input objects are seldom created by graphical user interfaces, so it is unlikely that you will see them. Some of these input objects also have simpler methods for specifying geometry, such as using a single vertex, height, width, tilt, and azimuth or just specifying the fin location relative to the window edge. The following is a list of these input object variations for surfaces:
Wall:Detailed, Wall:Exterior, Wall:Adiabatic, Wall:Underground, Wall:Interzone
RoofCeiling:Detailed, Roof
Floor:Detailed, Floor:GroundContact, Floor:Adiabatic, Floor:Interzone
Ceiling:Adiabatic, Ceiling:Interzone
Window, Window:Interzone
Door, GlazedDoor, Door:Interzone, GlazedDoor:Interzone
Shading:Site, Shading:Building, Shading:Overhang, Shading:Overhang:Projection, Shading:Fin, Shading:Fin:Projection
GlobalGeometryRules - A required input object that should be in all files. It sets the way geometry is specified for all of the surface input objects. The most common approach is that the order of coordinates for each surface should start with the upper left corner (when viewed from “outside” the zone with the surface) and that the coordinates should proceed in a counter-clockwise order. In addition, most common is to use a world coordinate system where all the vertices are based on a single coordinate system for the entire building rather than one that changes relative to each zone. However, if you want to rotate the building, then you must specify Relative coordinates, and the zone origins may all remain at (0,0,0).
WindowShadingControl - for a window, describes the kind of movable shading (interior shade, interior blind, between glass shade, exterior blind, etc..) as well as how it is controlled and the physical material of the shade or window construction with the shade. Good examples are in the PurchAirWithDaylightingAndShadeControl.idf file.
WindowProperty:FrameAndDivider - defines the frame material around a window and any dividers between separate lites of the window (see Figure X). While a window does not necessarily need to define the frame, it is a more accurate approach since the heat transfer through the frame usually has significant impacts the overall performance of a window. Note that the area of the Fenestration:Detailed object is the glazed area without the frame. The frame extends beyond the glazed area. See the PurchAirWithDaylighting.idf example file.
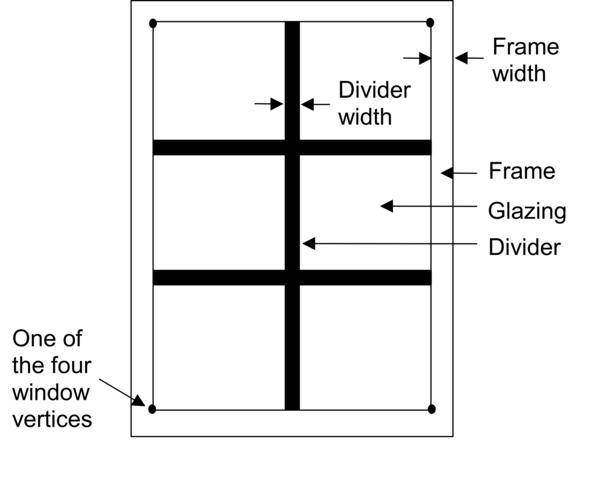
WindowProperty:AirflowControl - defines windows that have forced air flow between the panes of glass, also called heat-extract windows or climate windows. See the example file AirflowWindowsAndBetweenGlassBlinds.idf.
WindowProperty:StormWindow - allows the definition of a movable storm window that is usually applied to a window in the winter. See the StormWindow.idf example file.
InternalMass - used to define thermal mass that is not described anywhere else in the model - often used to capture the effect of furnishings or interior floors that are not being modeled. Used in many example files including RefBldgLargeOfficeNew2004_Chicago.idf.
ShadingProperty:Reflectance - specifying the reflectance properties for shading and is only needed if the input object Building specifies the “with reflections” option. See the ReflectiveAdjacentBuilding.idf example file.
Other less common input objects include ZoneList and ZoneGroup that can be used when doing multi-story simulations and GeometryTransform which allows a building model to be stretched with just a few inputs.
Internal Gains[LINK]
Inside a building, people, appliances, office equipment, lighting, and other devices produce heat. The combination of all these items that produce heat within a building are called internal gains and represents a significant contribution, sometimes the largest contribution, to the cooling requirements for a building. In addition, they offset the amount of heat from the HVAC system that is needed at a given time. Typically, the peak value is entered in the input objects for this group such as the maximum number of people, the total power of equipment, or the total lighting power and then a schedule is used to modify that value each hour of the year. It is just as critical that the schedule values are realistic for your building as is the peak value. For almost all buildings, it is rare that the peak occupancy occurs for more than a few hours per year if at all and this is especially the case for retail stores, theaters, and sports complexes. Even office buildings when counting vacations and people out of the building for meetings will rarely have peak occupancy.
The most common internal gain input objects that are shown in almost all the example files are:
People – specifies not only the sensible, latent and radiant heat from people but also includes ways of reporting the comfort of occupants using a variety of thermal comfort models. The DynamicClothing.idf example file shows how to use the thermal comfort models.
Lights – describes the heat related to lighting systems.
ElectricEquipment – describes the heat related to electrical appliances, office equipment, and other heat sources that are powered by electricity.
GasEquipment - specifies the heat related to cooking appliances and other equipment that uses natural gas.
Less common internal gains input objects include:
OtherEquipment - describes any heat gain or loss (sensible, radiant, and/or latent) that impacts the space but does not consume utility energy in the simulation. Typically used to model a process load which is not to be included in the overall building energy consumption.
ElectricEquipment:ITE:AirCooled - see the 1ZoneDataCenterCRAC_wApproachTemp.idf example file.
SwimmingPool:Indoor - see the 5ZoneSwimmingPool.idf example file.
Other
-
ComfortViewFactorAngles – allows the specification of how different surfaces impact the thermal comfort calculations for the occupants. See the PurchAirWithDaylightingAngleFac.idf example file.
The Internal Gains group also contains input objects related to zone contaminant sources and sinks. The input objects include modeling components that impact contaminant concentrations which are scheduled, pressure driven, use a cut off model, assume a decaying source, surface diffusion, or using a deposition velocity model. The input objects described in this section are further explained in the InputOutputReference under the heading “Group-Internal Gains.”
Reducing the amount of powered lighting that is used when sufficient natural daylight illuminates the interior building through windows and skylights is called daylighting. Automatics daylighting control systems are a very common energy efficiency measure in buildings and are often required for new building designs depending on the energy code that applies to the building location. The most common input objects related to daylighting are:
Daylighting:Controls – specifies the algorithm used for daylighting, the dimming of lights is continuous or stepped, and how glare calculations are performed.
Daylighting:ReferencePoint – specifies the location of the sensors for the daylighting control system.
The InputOutputReference includes not only a description of these input objects but also extra guidance on how they should be applied. The PurchAirWithDaylighting.idf contains examples of these input objects.
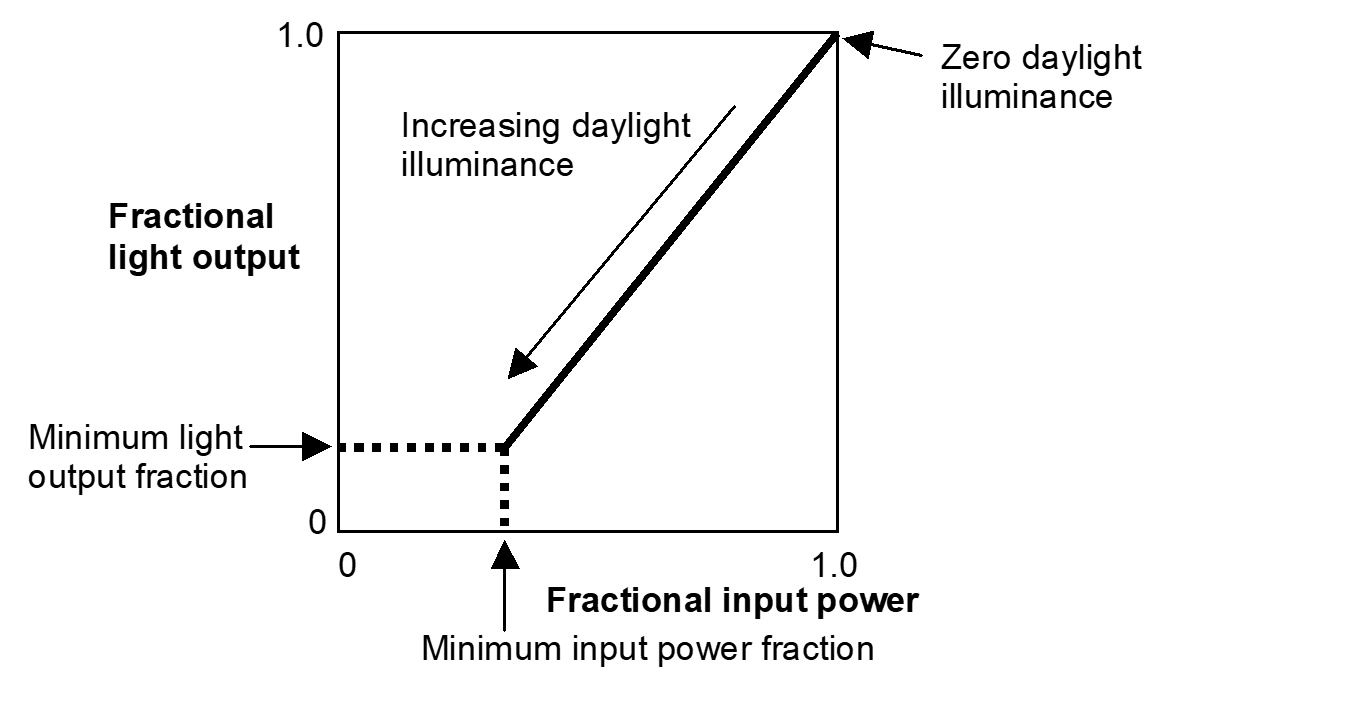
Three different devices can be used with daylighting:
An input object called Daylighting:DELight:ComplexFenestration is used with one of the two control methods specified in the Daylighting:Controls input object when used in conjunction with complex fenestration systems such as prismatic and holographic glass.
Some flexibility is given to provide extra output related to daylighting and includes:
Output:DaylightFactors – creates a special report on the factors used in daylighting. See the ReportDaylightFactors.idf example file.
Output:IlluminanceMap – allows the generation of maps of illuminance values within each interior zone that uses daylighting controls. The exact file format can be set using the OutputControl:IlluminanceMap:Style input object. See the DaylightingDeviceTubular.idf for example of both input objects.
More details of these output options can be found in the OutputDetailsAndExamples document. The input objects described in this section are further explained in the InputOutputReference under the heading “Group-Daylighting.”
Advanced Construction, Surface, Zone Concepts[LINK]
The group of input objects contains many special cases for more sophisticated modeling for constructions, surfaces, and zones. As part of this, one of the ways to model building foundations called Kiva is described. See the ZoneCoupledKivaBasement.idf and ZoneCoupledKivaSlab.idf example files for example of these input objects.
Foundation:Kiva - describes the insulation depth and width for interior and exterior horizontal and vertical insulated foundations as well as the construction for the wall footing, see Figure X .
Foundation:Kiva:Settings - sets the soil conditions and other parameters related to the Foundation:Kiva input object.
SurfaceProperty:ExposedFoundationPerimeter - used to set the portion of the foundation that is along the exterior perimeter of the building that undergoes heat transfer with the environment. Edges of underground surfaces that are fully under the building and not along the perimeter are not expected to have any heat transfer with the environment.
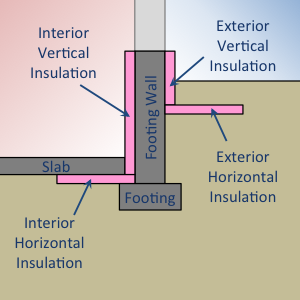
Input objects of interest in this group not related to Kiva include
SurfaceControl:MovableInsulation - allows the modeling of insulation panels that are removable for walls, floors, and roofs but not windows. See MovableExtInsulationSimple.idf and MovableIntInsulationLightsLowE.idf example files.
SurfaceProperty:Underwater - allows the outside of the building to be modeled as underwater and even as moving through the water allowing EnergyPlus to model vessels. See the VaryingLocationAndOrientation.idf example file.
SurfaceProperty:ExteriorNaturalVentedCavity - provides a method to include the modeling of baffles in the multi-skin exteriors. See the HP_wICSSolarCollector.idf example file.
Other input objects in this group set the heat transfer algorithms for specific surfaces to override the building level heat transfer algorithm, when other models are used to describe the variation in temperature on the outside of a surface, override the algorithm used for modeling convection heat transfer between the air inside or outside of a zone and the surface, vapor transfer coefficients when using algorithms that include moisture modeling of surfaces, override the algorithm that distributes the solar radiation on interior surfaces, overrides the solar energy absorbed by different layers for complex windows, a way to override the longwave radiation with other surfaces in the zone, allows overriding the external environment for a surface or a zone including solar shading or airspeed or temperature or humidity, overrides the source term for the heat balance, or overrides the view factors for a zone. The input objects described in this section are further explained in the InputOutputReference under the heading “Group-Advanced Surface Concepts.”
Exterior Equipment[LINK]
While equipment that is outside of a building does not impact the thermal performance of the building, the accounting of all end-uses including those outside of the building is important for many compliance and incentive programs that require building energy modeling. See the ExteriorLightsAndEq.idf example file for these input objects.
Exterior:Lights - describes the external site lighting for the building grounds, entrances, and facades which are either controlled by a schedule or when the sun is set.
Exterior:FuelEquipment - describes other energy consumption on the site that is external to the building other than lighting.
Exterior:WaterEquipment - describes the flow rate of water use on the building site outside of the building.
The input objects described in this section are further explained in the InputOutputReference under the heading “Group-Exterior Energy Use Equipment.”
The Zone Airflow input object group provides a way to model the airflow between zones and airflow due to natural ventilation (e.g., open windows) or mechanically-induced ventilation (e.g., exhaust air fans).
ZoneInfiltration:DesignFlowRate - provides a way to describe the air infiltration into a building through leaks in the envelope including around windows or the normal operation of doors. The leakage can be a function of temperature and wind speed and can be expressed as either a total flow rate, a flow rate per floor area, per wall area, or as an air change rate. This input object appears in most example files.
ZoneInfiltration:EffectiveLeakageArea - similar to the previous input object but uses a different equation to express the infiltration rate. The DirectIndirectEvapCoolers.idf file contains an example.
ZoneInfiltration:FlowCoefficient - also similar to the ZoneInfiltration:DesignFlowRate input object but uses yet a different equation.The DirectIndirectEvapCoolers.idf file contains an example.
ZoneVentilation:DesignFlowRate - a method to add outside air to a zone with similar inputs to the ZoneInfiltration:DesignFlowRate but this would represent a purposeful introduction of outdoor air into the space. See the 5ZoneNightVent2.idf example file.
ZoneVentilation:WindandStackOpenArea - describes the natural ventilation driven introduction of outdoor air into the zone using a simpler method than an AirflowNetwork model. The inputs include the opening area and effectiveness as well as simple controls based on zone or outdoor temperature or the difference between the two or wind speed. See the VentilationSimpleTest.idf file.
ZoneMixing, ZoneCrossMixing, and ZoneRefrigerationDoorMixing - these three input objects provide simplified treatments of air exchange between zones.
ZoneEarthtube - provides a way to model an earth tube which is a way to draw outdoor into the zone through an underground pipe in order to cool the air in the summer and heat it in the winter. An example of this input object is in the EarthTubeSimpleTest.idf file.
ZoneCoolTower:Shower - models a passive downdraught evaporative cooling tower (sometimes also called a shower cooling tower or a wind tower) using natural ventilation and water evaporation to providing cooling in typically arid climates. See the CooltowerSimpleTestwithVentilation.idf for an example of this input object.
ZoneThermalChimney - models a passive solar driven thermal chimney that utilize the buoyancy of air heated by the sun to provide ventilation. See the file ThermalChimneyTest.idf.
ZoneAirBalance:OutdoorAir - calculates the combined outdoor airflow including the interactions between mechanical ventilation, infiltration, and duct leakage and is usually applied to residential buildings. See the SingleFamilyHouse_TwoSpeed_ZoneAirBalance.idf file for example.
The input objects described in this section are further explained in the InputOutputReference under the heading “Group-Airflow.”
HVAC Templates[LINK]
New users to EnergyPlus need to learn many things to understand how to create detailed input objects for modeling an HVAC system. In order to reduce this initial effort, HVACTemplates were created. Unlike other input objects, the HVACTemplate input objects are not directly processed by EnergyPlus; instead, a preprocessor called ExpandObjects turns these HVACTemplate input objects into the detailed HVAC input objects. This can be used as a learning tool since you can review the .expidf file that contains the detailed input objects or it can be used for long term modeling especially if your focus is not on HVAC related energy efficiency measures. The primary disadvantage of using the HVACTemplate input objects is that only a small subset of possible configurations can be modeled using them; however, the subset of configurations supported by the HVACTemplate input objects was carefully chosen to be some of the most common HVAC configurations. If the HVACTemplate input objects do not support the HVAC configuration you are considering; you need to model it with the detailed HVAC EnergyPlus input objects. When using HVACTemplate input objects, no regular EnergyPlus input objects related to HVAC should be used (see the InputOutputReference for some exceptions to this). The HVACTemplates can model:
Baseboard heating systems with optional hot water boiler
Fan coil systems with boilers and chillers
Packaged terminal air conditioner (PTAC) system with optional hot water boiler
Packaged terminal air-to-air heat pump (PTHP) systems
Water to air heat pumps with boiler and cooling tower
Variable refrigerant flow heat pumps (air-to-air)
Variable refrigerant flow heat pumps (water-to-air) with boiler and cooling tower
Direct-expansion (DX) cooling, package and split systems
Direct-expansion (DX) heat pump systems
Packaged variable air volume system using direct-expansion cooling
Variable air volume systems with boilers and air-cooled chillers
Variable air volume systems with boilers and water-cooled chillers
Constant air volume systems with boilers and water-cooled chillers
Dual-duct systems (constant or variable air volume) with boilers and water-cooled chillers
Dedicated outdoor air systems (DOAS) combined with zonal template systems
The Input Output Reference includes a list of exactly which input objects are needed for each of these configurations
In addition, this group of input objects includes three plant input objects that allow the referencing of chillers, towers, and boilers respectively so that additional details can be described in those input objects. Example for these are in the ExampleFiles directory and start with the name HVACTempate. All of these are described in the “Input/Output Reference” document under the Group “HVACTemplates” and please note that this group is described in Chapter 2 while most of the other groups of input objects are described in Chapter 1. The expansion process is described in the Auxiliary Programs document under “ExpandObjects.”
Detailed HVAC[LINK]
In buildings, HVAC systems are comprised of components such as fans, pumps, coils, chillers and boilers connected by ducts or pipes and controlled by systems using sensors strategically located in the distribution systems and in the zones. In many respects, EnergyPlus mirrors this topology by having a large number of components and a means to describe their connections with one another and their control systems. Every component in an HVAC system must have an inlet and outlet “node.” In the actual system, a node might be a point in the system at which fluid properties can be measured. In an EnergyPlus simulation, the nodes are points at which fluid properties are evaluated and passed on to subsequent equipment. Components are linked together to form various loops within the simulation. Thus, the output node from one component also serves as the inlet node to the next component. Loops are constructed combining the components as well as input objects the describe the arrangement of the components. The figure below shows a generic example of the loop-node concept. Loop nodes are a key defining feature in EnergyPlus. As a result, it is recommended that one of the first steps taken in defining an HVAC system in EnergyPlus be the definition of a node diagram or map. This is helpful for visualization of the entire system.
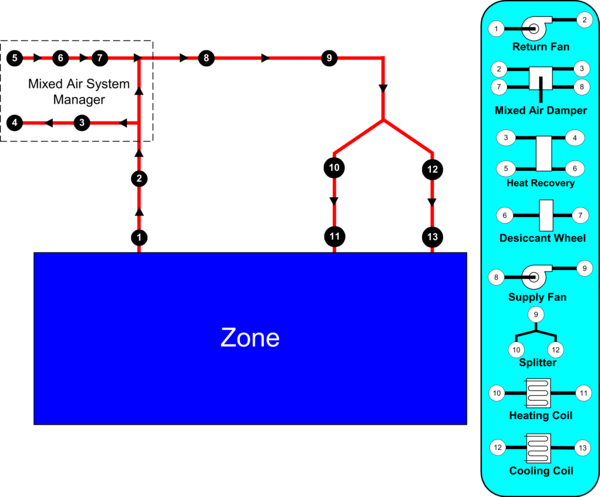
So that these loops are manageable and more clearly defined both in the input and in the simulation, four different loop sections can be defined in an EnergyPlus input file. In general, these four types are in essence two pairs of loop sections that make up two distinct types of loops: a zone/air loop and a plant loop.
Air Loop Supply Side: The air loop is defined by the section of the zone/air loop that starts after the zone return streams are combined and continues on until just before any air stream(s) are branched off to individual zones. The starting point of the air loop is fairly straightforward. The ending point is slightly more complex but can be understood with some examples. For instance, in a terminal reheat system, the end of the air loop would typically be considered the node following the cooling coil. In a dual duct system, the air loop would have two ending points that would correspond to the nodes after the cooling coil and after the heating coil/humidifier. In most cases, the air loop has a single starting point and up to two ending points (for a two-deck system). An outdoor air subsystem can be included in the supply side for ventilation and relief air.
Air Loop Zone Equipment: The zone equipment section of the input file is defined as more or less the rest of the zone/air loop (outside air is handled separately as a subset of the air loop). This includes everything from where the ducts are split to serve various zones up through where the return ducts from various zones are mixed into a single return duct. Zone equipment can include dampers and reheat coils as well as zone-specific conditioning systems such as thermostatic baseboard or a window air conditioner. Most control issues are typically dealt with in the zone equipment section of the simulation.
Plant Loop Demand Side: One side of the plant is where energy is “demanded” by various components that make up the air loop or zone equipment. Typically, this is the water side of equipment such as coils, baseboard, radiant heating and cooling, etc. In the case of a condenser loop, energy is typically “demanded” by a chiller condenser or other water source heat pump. The demand side of this loop can also include a splitter, a mixer, and a bypass.
Plant Loop Supply Side: The other side of the plant loop is where energy is “supplied” by various components. The components typically found on the supply side include pumps, boilers, chillers, purchased heating and cooling, ice storage, etc. In the case of a condenser, the components would be a cooling tower, fluid cooler, or ground source heat exchanger, etc. As with the demand side, this loop can also include a splitter, a mixer, and a bypass.

The following is a list of groups of input objects related to specifying detailed HVAC systems in EnergyPlus related to zone equipment and secondary systems:
HVAC Design Objects - describes input objects related to how EnergyPlus performs autosizing for air terminals, zone equipment, systems, and plant components as well as for outdoor air systems.
Node-Branch Management - used to describe some of the topological features of EnergyPlus such as nodes, pipes, and ducts as well as branches (pieces of loops) and connectors.
Air Distribution - describes the arrangement of the components in an air distribution system includes the outdoor air system, splitters, mixers, and plenums.
Zone HVAC Controls and Thermostats - input objects related to thermostats and humidistats used to control the conditions in a zone.
Zone HVAC Forced Air Units - defines input related to zone forced air equipment like window air conditioners, packaged terminal air conditions (PTAC), unit heaters, fan coil systems, and outdoor air units as well as other related input objects.
Zone HVAC Radiative/Convective Units - models baseboard systems, low- and high-temperature radiant systems, and active portion of ventilated slabs.
Zone HVAC Air Loop Terminal Units - describes air terminals including constant volume, variable volume, series and parallel powered induction units, and duel duct terminals.
Zone HVAC Equipment Connections - used to describe the HVAC equipment connections at the zone level.
Fans - describes constant volume, variable volume, exhaust fans as well as more system and component model fans.
Coils - contains a long list of input objects to model heating and cooling water coils; heating and cooling DX coils including two-, multiple-, and variable-speed units; variable refrigerant coils; fuel and gas coils; desuperheater coils; air to water heat pump coils; and other coil input objects.
Evaporative Coolers - describes direct and indirect evaporative coolers.
Humidifiers and Dehumidifiers - for electric and gas steam humidifiers as well as desiccant dehumidifiers.
Heat Recovery - models for air-to-air flat plate and combined sensible and latent heat exchangers as well as heat exchangers coupled with desiccants.
Unitary Equipment - describes unitary input objects that are generally placed in the primary air loop and includes heating only, heating and cooling, and air-to-air heat pump input objects.
Variable Refrigerant Flow Equipment - input objects to describe variable refrigerant flow (VRF) equipment as well as the controls.
The following is a list of control systems in EnergyPlus related to HVAC
Controllers - input objects for simple controllers that look at a single node and compare it with the setpoint and includes controllers for water coils, outdoor air, and mechanical ventilation.
System Availability Managers - these input objects can take an input from any node and control whether an entire portion of the HVAC system is active and can be based on temperature, differential temperature, schedules, night cycle, and ventilation.
Setpoint Managers - these take input from any node or nodes and calculate a setpoint at another node and include controls for single zone heating, cooling, or reheat; humidity control; mixed air; warmest or coldest; and many other scenarios.
Plant-Condenser Control - provides control for the plant loop primarily controlling the operation of the loop and which equipment is available and includes control based on heating or cooling load and in reference to outdoor conditions such as dry-bulb or wet-bulb temperature.
Plant-Condenser Flow Control - describes the TemperingValve input object for the special case of flow control with thermal storage systems.
The following is a list of input objects related to primary systems and equipment:
Pumps - describes constant speed and variable speed pumps and headered multiple pump systems.
Plant-Condenser Loops - describes the supply and demand side of the loops the operating temperatures and flow rates.
Plant Heating and Cooling Equipment - used to input the central plant equipment such as steam and hot water boilers; electric, absorption, engine driven, and turbine chillers; and water-to-water heat pumps; as well as connections to district heating and cooling sources.
Condenser Equipment and Heat Exchangers - describes single-, two, and variable speed cooling towers; single and two speed evaporative and non-evaporative fluid coolers; vertical, surface, trench and slinky ground heat exchangers; and fluid-to-fluid heat exchangers.
Non-Zone Equipment - describes the LoadProfile:Plant input object that allows the load on the plant to be specified by schedule if already known.
User Defined HVAC and Plant Component Models - a group that allows the user to define custom models for zonal systems, air terminals, coils, and plant equipment.
The input object groups described in this section are further explained in the InputOutputReference.
Output Reporting[LINK]
The primary goal of modeling is seeing the results of the model contained in the output reporting. EnergyPlus has several different types of outputs, but initially the most important to understand are the tabular output reports that summarize the results of the simulation. The Output:Table:SummaryReports and OutputControl:Table:Style input objects described below are the only two necessary to start generating the tabular output reports:
Output:Table:SummaryReports - allows the specification of different tabular reports but usually just specifying AllSummary is necessary. Additional reports can be shown by specifying AllSummaryAndMonthly, AllSummaryMonthlyAndSizingPeriod.
OutputControl:Table:Style - specifying the output format for the tabular reports which is most commonly HTML but a comma, tab, fixed width, and XML options are also available. Depending on what is specified the output reports can have different file extensions and the file name usually has the word “Table” or “tbl” in it.
You can also create your own custom tabular reports by using one of the following input objects:
Output:Table:TimeBins - shows the amount of time in hours that occurs in different bins for the single specific output variable or meter specified
Output:Table:Monthly - shows a series of output variables or output meters on a monthly basis using different aggregation schemes. For output variables that reoccur for each zone or other input objects, the monthly report will be repeated for each one.
Output:Table:Annual - shows a series of output variables or output meters on an annual basis using different aggregation schemes. For output variables that reoccur for each zone or other input objects, additional rows of results will be displayed.
Output:VariableDictionary - provides a list of available output variables for use with these custom tabular reports as well as the time step reporting described next. The list of output variables that are available for specific simulation appear in a file with a .rdd extension, and the output meters appear in a file with a .mdd extension.
When you need to dive deeper into the results for a specific output variable or output meters, time step outputs allow you to see the values of an output variable for each timestep or other time periods. By looking at multiple output variables and seeing how they change together over time, a deeper understanding of the system and control operation can be gained.
Output:Variable - these input objects are added one for each output variable desired. Usually, an asterisk is used for the “key value” field so that all instances of the output variable are included. The output shows up in the .eso file which is generally converted to a .csv file for use with a spreadsheet.
Output:Meter and Output:Meter:MeterFileOnly - these input objects specify the output meters (think of them as very detailed submeters). The output from these input objects show up in the .mtr file which is generally converted to a Meter.csv file for use with a spreadsheet. Also, note that the .mtd file shows the exact relationship between specific end-use output report variables and each output meter.
Output:SQLite - use this input object if you want to output in the SQLite database format. Not only can the output variables and meters be in SQLite format but the tabular reports are also included.
EnergyPlus also includes a number of special reports that usually appear in different output files or in the .eio output file
Output:Surfaces:List - provides a report on all the surfaces in a file and the output appears in the .eio and .sln output files.
Output:Surfaces:Drawing - provides a DXF drawing that can be opened in some CAD programs .
OutputControl:SurfaceColorScheme - controls the colors used in the DXF file.
Output:Schedules - provides a summary of the schedules in the input file and appears as part of the file with the .eio extension.
Output:Constructions - provides a summary of constructions in the input file and appears as part of the file with the .eio extension.
Output:EnergyManagementSystem - creates a list of detailed output related to the energy management system in a file with the .edd extension.
OutputControl:ReportingTolerances - provides more control over the amount of time reported for the setpoints not being met.
Output:Diagnostics - provides additional detail in the output messages in the .err file . Normally this extra detail is not shown to reduce confusion for new users.
Output:DebuggingData - provides an additional detailed output related to HVAC nodes in a file with a .dbg extension.
Environmental reporting adds new meters showing the emissions related to the building and is triggered by the use of the following three input objects. See the 5ZoneTDV.idf file for examples.
Output:EnvironmentalImpactFactors - specifies the frequency of the output variables related to emissions.
EnvironmentalImpactFactors - specifies the efficiency of district heating and cooling systems as well as the carbon equivalent emission factors for N20, CH4, and CO2.
FuelFactors - for each type of energy resource (electricity, natural gas, etc..) provides a way to enter factors related to source energy and emissions of CO2, CO, CH4, NOx, N20, SO2, PM, NH3, NMVOC, Hg, Pb, and other factors.
Other input objects in this group allow the accumulation of metered results, the combination of output variables or meters to create custom meters, and a method for preprocessors to include error messages in the normal error file. Many example files contain some of these input objects. All of these are described in the “Input/Output Reference” but note that this group is described in Chapter 5 “Input for Output” and Chapter 7 “Standard Output Reports” while most of the other groups of input objects are described in Chapter 1. The OutputDetailsAndExamples documentation provides even more details on the outputs created by each of these input objects. Several other output related input objects appear in other areas such as Output:DaylightFactors input object in the Daylighting group.
EnergyPlus contains several input objects that allow economic analysis to be performed. When these input objects are included in the input file, new tabular output reports are automatically generated. The input objects used by EnergyPlus for cost estimating calculations are as follows:
ComponentCost:LineItem - provides inputs related to determining the construction cost and can be associated with several different input objects and the cost estimate is based on factors such as cost per area or cost per unit of output capacity. It has not been applied to all types of input objects so for many scenarios; construction costing would need to be performed outside of EnergyPlus.
ComponentCost:Adjustments - allows the specification of adjustments including miscellaneous costs per conditioned area, design and engineering fees, contractor fees, contingency, permitting, bonding, and insurance as well as commissioning and regional adjustment fees.
ComponentCost:Reference - entry of reference building costs so that the current model can be compared to the reference building.
For many building projects, while energy estimates are important, the computation of estimated utility bills provides an understanding of how much money is going to be saved to help offset possibly higher initial costs of a high-performance building. Due to the many different utility companies and regulatory agencies, the approach used to compute monthly utility bills has become widely varied and, at times, quite complicated depending not only on energy and demand but the timing of each and the relationship between the two. Overall, the goals of the UtilityCost input objects of EnergyPlus are to make simple tariffs easy to model and complex tariffs possible to model. The 5ZoneEconomicsTariffAndLifeCycleCosts.idf example file provides several different example tariffs. The input objects used by EnergyPlus for the calculation of monthly and annual utility bills are as follows:
UtilityCost:Tariff - sets the parameters for the overall tariff such as associated output meter, conversion factors, demand computation, monthly charges, and minimum charges, and schedule names for the time of use periods, seasons, billing cycle, and real-time pricing.
UtilityCost:Qualify - provides a method to qualify if a tariff applies to the building being modeled since utilities provide limits usually based on peak demand or energy consumption for each tariff.
UtilityCost:Charge:Simple - defines cost per unit value for a charge based on energy or demand or other charges for a specific season. The charges are arranged in a hierarchy shown in Figure X Hierarchy of Economic Charges.
UtilityCost:Charge:Block - defines a more complicated but common type of charge for energy or demand where the costs are defined in the tariff with blocks of charges (i.e., the first 1000 kWh is one cost per kWh, the next 5000 kWh is a second cost, and remaining kWh is a third cost). Like UtilityCost:Charge:Simple, the charges use the same hierarchy.
UtilityCost:Ratchet - some utilities charge not only for the current month’s demand but also compensate for the highest demand in recent months, and this input object allows the specification of such a structure.
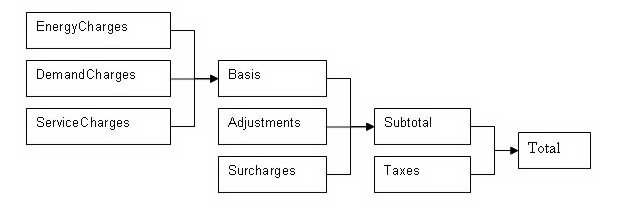
The following two input objects are uncommon to use:
UtilityCost:Variable - allows the specific specification of a monthly variable to be used in the calculation of the tariff.
UtilityCost:Computation - provides the step-by-step specification of the steps needed to compute the tariff. The output report tariff summary includes the default computation steps for the input objects specified.
Life-cycle costing allows the combination of initial and future costs (typically energy bills) to be understood using a single metric so that multiple building energy models can be compared even if they all have different initial and future costs. The input objects used for performing a life-cycle cost analysis are:
LifeCycleCost:Parameters - describes the discount, tax, and inflation rates, the approach used for inflation and discounting, as well as the base date and length of the study period and other parameters related to life-cycle costing.
LifeCycleCost:RecurringCosts - used to enter reoccurring costs other than costs related to energy and water usage since those are included automatically.
LifeCycleCost:NonrecurringCost - used to enter costs that occur only once during the study period.
LifeCycleCost:UsePriceEscalation - specifies the annual escalation of energy costs in future years and is generally based on government predictions. The increases in energy costs for future years are assuming they change differently than inflation. A file that is updated each year begins with the name LCCusePriceEscalationDataSet is included in the DataSets directory and is based on supplements to the NIST 135 handbook.
Two less commonly used input objects are
LifeCycleCost:UseAdjustment - allows manual adjustment of energy or water costs in future years.
CurrencyType - specifies the currency symbol of the monetary unit. If it is not included a dollar sign ‘$’ is used in all reports.
All of these are described in the “Input/Output Reference” but note that this group is described in Chapter 3 “EnergyPlus Economics” while most of the other groups of input objects are described in Chapter 1. The OutputDetailsAndExamples documentation provides even more details on the tabular outputs created in the section labeled “eplustbl.<ext>”.
The previous sections describe major groups of input objects. This section briefly covers some of the remaining input object groups.
Detailed Ground Heat Transfer - provides an alternative way of describing ground heat transfer through basement walls and floors and slabs using input objects that are then processed by the SLAB and BASEMENT programs and is also documented in AuxiliaryPrograms.
Energy Management System (EMS) - a high-level control method that connects sensors and actuators with a simple control programming language and is also documented in the EMSApplicationGuide.
External Interface - allows the connection of EnergyPlus using co-simulation by the import of Functional Mockup Units (FMUs) and is also documented in the ExternalInterfacesApplicationGuide.
Operational Faults - provides for the modeling of operation problems in sensors, controllers, meters, equipment, and systems and is commonly used with existing buildings.
General Data Entry - contains the Matrix:TwoDimension input object used with the Construction:ComplexFenestrationState input object.
Performance Curves - allows the specification of polynomial curves used to characterize the performance of HVAC equipment.
Performance Tables - allows the specification of tables used to characterize the performance of HVAC equipment.
Fluid Properties - describes the detailed properties of refrigerants and glycols.
Demand Limiting Controls - provides a way of implementing management of the systems of the building to regulate the peak demand.
Natural Ventilation and Duct Leakage - provides a way to model multizone airflows driven by wind and forced air systems (shown under Group-Airflow Network in the InputOutputReference).
Room Air Models - allows the description of non-uniform room air temperatures (not fully mixed).
Compliance Objects - provides an input object that allows rotation of the building when used for compliance purposes.
Parametrics - allows for simple parametric cases to be defined within an input file using input objects. Makes use of the ParametricPreprocessor as described in the AuxiliaryPrograms document.
Refrigeration - describes supermarket and warehouse refrigeration systems.
Electric Load Center-Generator Specifications - allows the specification of fuel and photovoltaic generators and controls on when they should be used to provide power to the facility.
Water Systems - contains input objects to describe the use of water in the building including from wells, rain, and storage.
Solar Collectors - describes various systems that convert solar energy into thermal energy including those that are integrated with photovoltaic systems.
Water Heaters and Thermal Storage - describes systems that provide water heating and storage as well as ice and chilled water storage.
Introduction[LINK]
The following background on building energy modeling (BEM) will provide a foundation before learning the essentials of EnergyPlus. If you are already familiar with BEM, you may wish to skip to Section 1.4 describing the EnergyPlus QuickStart Guide.
What is BEM?[LINK]
According to the BEM Library:
Some other terms that are used to describe the same topic are:
Building Simulation
Building Performance Simulation
Building Energy Simulation
Building Performance Modeling
Somewhat confusing, the term “model” can refer to both the specific building being described and analyzed as well as referencing the software for implementing a specific component of the building such as a wall or chiller.
To learn more about building energy modeling consider reviewing the following resources:
2017 ASHRAE Handbook - FundamentalsChapter 19 Energy Estimating and Modeling Methods
BEM Libary
IBPSA, IBPSA-USA, and YouTube videos
Numerous books
ASHRAE Standard 209 Energy Simulation Aided Design for Buildings Except Low-Rise Residential Buildings
Study materials for the ASHRAE Building Energy Modeling Professional (BEMP) or AEE Building Energy Simulation Analyst (BESA) professional certifications
Building energy modeling is necessary to understand the overall energy consumption in buildings, because, the energy flows in buildings can be very complicated. The heat flow through walls is determined not just by the area and the temperatures, but the mass characteristics of the walls may result in heat flowing out of a wall several hours after it has flowed in. The constantly changing temperature on the outside of the wall and the less frequent but often large step changes in thermostat setpoints between day and night operation for the inside of the building make the direction of the heat flow vary over time. Solar energy is absorbed on the exterior wall and roof surfaces as well as entering windows. The intensity of solar energy varies by the sun position for each period of time over the day and over the year. Heat sources within the building including people, office and other equipment, and lighting include both heat that immediately impacts the air within (convective heat) and heat that is absorbed by the surfaces and released slowly over time (radiant heat). Lighting may be controlled by a sensor that turns it on or off or changes its intensity based on the amount of natural daylight that is entering the space through windows and skylights making the heat generated from the lighting system change over time. Air conditioning and heating systems come in a huge number of configurations, and each one can be used with many different control configurations based on the temperature or other conditions within each space in the building, and ultimately their operation accounts for a large portion of the energy consumed in a building. For these reasons and more, what might first appear as something that can be calculated with just a few formulas in a spreadsheet is instead a software program and, in the case of EnergyPlus, with over 500,000 lines of code.
Questions that BEM can answer[LINK]
The most common questions that BEM can answer are:
If my building was made or operated differently, how would the required equpment capacity and energy consumption change?
Does my building comply with a building energy code or standard?
What kind of rating or how many points can I get in an environmental certification program?
Is my building operating as it was designed to?
What is a good target for energy consumption for my building?
These questions and more can occur at different times during the life-cycle of a building, from before schematic design all the way through the rest of the design process, and into the operation of the building
The Design Process and BEM[LINK]
Building energy modeling can be used throughout the design process for a new building or when considering updates to existing buildings. It can also be used later in the life-cycle of a building related to comparing actual operation of the building with the predicted operation. ASHRAE Standard 209 titled “Energy Simulation Aided Design for Buildings Except Low-Rise Residential Buildings” is a critical document in how to apply building energy modeling. It describes a methodology to apply building energy modeling to the design and was created to define reliable and consistent procedures that advance the use of timely energy modeling to quantify the impact of design decisions at the point in time which they are made. The standard includes different “Modeling Cycles” for different stages of using building energy modeling during the life-cycle of the building:
Modeling Cycle #1 – Simple Box Modeling
Modeling Cycle #2 – Conceptual Design Modeling
Modeling Cycle #3 – Load Reduction Modeling
Modeling Cycle #4 – HVAC System Selection Modeling
Modeling Cycle #5 – Design Refinement
Modeling Cycle #6 – Design Integration and Optimization
Modeling Cycle #7 – Energy Simulated-Aided Value Engineering
Modeling Cycle #8 – As-Designed Energy Performance
Modeling Cycle #9 – Change Orders
Modeling Cycle #10 – As-Built Energy Performance
Modeling Cycle #11 – Postoccupancy Energy Comparison
In addition, it has information about how to integrate climate and site analysis, benchmarking, energy charrettes (a meeting of the stakeholders to discuss goals and design strategies) and the energy performance goals of the owners project requirements into the design process when using building energy modeling.
EnergyPlus QuickStart Guide[LINK]
Don’t be intimidated by the apparent complexity of EnergyPlus; you can get started using EnergyPlus quickly using the QuickStart Guide which is part of the documentation. It shows you how you can use just an input file and some output files to start seeing results quickly. The building description, the detecting and solving of errors, and the most common primary outputs are found in the IDF input file, the Table.HTML output file and the .ERR diagnostics file. Starting with these three files and branching out to others as needed is a good strategy for learning EnergyPlus.
EnergyPlus Capabilities[LINK]
According to the energyplus.net web site (as of January 2019):
Integrated, simultaneous solution of thermal zone conditions and HVAC system response that does not assume that the HVAC system can meet zone loads and can simulate un-conditioned and under-conditioned spaces.
Heat balance-based solution of radiant and convective effects that produce surface temperatures, thermal comfort, and condensation calculations.
Sub-hourly, user-definable time steps for interaction between thermal zones and the environment; with automatically varied time steps for interactions between thermal zones and HVAC systems. These allow EnergyPlus to model systems with fast dynamics while also trading off simulation speed for precision.
Combined heat and mass transfer model that accounts for air movement between zones.
Advanced fenestration models including controllable window blinds, electrochromic glazings, and layer-by-layer heat balances that calculate solar energy absorbed by window panes.
Illuminance and glare calculations for reporting visual comfort and driving lighting controls.
Component-based HVAC that supports both standard and novel system configurations.
A large number of built-in HVAC and lighting control strategies and an extensible runtime scripting system for user-defined control.
Functional Mockup Interface import and export for co-simulation with other engines.
Standard summary and detailed output reports as well as user definable reports with selectable time-resolution from annual to sub-hourly, all with energy source multipliers."
In addition:
ASCII text-based weather, input, and output files that include hourly or sub-hourly environmental conditions, and standard and user definable reports, respectively.
Transient heat conduction through building elements such as walls, roofs, floors, etc. using conduction transfer functions.
Thermal comfort models based on activity, inside dry-bulb temperature, humidity, etc.
Anisotropic sky model for improved calculation of diffuse solar on tilted surfaces.
Atmospheric pollution calculations that predict CO2, SOx, NOx, CO, particulate matter, and hydrocarbon production for both on-site and remote energy conversion.
EnergyPlus can be used for for building load calculations and sizing equipment and uses the heat balance method recommended in the ASHRAE Handbook Fundamentals. Proper sizing of equipment without oversizing, generally saves energy as the equipment is operated nearer to optimal loads.
EnergyPlus runs on Windows, MacOS, and Linux computers.
Integration of Loads, Systems, and Plants: One of the strong points of EnergyPlus is the integration of all aspects of the simulation—loads, systems, and plants. System and plant output are allowed to directly impact the building thermal response rather than calculating all loads first, then simulating systems and plants. The simulation is coupled allowing the designer to more accurately investigate the effect of undersizing fans and equipment and what impact that might have on the thermal comfort of occupants within the building.
Open Source[LINK]
EnergyPlus is an Open Source program so all the source code is available to inspect and modify. If you are interested in how calculations are performed and the Engineering Reference does not provide enough details to you, you can review the source code itself. Instructions to build the code (compile the source code into an executable application) are available in the source code repository wiki if you see something that needs to be enhanced or fixed, please also see the contribution policy.
Brief History[LINK]
EnergyPlus has been under development since 1997 and was first released in 2001. EnergyPlus has its roots in both the BLAST and DOE–2 programs. BLAST (Building Loads Analysis and System Thermodynamics) and DOE–2 were both developed and released in the late 1970s and early 1980s as energy and load simulation tools. BLAST was developed by the Construction Engineering Research Laboratory (CERL) and the University of Illinois while DOE-2 was developed by Berkeley Lab and many others. Their intended audience is a design engineer or architect that wishes to size appropriate HVAC equipment, develop retrofit studies for life cycling cost analyses, optimize energy performance, etc. Born out of concerns driven by the energy crisis of the early 1970s and recognition that building energy consumption is a major component of the American energy usage statistics, the two programs attempted to solve the same problem from two slightly different perspectives. In the late 1990s, concern about limitations of both BLAST and DOE-2 as well as difficulty in maintaining the old code bases prompted combining the development efforts for a new program called EnergyPlus. EnergyPlus was originally written in Fortran, in 2014 it was converted to C++. It was developed as a simulation engine, and many graphical user interfaces utilize it.
Documentation[LINK]
The EnergyPlus documentation is currently included in the installation in the “Documentation” folder as PDFs. It is also available as PDFs online and from third parties that have generated HTML documentation from the source. Using search in the documentation is critical to finding the information needed. Some of the documentation PDFs are very large, so searching is a good way to find specific information about a topic or an input object. The documentation includes:
QuickStart Guide: Contains a brief high-level overview of EnergyPlus and get you up and running quickly with the program
Input Output Reference: Contains a thorough description of the various input and output files related to EnergyPlus, the format of these files, and how the files interact and interrelate.
Output Details and Examples: Contains details on output from EnergyPlus. It also addresses the reference data sets that are included.
Auxiliary Programs: Contains information for the auxiliary programs that are part of the EnergyPlus package. For example, this document contains the user manual for the Weather Converter program, descriptions on using Ground Heat Transfer auxiliary programs with EnergyPlus, and other assorted topics.
Engineering Reference: Provides more in-depth knowledge into the theoretical basis behind the various calculations contained in the program including algorithm descriptions.
Application Guide for EMS: Provides an in-depth look at the Energy Management System (EMS) feature which provides a way to develop custom control and modeling routines.
External Interface(s) Application Guide: Contains information specific to using the external interface feature of EnergyPlus to connect other simulation systems.
Plant Application Guide: Details the methods for simulating chilled and hot water plant systems within EnergyPlus.
Using EnergyPlus for Compliance Guide: Contains information specific to using EnergyPlus in compliance and standard rating systems.
Tips & Tricks for Using EnergyPlus: Contains short tips and tricks for using various parts of EnergyPlus.
Example Files[LINK]
Many hundreds of example files come with EnergyPlus, and they are in the ExampleFiles folder from the installation. The \ExampleFiles\ExampleFiles.html lists each one and includes the name, a description (scroll all the way to the right) and lots of information such as the floor area and whether certain types of input objects are included in the file. Often searching through this file is a good way to find the proper example file to learn about a feature. Another method is the \ExampleFiles\ExampleFiles-ObjectsLink.html file which lists every type of input object that EnergyPlus uses and then the first three files that use that input object. It is possible that many other files also use a particular input object so if the first three files do not help, a text search of files in the ExampleFiles folder may find more.
The EnergyPlus Ecosystem[LINK]
Current Interfaces[LINK]
EnergyPlus is often used directly using the text file input (IDF or epJSON) and various output file formats along with the utilities that come with the installation package. More information on that can be found in section 3. In addition, EnergyPlus is often the simulation engine for graphical user interfaces. To see a list, see the BEST (Building Energy Software Tools) Directory that is operated by IBPSA-USA.
Approaches to Implement Measures[LINK]
In the terminology used within the building energy modeling industry “measures,” sometimes called energy conservation measures (ECMs) or energy efficiency measures (EEMs), are when alternative configurations of a building are considered and simulated and compared with the original building model. Measures include added wall or roof insulation, lower internal lighting power, higher efficiency heating and cooling equipment, and many others. When using EnergyPlus within a graphical user interface, that interface often provides a way to implement various measures. When not working within a graphical user interface, users have several options for implementing measures.
For a specific building input file, a copy of the input file can be made and then modified to reflect the measure. This is an easy approach initially, but since the original building model might change, it means making the change in the file that reflects the measure. When many measures are being considered, this duplicative editing can be inefficient and prone to errors. In addition, the measure cannot be easily applied to a different building energy model without again editing another set of files duplicating the original effort. Due to this, it is very common for some type of scripting to be used so that measures can be applied to the original building model and other models of other buildings reliably and quickly. Scripting in this approach means to apply some type of programming language to the task of modifying files.
EnergyPlus includes, with the installation package, two methods of implementing measures EP-Macro and the ParametricPreprocessor. EP-Macro is similar to the C language pre-processor and allows for portions of the file to be included or excluded, portions of other files to be included when desired, and for specific entries that are normally fixed values to change programmatically. EP-Macro is documented in the AuxiliaryPrograms documentation. A file with lines starting “##” or with the “imf” file extension is likely to be a file using EP-Macro commands.
The EnergyPlus ParametricPreprocessor uses special input objects in EnergyPlus to set values for any field in any other input object for a series of simple options. This is briefly described in the AuxiliaryPrograms documentation, and more details are present in the InputOutputReference under the section on “Parametric Objects.” The ParametricPreprocessor approach is very straight forward, however it has limits in the flexibility that it provides. It is suitable for implementing measures related to internal loads, constructions, and simple efficiency changes but is probably not the appropriate tool for more complicated measures.
A paper that describes various other approaches to scripting was written during the 2018 ASHRAE/IBPSA-USA Building Performance Conference and SimBuild.
Parametric Analysis Tools[LINK]
When just implementing a simple measure or even a series of measures is not enough, a parametric analysis tool may be appropriate. These tools allow the exploration throughout the range of variables (such as the thickness of insulation in the roof or the efficiency of a boiler) to see the impacts of optimization. While many of the approaches used to implement measures described previously may also be used for parametric analysis, a few specific tools have been developed. To see a list, see the BEST (Building Energy Software Tools) Directory that is operated by IBPSA-USA.
Weather Files[LINK]
Weather files are available for many locations throughout the world. Finding the right file that represents the weather in your specific location can sometimes be a challenge. Often the closest weather location is the best one to choose, but sometimes a site that is further away may actually have the most similar weather. This is especially the case in terrain that varies in elevation or when near large bodies of water. Many weather files are available from both public and private sources. The EnergyPlus weather file web site has many weather files with sources described. That web site also has a page with links to many other sites that provide weather files. The modeler must also choose between using a typical year weather files or an actual year file. Typical year files, such as TMY3 and IWEC are representative of long-term weather compiled from 20-30 years of data. Actual year files contain a specific year of weather data and generally used for calibration or verification studies where the simulation results are compared to actual utility bills or other measured data.
Co-Simulation and Linked Software[LINK]
The modelling of multi-domain, multi-physics, and multi-time scale systems such as buildings is a challenge for building energy modelling and simulation tools. In certain circumstances, it may be better for modelling such systems to split the systems into multiple sub-systems, model the individual sub-systems in the language or tool which is best suited for the system’s domain, and use a master algorithm to link the sub-systems for a so called “co-simulation.” In a nutshell, co-simulation consists of the theory and techniques that enable the simulation of a coupled system through the composition of simulators. Each simulator is an input-output mock-up of a constituent system, developed and provided by the team that is responsible for the sub-system. The coupling of the sub-systems is performed by a master algorithm which is responsible for linking the sub-systems at run-time for data-exchange. EnergyPlus implements three mechanisms to support co-simulation.
EnergyPlus implements the Building Controls Virtual Test Bed ( BCVTB) API. This API leverages the BCVTB to enable the co-simulation of EnergyPlus with various simulation programs such as TRNSYS, ESP-r, Radiance, or DYMOLA.
EnergyPlus provides an interface which allows it to import, link, and exchange data with simulation models which implement the Functional Mock-up Interface (FMI) for co-simulation. Such models are called Functional Mock-up Units (FMUs). This feature allows for instance the integration and testing of Simulink or Modelica-based control algorithms which may not exist in EnergyPlus.
EnergyPlus itself can be exported as an FMU which implements the FMI for co-simulation. Such FMU can then be imported into any simulation engine which implements the FMI import interface for co-simulation. This feature is relevant for applications such as the development of building controls. For example, the building envelope of EnergyPlus may be exported as an FMU which in turn will be imported in a tool which is best suited for control development. In this use case, the FMU will be used as a boundary condition for control’s development.
Getting Help[LINK]
Several resources are available for getting help when using EnergyPlus:
UnmetHours
EnergyPlus Helpdesk
EnergyPlus_support mailing list
Several organizations provide paid support
Please do not post questions as issues on the EnergyPlus Github website. Of course, if you are using a graphical user interface with EnergyPlus, the vendor will provide direct support.
After reviewing this document and other pertinent documents that come with EnergyPlus like the InputOutputReference, if additional training is required, several sources are available:
YouTube
University course teaching materials
Several organizations provide paid training
In addition, if you are using a graphical user interface, the vendor probably also provides training.
Using EnergyPlus[LINK]
Installing EnergyPlus[LINK]
Please see the EnergyPlus QuickStart Guide for instructions on how to install EnergyPlus for your system.
Running EnergyPlus[LINK]
EnergyPlus is a simulation engine, so it was designed to be an element within a graphical user interface. However, it can be run standalone without such an interface. There are several options for performing a simulation with EnergyPlus:
Graphical user interface
Command line
EP-Launch
In each case, a building model will be simulated in combination with a weather file for the appropriate building location.
Graphical User Interface[LINK]
When running an EnergyPlus simulation within a graphical user interface, the exact method will vary depending on the specific program being used. You should read the documentation for that software to understand how to perform a simulation. In all cases, the interface will ultimately generate an EnergyPlus idf or epjson input file, execute the EnergyPlus simulation, and read the EnergyPlus output files to present results.
Command Line[LINK]
EnergyPlus can be used as a command line tool within a Terminal window in Linux or MacOS or with the CMD prompt or PowerShell window under Windows. Basic usage using the command line approach is well documented in the QuickStart Guide. To learn more about the command line mode, you can type:
when in the EnergyPlus folder. This will give the following display of options:
EnergyPlus can be run by specifying a number of options followed by the path to the input file. The file itself is usually in IDF (Input Data File) format or epJSON format, but it may also be in IMF (Input Macro File) format to be run with EPMacro using the –epmacro option. Each option has a short form (a single-character preceded by a single dash, e.g., -h) and a long form (a more descriptive string of characters preceded by double dashes, e.g., –help). Several of these options are commonly used including the weather, output-prefix, expandobjects, and readvars options. The following are some examples of using the command line options.
Pre-processing using EPMacro and ExpandObjects:
Forcing design-day only simulations:
Giving all output files the prefix being the same as the input file (building.idf) and placing them in a directory called output:
If no arguments are passed on the command line, EnergyPlus expects the input and weather files to be located in the current working directory and name in.idf (or in.epjson) and in.epw respectively.
EP-Launch[LINK]
For users that want a simple way of selecting files and running EnergyPlus, EP-Launch provides this and more. In addition, EP-Launch can help open a text editor for the input and output files, open a spreadsheet for the result files, a web browser for the tabular results file, and start up a viewer for the selected drawing file. There are two different versions of EP-Launch currently part of the EnergyPlus system.
The main screen of EP-Launch 2 is shown below:
It is a Windows program only. EP-Launch 2 is included in the EnergyPlus installation package when installing on Windows, so no additional steps are needed to run it. It is located in the main “root” folder of EnergyPlus, usually, a folder named EnergyPlusVx-x-x, where the x’s are the version number.
In 2018, EP-Launch 3 was developed, and its main screen is shown below:
EP-Launch 3 is not part of the EnergyPlus installation package and needs to be installed separately. It is also open source and is available from GitHub, and it is documented on readthedocs or in the docs folder on GitHub. EP-Launch 3 works on Windows, MacOS, and Linux systems and is written in Python.
While both EP-Launch 2 and EP-Launch 3 do many of the same functions, the interface is quite different. For now, EP-Launch 2 allows groups of files to be run together and has access to some utilities that the newer version does not. EP-Launch 3 works across multiple platforms and is a built from the ground up to be flexible and extensible so that individuals can make their own workflows that run whatever programs they need to run.
IDF and JSON syntax[LINK]
EnergyPlus has two different input file formats that can be used to describe the building and system that is simulated. The file extensions for the two formats are IDF and epJSON. For both input files, the numeric inputs are in SI units (International System of Units often called metric units).
IDF[LINK]
The legacy file format is a text-based format that describes each input object in series. Each input object starts with the type of input object, and each value for each field follows in strict order separated by commas. The end of the input object is indicated by a semi-colon. Comments are indicated by an exclamation point “!” and anything after this is ignored by EnergyPlus. Commonly, an input object is spread over many lines in the file with one value for each field per line. The names of each field are not required but are usually shown after the value and the comma or semicolon as a special comment using “!-” as an indicator. The input objects can be in any order. An example of an input object in an IDF file is shown below:
The details of this example input object are not important, but the use of commas, exclamation points, and the closing semi-colon are important. The IDF format is currently the most commonly used format throughout the EnergyPlus ecosystem of utilities and GUIs. The list of possible input objects and fields is documented in the Energy+.idd file.
A variation on the IDF file format is the IMF file format which includes macros that can be used for parametric analysis or file management called EP-Macros. To learn more about macros see the Input Macros chapter of the AuxiliaryPrograms document.
epJSON[LINK]
A new file format based on the industry standard JSON format most often used to transmit data to and from web servers and web-browser based applications. It is a text-based file format. The JSON format has wide usage across many industries and is supported in just about every modern programming language. It is a field-value style format using brackets and colons to indicate the hierarchy and commas to separate each field and value pair. The input objects must appear grouped by the type of input object. The list of possible input objects and fields is documented in the Energy+.schema.epJSON file which uses json-schema. The same input object shown above in IDF format is shown below in epJSON format:
While the IDF and epJSON file formats are quite different, they contain the same information, and either may be used. In general, if producing EnergyPlus input files using a programming language, the epJSON format might make more sense while, at this point, if producing IDF files using a GUI, they are likely to use the IDF format. EnergyPlus, when used on the command line, can convert from IDF to epJSON and from epJSON to IDF using the -c or –convert option.
Creating and Editing Input Files[LINK]
Since both the IDF and epJSON file formats are text formats, a simple text editor may be used to edit them. Even if not regularly used, a good text editor is an important application to have when working with EnergyPlus. There are many different text editors, and a few have special features related to the IDF format such as syntax highlighting including Atom, Notepad++, and UltraEdit.
Another editing choice for IDF file is the IDF Editor which comes with EnergyPlus in the \PreProcess\IDFEditor directory and can be run directly or from EP-Launch. It is a Windows-only program and was not designed to run on Linux or MacOS. It is specially designed for editing IDF files and includes many features to simplify the process. It performs unit conversions so either SI (metric) or IP (inch-pound) units can be used for editing but the IDF file is always saved in SI units. It can initialize an input object using the default values and has indications when values outside the acceptable range are used. The main screen of the IDF editor is shown below. Full details of the IDF Editor can be found in the Auxiliary Programs document under the “Creating Input Files” section.
Run-Check-Edit Repeat[LINK]
For most building energy modeling projects, whether assisting in early design, refining a design, selecting a control method, or calibrating an existing building, the use of EnergyPlus will be part of a repeating process. The process will probably be in the form of:
Running an EnergyPlus input file
Checking error and other output files
Fixing the input file
Repeat
Don’t expect that an initial model is ever correct; it is probably not. Initially, errors are likely to exist. The .ERR file should be the first file checked each time EnergyPlus is run. The .ERR file has several levels of messages:
Warning
Severe
Fatal
A Fatal error means that EnergyPlus has stopped during the simulation and the input file needs to be fixed before the simulation can be run to completion. Fatal errors should be the first thing fixed. Some Fatal messages reference previous Severe messages so in that case those should be fixed. Since the entire simulation was not performed, it is likely that once the fatal errors are fixed that new Severe and Warning messages will be shown. After all Fatal messages are eliminated, you should work on Severe messages; they should also be fixed. Finally, Warning messages should be reviewed. Often Warning messages are informative and point out unusual configurations, conditions, or choices. If what is being described by the Warning message is as intended, then the Warning message can be ignored. More often, the Warning message points out something that is not as intended and should be fixed or addressed. Since the .ERR file is a text file; you can usually keep it open in a text editor program. Many (but not all) text editor programs will detect that the .ERR file has been updated after each EnergyPlus simulation and lets you load the most recent version.
The next files to be examined are ones that show output results from the simulation. Either the tabular output file (usually an HTML file see Output:Table:SummaryReports and OutputControl:Table:Style) or CSV file (see Output:Variable and Output:Meter) should be examined depending on what you want to look at. Upon examination of the output results, it is very likely that an aspect of the building and its systems are not behaving as expected. For example, the Annual Building Utility Performance Summary report contains a subtable titled Comfort and Setpoint Not Met Summary. If an annual simulation has 100s or 1000s of hours of setpoint not met, then the HVAC system is undersized, or the controls are not working as expected. With an input file representing many thousands of assumptions, some assumptions made by you or as a default of EnergyPlus are likely to be incorrect. Revising the EnergyPlus input file to address this may cause new issues to be shown in the .ERR file so it should always be examined after each change.
To speed the process of running the simulations, you may want only to run a design day (see SimulationControl and SizingPeriod:DesignDay) or a subset of the year (see RunPeriod) while developing and debugging the inputs. This approach speeds up the simulation time itself, and if used, please remember to recheck the .ERR file when running an annual simulation for the first time.
Key Concepts[LINK]
The following sections highlight some key concepts in EnergyPlus
Everything Included[LINK]
One principal that EnergyPlus uses is that (almost) everything is specified in the input file. This means that instead of referencing an external library for materials, schedules, equipment performance, etc., the input objects that fully describe those items should be included directly in the input file. In addition, each input object contains a list of values for every field that needs one. The DataSets folder distributed with EnergyPlus contains these kinds of details and to use them, the input objects should be copied into the input file that you are developing. This approach does make the file include more specification than you might be used to, and typically results in a large input file, but you will have the assurance of knowing that all the inputs related to your building are in the input file you have developed. There are a few exceptions where external data is referenced such as with Schedule:File input objects.
Wall Thickness[LINK]
Exterior and interior walls in real buildings have a thickness as specified on building plans by detailed cross-sections. For EnergyPlus, the Construction input object is made up of a list of names for the Material input objects that make up the wall or roof or floor. Each material input object has a thickness along with the conductivity, density, specific heat and other factors. These thicknesses should match the thicknesses shown in the detailed cross-sections. But when it comes to specifying the walls themselves in three-dimensional space, the walls should be entered assuming zero thickness. Once each surface has been placed, changing the material thickness will have no impact on zone volume, ceiling height, floor area, shading, or daylighting. For most modern buildings the choice of where to locate the wall: inside vs. outside vs. centerline should have little impact on results, so many modelers just pick one and let the volumes be slightly off. Using centerlines throughout the model splits the difference. Or some modelers use outer edges for exterior walls and then use centerlines for interior walls. If you are modeling a very thick wall, such as an old stone building, then you also have thermal mass considerations. If you use the outside edges there will be too much mass, inside will be too little. Again, centerline will split the difference and will be very close to the correct amount of thermal mass (possibly losing some corner mass).
Zones Are Not the Same as Rooms[LINK]
A zone, sometimes called a “thermal zone,” is a theoretical construct that usually describes a group of rooms that can be treated as a single thermal entity. A zone typically includes multiple rooms. Often a zone can be seen as a group of rooms that share a single thermostat. In the case of many similar rooms with the same thermal and operating characteristics, even if many different thermostats are used, they may still be grouped into a single zone in EnergyPlus.
One Construction Per Surface[LINK]
Only one type of construction can be associated with each surface so if the top half of a wall is made up of a different construction than the bottom half of the wall, the top half and the bottom half each need to be represented as separate surfaces.
Available Outputs Created by First Simulation[LINK]
Since EnergyPlus creates a custom list of possible output variables during each simulation, you need to perform a simulation first before you can see them. To create the list use the Output:VariableDictionary input object and then check the .RDD and .MDD files that are created. Select the outputs you want and specify them in the input file.
Always Plan Ahead[LINK]
Some preliminary steps will facilitate the construction of your input file. EnergyPlus requires some information in specified, externally available formats; other information may require some lead time to obtain. The following checklist should be completed before you start to construct your input file.
Obtain location and design climate information for the city in which your building is located. If possible, use one of the weather files available for your weather period run.
Obtain sufficient building construction information to allow specification of overall building geometry and surface constructions (including exterior walls, interior walls, partitions, floors, ceilings, roofs, windows, and doors).
Obtain sufficient building use information to allow specification of the lighting and other equipment (e.g., electric, gas, etc.) and the number of people in each area of the building.
Obtain sufficient building thermostatic control information to allow specification of the temperature control strategy for each area of the building.
Obtain sufficient HVAC operation information to allow specification and scheduling of the fan systems.
Obtain sufficient central plant information to allow specification and scheduling of the boilers, chillers and other plant equipment.
Obtain utility tariff information when expressing the results as costs.
Obtain component cost information when performing life-cycle costs.
What Are All These Folders?[LINK]
The installation of EnergyPlus includes many different files in different folders:
Many of these folders include valuable resources for using and learning EnergyPlus.
The main folder includes the EnergyPlus executable which can be used on the command line and EP-Launch 2, a program that makes it easier to use EnergyPlus and the Energy+.IDD that describes each possible EnergyPlus input object and the default, minimum, maximum, and options for each field within each input object.
The Documentation folder includes this document as well as the InputOutputReference, EngineeringReference, AuxiliaryPrograms, OutputDetailsAndExamples which are very important to understand. If you haven’t looked through the documentation yet, take a few minutes and get familiar with it.
The DataSets and MacroDataSets folders include files containing libraries of input objects that may be useful in constructing your own input files. The ASHRAE_2005_HOF_Materials.idf and WindowConstructs.idf files, for example, will help with defining walls and windows.
The ExampleFiles folder includes a huge number of example files that are indexed in the two HTML files in that folder or can be searched through using most text editors.
The Preprocess and PostProcess folders include many utilities that can be used directly or as part of EP-Launch that can aid in the setting up input files or extracting or converting results. The WeatherData folder includes a small sample of the many weather files that are available. For other weather files, please see the previous section on 2.4.
What Are All These Output Files?[LINK]
When running EnergyPlus using EP-Launch or from the command line, depending on the options selected, many different output files may be generated. The file extensions and file suffixes (added to the original file name prior to the file extension are shown below:
ERR – list of errors and warnings
TABLE.HTML, TABLE.TXT, TABLE.TAB, TABLE.CSV, TABLE.XML – tabulated report of the bin and monthly data in HTML, space delimited, tab delimited, comma delimited, or XML format. This is one of the primary otuput files.
CSV, TAB, or TXT – time series output from the Output:Variable input object in a comma, tab, or space delimited format (generated by the ReadVarsESO postprocessor)
METER.CSV, METER.TAB, or METER.CSV File – time series output from the Output:Meter input object in a comma, tab, or space delimited format (generated by the ReadVarsESO postprocessor)
SQL - sqlite3 output database format
EIO – additional EnergyPlus results
RDD – list of output variables available from the run
MDD – list of output meters available from the run
MTD – list of meter component variables
DXF – drawing file in AutoCAD DXF format
AUDIT – input file echo with input processor errors and warnings
BND – HVAC system node and component connection details
DBG – output from the debug command
EDD – Energy Management System details
END - a single line synopsis of the simulation
EPMIDF – clean idf file after EP-Macro processing
EPMDET – EP-Macro detailed output with errors and warnings
ESO – raw Output:Variable output before processing into CSV, TAB, or TXT files
MTR – raw Output:Meter output before processing into CSV, TAB, or TXT files
SHD – output related to shading
SLN – output from “report, surfaces, lines”
SSZ – system sizing details in a comma, tab, or space delimited format
ZSZ – zone sizing details in a comma, tab, or space delimited format
MAP – daylighting illuminance map
DFS - daylighting factors report
Screen.CSV - window screen transmittance map report
RVAUDIT - output from the ReadVarsESO post-processing program
SVG - HVAC Diagram related to the arrangement of HVAC components
SCI - surface cost information report
WRL – drawing file in VRML (Virtual Reality Markup Language) format
Delight IN - DElight input generated from EnergyPlus processed input
Delight OUT – Detailed DElight output
Delight ELDMP – DElight reference point illuminance per time step
Delight DFDMP – DElight warning and error messages
EXPIDF – Expanded IDF when using HVACTemplate input objects
Group Error – combined error files for a group run
VCpErr – Transition program error file
Proc.CSV – Simple statistics generated from CSVProc
Most of these output files are documented in the Output Files chapter of the OutputDetailsAndExamples document.
Don’t be intimidated by the long list of files; you can do a lot in EnergyPlus with just the IDF input file, the TABLE.HTML file, and the ERR file. The building description, the detecting and solving of errors, and the most common primary outputs are found between these three files. Starting with these three files and branching out to others as needed is a good strategy for using EnergyPlus.
Versions and Updating[LINK]
EnergyPlus version updates are released generally twice per year in March and September. Each version of EnergyPlus is installed to a unique folder, so it is possible, and recommended, to keep older versions in place when adding a new one. This is very helpful if you need to go back and make a change to an older project and don’t want to introduce version-related changes in results. When using the IDF input file format with EnergyPlus, each release is likely to have small changes to the file format. Included with EnergyPlus are a number of ways to update files so that they are compatible with the release. Each method ultimately uses the TransitionVx-x-x-ToVx-x-x.exe files that are located in the Preprocess\IDFVersionUpdater folder. The ways to update your IDF files are:
EP-Launch 2 - The Windows-only program that comes with the EnergyPlus installation can update a single file from the just previous version of EnergyPlus by using the File…Transition command.
EP-Launch 3 - The program for Windows, Linux, and MacOS can update a single file across multiple versions using the Transition workflow.
Command line Transition - This allows updating files using the command line such as the Terminal for MacOS and Linux or the CMD or PowerShell for Windows. It is documented in the Chapter titled “Using Older Version Input Files - Transition” in the AuxiliaryPrograms document.
Errors and How to Fix Them[LINK]
As described in the section dealing with errors described in the ERR file are part of creating files with EnergyPlus. Resolving errors is something that both new and very experienced users have to do. Most of the error message itself, if carefully reviewed will point to the problem. Some error messages will also reference earlier messages that should also be checked. A careful review of the ERR file and the input file will often reveal solutions to the most common errors. Also, see the section.
Data Sets[LINK]
EnergyPlus uses snippets of IDF files to create the library of data that may be useful for you. Two folders are created upon installation: DataSets – which contains IDF snippets and MacroDataSets – which also contain IDF snippets but are in a form such that they can be easily used with the EPMacro program. Another data set are DDY files that acompany each EPW weather file. The DDY files include several varieties of the corresponding design day data for each weather file location.
Other Useful Utility Programs[LINK]
The EnergyPlus install includes a variety of tools to help with various aspects of converting data or displaying information to help with using EnergyPlus
Coefficient Curve Generation - The CoeffConv and CoeffConv utility programs can be used to convert DOE-2 temperature dependent curves (Fahrenheit) to EnergyPlus temperature curves (Celsius). These programs are described in the Auxiliary Programs document.
HVAC Performance Curve Fit Tool - The CurveFitTool.xlsm spreadsheet generates performance curves for a set of tabular data as typically supply by manufacturers
HVAC-Diagram - Another post-processing program is the HVAC-Diagram application. It reads one of the EnergyPlus output files (eplusout.bnd) and produces a Scalable Vector Graphics (SVG) file. Many web browsers and other drawing programs can open SVG files. This utility runs automatically with EP-Launch. More information on the HVAC Diagram program is found in the Auxiliary Programs document.
convertESOMTR - This simple post-processing program can be used seamlessly with EP-Launch to provide IP (inch-pound) unit output files rather than SI units. This program is described more fully in the Auxiliary Programs document.
WeatherConverter - Used to convert epw to csv format with column headings to inspection of the data.
Input Object Groups[LINK]
The following sections provide an overview of the input objects based on groups described in the energy+.idd file and the InputOutputReference. The sections give you a taste of the capabilities and may help guide you to further investigation on how to model your building or a specific energy efficiency measure.
Simulation Parameters[LINK]
EnergyPlus includes a group of input objects used to set general parameters related to how the simulation is performed. Some of these input objects are controlling different options that are allowed within EnergyPlus such as the selection of algorithms to use or parameters related to how an algorithm is used. For a new modeler, these input objects should be included with their default field values. Later when additional control is necessary to model a specific type of measure, the field values can be re-evaluated. The following input object allows you to control how you want the simulation to be performed. The input objects should appear in your file and appear in almost all of the example files:
Two other input objects should appear in your input file and are included in almost all example files:
Version - indicates what version of EnergyPlus is being used.
Building - includes fields for the name of the building, and the angle of the entire building compared to true north, as well as parameters related to the simulation that, in general, should be allowed to default.
For a new modeler, the following input objects may be omitted. They can be added later for special cases althought they and appear in almost all of the example files:
Timestep - the number of timesteps each hour and usually set to 6.
HeatBalanceAlgorithm - selects the algorithm used for simulating heat and moisture transfer through the surfaces of the building and usually set to ConductionTransferFunction.
SurfaceConvectionAlgorithm:Inside - selects the algorithm used for the inside face of the building surfaces and is usually set to TARP.
SurfaceConvectionAlgorithm:Outside - selects the algorithm used for the outside face of the building surfaces between interior and exterior conditions and is usually set to DOE-2.
These input objects and more are further explained in the InputOutputReference under the heading “Group-Simulation Parameters.”
Location and Climate[LINK]
Many of the fields in the group of input objects related to location, climate, and the weather file are ones that will be set once for each specific project.
Site:Location - describes the name, latitude, longitude and other parameters related to the location of the building. When using a weather file, the values from the weather file will be used instead. Predefined location objects may be found in the DDY file that accompanies most epw weather files.
SizingPeriod:DesignDay - the high and low temperature and humidities describing a design day that is used for sizing equipment. Two (or more) instances of this input object are frequently in a file, one for heating and one for cooling. The DDY file that comes with the weather file should include input objects that may be used here.
RunPeriod - the start and stop dates of the simulation and often set to the full year. When debugging a file, a shorter period of time can be used to speed up the simulation portion of the Run-Check-Edit cycle.
RunPeriodControl:SpecialDays - allows specfication of holidays and a good example can be seen in 5ZoneCostEst.idf.
RunPeriodControl:DaylightSavingTime - allows the specification of the start and ending period for daylight savings time. This will impact when schedules operate but please note that output reporting timesteps are always shown in standard time so schedules will shift an hour in the output when daylight savings time is active. A good example can be seen in 5ZoneCostEst.idf.
Site:GroundTemperature:BuildingSurface - for one of the ground temperature algorithms, specifies the average temperature for each month of the year. This temperature is applied directly to the outside face of surfaces which use the Ground outside boundary conditions. See Ground Heat Transfer in EnergyPlus in the Auxiliary Programs document for information about preprocessors. There are also other more integrated ground heat transfer options, see Site:GroundDomain:* and Foundation:Kiva.
Site:WaterMainsTemperature - input for the water temperatures supplied to the building from underground water mains and should be specified whenever water heaters are described. A good example can be seen in 5ZoneVAV-ChilledWaterStorage-Mixed.idf. If not specified, some default assumptions are used for the water temperature supplied to the building.
Other input objects in this group can help perform sizing using the weather file, override the sky temperature, impact the variation of outdoor conditions with building height (especially important for tall buildings), work with ground temperatures and ground heat transfer, override the precipitation in weather files, specify the irrigation for a green roof, and some advanced properties related to the light spectrum for window performance. These input objects and more are further explained in the InputOutputReference under the heading “Group-Location and Climate.”
Schedules[LINK]
Many aspects of building operation are characterized by timing whether it is the hours that a building is occupied or when the control systems are in various modes. Due to this, specifying when something occurs using the Schedule input objects becomes one of the most common things to do. It is important to coordinate schedules properly. The operation of office equipment in a space usually corresponds to occupancy of that space as does the thermostat set points and fan operation. Because schedules are such a key input for so many features of a building, a great deal of flexibility exists in EnergyPlus to specify them.
Schedule:Compact - The most commonly used method of specifying schedules and uses “Through” and “For” to reduce the amount of input required.
ScheduleTypeLimits - Every schedule input object includes a field that helps validate the limiting values for the schedule, and this input object describes the upper and lower limit.
Schedule:Constant - If the value of the schedule is the same every hour of the year, this input object is the easiest way to specify that value.
Schedule:File - At times, data is available from a building being monitored or for factors that change throughout the year. This input object allows a column of data from an external file to be referenced as the values of the schedule. A variation of this input object allows input specifically for shading.
Other input objects in this input group allow specification of schedule values to be in different formats. These input objects and more are further explained in the InputOutputReference under the heading “Group-Schedules.”
Surface Construction Elements[LINK]
Specifying the physical properties of the building envelope is something every building model includes. The input objects in this group allow the specification of the different layers that make up exterior and interior walls, roofs, floors, windows, and skylights as well as the order of the materials in these surfaces. A large number of input objects appear in this group since there are many special features that need to be modeled for certain energy efficiency measures. The following is a list of only the most commonly used input objects.
Material - the most common input object to describe the materials used in opaque constructions in walls, roofs, and floors and includes inputs for the thickness, conductivity, density, and specific heat as well as absorptances. See examples in ASHRAE_2005_HOF_Materials.idf located in the DataSets folder.
Material:NoMass - used when the material only has thermal resistance and little thermal mass such as insulation. It should not be used to describe materials that do have significant thermal mass.
Material:AirGap - used to describe when walls or roofs have an air gap. Note, this is modeled as a fixed resistance (with no internal convection or radiant transfer), and it cannot be used for windows.
WindowMaterial:Glazing - describes the material used in the glass (or other transparent material) portion of the fenestration (windows and skylights). See WindowGlassMaterials.idf in the DataSets folder for examples.
WindowMaterial:Gas - the type of gas used between layers of glass in windows and skylights has a significant impact on the heat transfer performance. See WindowGasMaterials.idf in the DataSets folder for examples.
Construction - a list of materials (any from the list above plus others) in order from the outside to the inside making up the wall, roof, floor, window or skylight. Every input file will have several of these input objects. Examples of constructions for walls, roofs, and floors can be found in ASHRAE_2005_HOF_Materials.idf located in the DataSets folder while examples for windows and skylights can be found in WindowConstructs.idf in the same folder.
WindowMaterial:SimpleGlazingSystem - the best way to describe a window is with a construction input object that references WindowMaterial:Glazing and WindowMaterial:Gas input objects but if all you have is the U-Factor and Solar Heat Gain Coefficient (SHGC) they can be specified in this input object.
A large variety of input objects in this group are not as commonly used but are key to modeling specific types of walls and windows so if what you are trying to model does not fall into the neat categories for the input objects described so far, there is still a good chance that EnergyPlus has an input object that will work. These other input objects include ones for walls and roof that can be used when modeling combined heat and moisture transfer, modeling materials which undergo a phase change to store heat in the wall or when the material properties change with temperature, when the material allows infrared radiation to flow through it, when modeling green (vegetated) roofs, for simplified C- or F-factor modeling, or when the wall includes resistance or hydronic tubing to provide heat. The other input objects to describe windows and skylights include input objects that can be used to describe thermochromic and electrochromic glazing, mixtures of gases between layers of glass, vacuum glazing, movable portions of the window assembly such as shades and blinds and screens, alternative ways of specifying fenestration such as equivalent layers or refraction extinction method or ASHWAT model or from a WINDOW program export/data file or specifying wavelength-by-wavelength properties.
The input objects described in this section are further explained in the InputOutputReference under the heading “Group-Surface Construction Elements.”
Thermal Zones and Surfaces[LINK]
The physical aspects of the building such as the walls, roof, and windows, is one of the most important and often challenging aspects of creating a building energy model. In EnergyPlus, the surfaces define the geometry of each zone and thus for the entire building. For many, a graphical user interface will be used to help define the geometric aspects of the building energy model, and many of the input objects described in this section will be directly created by that interface program. It is still important to understand some of the details for these input objects because it is likely that you will be reviewing them as part of debugging error messages. EnergyPlus uses the three dimensional position of each corner of a surface to define the position and orientation of that surface so for a typical rectangular wall that represents 12 numbers and for a typical building with hundreds of surfaces that means thousands of numbers are used to define the geometry of a building so you can see why using an interface is so common.
EnergyPlus uses a right-hand coordinate system as shown in Figure X with three dimensions. The X-axis points east, the Y-axis points north, and the Z-axis points up.
Zone - defines the name of the thermal zone as well as the ceiling height, floor area, and volume. For most zones that are fully enclosed these three entries can be calculated automatically be EnergyPlus and do not need to be entered. A zone multiplier allows a single zone to represent many identical zones (such as all the enclosed offices on one side of a building). The name of the zone will be referenced in many places in the input file so it should be clear what it is describing. When defining a zone, it is important for the entire area to be thermally similar both in heat being transferred through exterior walls as well as interior heat gains. But using as few zones as possible (and thus as few surfaces) also can result in faster simulations, so there is no reason to slow down the simulation just so two (or more) essentially identical areas are each simulated. The coordinates can be just set to zero if the world coordinate system is used (see GlobalGeometryRules below).
BuildingSurface:Detailed - lists the three-dimensional coordinates that define each corner as well as referencing the zone that the surface is attached to and the construction of the wall (list of materials). This input object supports any shape surface with three or more corners (vertices). In addition, this input object defines what is on the other side of the surface from the zone, whether that is outside, another zone in the building, or the ground. Other inputs indicate if the outside of the surface is exposed to the sun or the wind.
FenestrationSurface:Detailed - describes windows, doors, and special daylighting tubes and it references the wall that it is part of. It also requires the specification of vertices (usually four but three is also allowed) to describe the corners of the window or door as well as the construction which, in this case, is generally the layers of glass and the gas fill between the layers. It has a field for a multiplier although usually the multiplier is set to one since the position of windows matters to many of the algorithms used. In order to describe the frame of the window and any dividers that it might have, a separate input object (WindowProperty:FrameAndDivider) may be included and referenced. A good example file is WindowsTests.idf. To understand how to model the many options for windows, a section and a table in the Input Output Reference called “Window Modeling Options" should be examined.
Shading Related[LINK]
Casting shadows on the building, especially onto windows, can significantly impact the energy use of a building, and EnergyPlus includes several input objects to model this effect. The largest impact of shading surfaces is to reduce solar gain through windows that are shaded. There are two kinds of shading surfaces in EnergyPlus, detached and attached. A detached shading surface, such as a tree or neighboring building, is not connected to the building. An attached shading surface is typically an overhang or fin that is attached to a particular base surface of the building, usually a wall; attached shading surfaces are usually designed to shade specific windows.
Shading:Site:Detailed - describes something near but not attached to the building that casts a shadow on the building such as nearby buildings or mountains and includes the vertex of one corner as well as the length and width. For deciduous trees, and other situations that shading changes over time, the schedule for the transmittance can vary, otherwise, it should always be set to zero or leave the schedule name blank.
Shading:Zone:Detailed - describes an attachment to the building that casts a shadow such as an overhang or fin. It also includes a reference to a transmittance schedule. The wall that the fin or overhang is attached to is also specified.
If using relative coordinates (see GlobalGeometryRules), you may also want to use the Shading:Building:Detailed input object since it will “rotate” with the building. Typically, Shading:Site:Detailed is used for things that are fixed at the site and don’t move with building rotation. Shading:Building:Detailed is for larger structures like a parking garage or canopy which aren’t associated with a specific zone but would likely rotate with the building.
Input Object Variations[LINK]
EnergyPlus includes a bunch of variations on these basic surface input objects that map to a closer representation of real surfaces in buildings. These input objects are effectively just different ways to represent the same information as the BuildingSurface:Detailed, FenestrationSurface:Detailed, and Shading:Zone:Detailed input objects. These input objects are seldom created by graphical user interfaces, so it is unlikely that you will see them. Some of these input objects also have simpler methods for specifying geometry, such as using a single vertex, height, width, tilt, and azimuth or just specifying the fin location relative to the window edge. The following is a list of these input object variations for surfaces:
Wall:Detailed, Wall:Exterior, Wall:Adiabatic, Wall:Underground, Wall:Interzone
RoofCeiling:Detailed, Roof
Floor:Detailed, Floor:GroundContact, Floor:Adiabatic, Floor:Interzone
Ceiling:Adiabatic, Ceiling:Interzone
Window, Window:Interzone
Door, GlazedDoor, Door:Interzone, GlazedDoor:Interzone
Shading:Site, Shading:Building, Shading:Overhang, Shading:Overhang:Projection, Shading:Fin, Shading:Fin:Projection
Other Related Input Objects[LINK]
GlobalGeometryRules - A required input object that should be in all files. It sets the way geometry is specified for all of the surface input objects. The most common approach is that the order of coordinates for each surface should start with the upper left corner (when viewed from “outside” the zone with the surface) and that the coordinates should proceed in a counter-clockwise order. In addition, most common is to use a world coordinate system where all the vertices are based on a single coordinate system for the entire building rather than one that changes relative to each zone. However, if you want to rotate the building, then you must specify Relative coordinates, and the zone origins may all remain at (0,0,0).
WindowShadingControl - for a window, describes the kind of movable shading (interior shade, interior blind, between glass shade, exterior blind, etc..) as well as how it is controlled and the physical material of the shade or window construction with the shade. Good examples are in the PurchAirWithDaylightingAndShadeControl.idf file.
WindowProperty:FrameAndDivider - defines the frame material around a window and any dividers between separate lites of the window (see Figure X). While a window does not necessarily need to define the frame, it is a more accurate approach since the heat transfer through the frame usually has significant impacts the overall performance of a window. Note that the area of the Fenestration:Detailed object is the glazed area without the frame. The frame extends beyond the glazed area. See the PurchAirWithDaylighting.idf example file.
WindowProperty:AirflowControl - defines windows that have forced air flow between the panes of glass, also called heat-extract windows or climate windows. See the example file AirflowWindowsAndBetweenGlassBlinds.idf.
WindowProperty:StormWindow - allows the definition of a movable storm window that is usually applied to a window in the winter. See the StormWindow.idf example file.
InternalMass - used to define thermal mass that is not described anywhere else in the model - often used to capture the effect of furnishings or interior floors that are not being modeled. Used in many example files including RefBldgLargeOfficeNew2004_Chicago.idf.
ShadingProperty:Reflectance - specifying the reflectance properties for shading and is only needed if the input object Building specifies the “with reflections” option. See the ReflectiveAdjacentBuilding.idf example file.
Other less common input objects include ZoneList and ZoneGroup that can be used when doing multi-story simulations and GeometryTransform which allows a building model to be stretched with just a few inputs.
Internal Gains[LINK]
Inside a building, people, appliances, office equipment, lighting, and other devices produce heat. The combination of all these items that produce heat within a building are called internal gains and represents a significant contribution, sometimes the largest contribution, to the cooling requirements for a building. In addition, they offset the amount of heat from the HVAC system that is needed at a given time. Typically, the peak value is entered in the input objects for this group such as the maximum number of people, the total power of equipment, or the total lighting power and then a schedule is used to modify that value each hour of the year. It is just as critical that the schedule values are realistic for your building as is the peak value. For almost all buildings, it is rare that the peak occupancy occurs for more than a few hours per year if at all and this is especially the case for retail stores, theaters, and sports complexes. Even office buildings when counting vacations and people out of the building for meetings will rarely have peak occupancy.
The most common internal gain input objects that are shown in almost all the example files are:
People – specifies not only the sensible, latent and radiant heat from people but also includes ways of reporting the comfort of occupants using a variety of thermal comfort models. The DynamicClothing.idf example file shows how to use the thermal comfort models.
Lights – describes the heat related to lighting systems.
ElectricEquipment – describes the heat related to electrical appliances, office equipment, and other heat sources that are powered by electricity.
GasEquipment - specifies the heat related to cooking appliances and other equipment that uses natural gas.
Less common internal gains input objects include:
OtherEquipment - describes any heat gain or loss (sensible, radiant, and/or latent) that impacts the space but does not consume utility energy in the simulation. Typically used to model a process load which is not to be included in the overall building energy consumption.
ElectricEquipment:ITE:AirCooled - see the 1ZoneDataCenterCRAC_wApproachTemp.idf example file.
SwimmingPool:Indoor - see the 5ZoneSwimmingPool.idf example file.
Other
The Internal Gains group also contains input objects related to zone contaminant sources and sinks. The input objects include modeling components that impact contaminant concentrations which are scheduled, pressure driven, use a cut off model, assume a decaying source, surface diffusion, or using a deposition velocity model. The input objects described in this section are further explained in the InputOutputReference under the heading “Group-Internal Gains.”
Daylighting[LINK]
Reducing the amount of powered lighting that is used when sufficient natural daylight illuminates the interior building through windows and skylights is called daylighting. Automatics daylighting control systems are a very common energy efficiency measure in buildings and are often required for new building designs depending on the energy code that applies to the building location. The most common input objects related to daylighting are:
Daylighting:Controls – specifies the algorithm used for daylighting, the dimming of lights is continuous or stepped, and how glare calculations are performed.
Daylighting:ReferencePoint – specifies the location of the sensors for the daylighting control system.
The InputOutputReference includes not only a description of these input objects but also extra guidance on how they should be applied. The PurchAirWithDaylighting.idf contains examples of these input objects.
Three different devices can be used with daylighting:
DaylightingDevice:Tubular - see the DaylightingDeviceTubular.idf example file.
DaylightingDevice:Shelf - see the DaylightingDeviceShelf.idf example file.
DaylightingDevice:LightWell - see the GeometryTest.idf example file.
An input object called Daylighting:DELight:ComplexFenestration is used with one of the two control methods specified in the Daylighting:Controls input object when used in conjunction with complex fenestration systems such as prismatic and holographic glass.
Some flexibility is given to provide extra output related to daylighting and includes:
Output:DaylightFactors – creates a special report on the factors used in daylighting. See the ReportDaylightFactors.idf example file.
Output:IlluminanceMap – allows the generation of maps of illuminance values within each interior zone that uses daylighting controls. The exact file format can be set using the OutputControl:IlluminanceMap:Style input object. See the DaylightingDeviceTubular.idf for example of both input objects.
More details of these output options can be found in the OutputDetailsAndExamples document. The input objects described in this section are further explained in the InputOutputReference under the heading “Group-Daylighting.”
Advanced Construction, Surface, Zone Concepts[LINK]
The group of input objects contains many special cases for more sophisticated modeling for constructions, surfaces, and zones. As part of this, one of the ways to model building foundations called Kiva is described. See the ZoneCoupledKivaBasement.idf and ZoneCoupledKivaSlab.idf example files for example of these input objects.
Foundation:Kiva - describes the insulation depth and width for interior and exterior horizontal and vertical insulated foundations as well as the construction for the wall footing, see Figure X .
Foundation:Kiva:Settings - sets the soil conditions and other parameters related to the Foundation:Kiva input object.
SurfaceProperty:ExposedFoundationPerimeter - used to set the portion of the foundation that is along the exterior perimeter of the building that undergoes heat transfer with the environment. Edges of underground surfaces that are fully under the building and not along the perimeter are not expected to have any heat transfer with the environment.
Input objects of interest in this group not related to Kiva include
SurfaceControl:MovableInsulation - allows the modeling of insulation panels that are removable for walls, floors, and roofs but not windows. See MovableExtInsulationSimple.idf and MovableIntInsulationLightsLowE.idf example files.
SurfaceProperty:Underwater - allows the outside of the building to be modeled as underwater and even as moving through the water allowing EnergyPlus to model vessels. See the VaryingLocationAndOrientation.idf example file.
SurfaceProperty:ExteriorNaturalVentedCavity - provides a method to include the modeling of baffles in the multi-skin exteriors. See the HP_wICSSolarCollector.idf example file.
Other input objects in this group set the heat transfer algorithms for specific surfaces to override the building level heat transfer algorithm, when other models are used to describe the variation in temperature on the outside of a surface, override the algorithm used for modeling convection heat transfer between the air inside or outside of a zone and the surface, vapor transfer coefficients when using algorithms that include moisture modeling of surfaces, override the algorithm that distributes the solar radiation on interior surfaces, overrides the solar energy absorbed by different layers for complex windows, a way to override the longwave radiation with other surfaces in the zone, allows overriding the external environment for a surface or a zone including solar shading or airspeed or temperature or humidity, overrides the source term for the heat balance, or overrides the view factors for a zone. The input objects described in this section are further explained in the InputOutputReference under the heading “Group-Advanced Surface Concepts.”
Exterior Equipment[LINK]
While equipment that is outside of a building does not impact the thermal performance of the building, the accounting of all end-uses including those outside of the building is important for many compliance and incentive programs that require building energy modeling. See the ExteriorLightsAndEq.idf example file for these input objects.
Exterior:Lights - describes the external site lighting for the building grounds, entrances, and facades which are either controlled by a schedule or when the sun is set.
Exterior:FuelEquipment - describes other energy consumption on the site that is external to the building other than lighting.
Exterior:WaterEquipment - describes the flow rate of water use on the building site outside of the building.
The input objects described in this section are further explained in the InputOutputReference under the heading “Group-Exterior Energy Use Equipment.”
Zone Airflow[LINK]
The Zone Airflow input object group provides a way to model the airflow between zones and airflow due to natural ventilation (e.g., open windows) or mechanically-induced ventilation (e.g., exhaust air fans).
ZoneInfiltration:DesignFlowRate - provides a way to describe the air infiltration into a building through leaks in the envelope including around windows or the normal operation of doors. The leakage can be a function of temperature and wind speed and can be expressed as either a total flow rate, a flow rate per floor area, per wall area, or as an air change rate. This input object appears in most example files.
ZoneInfiltration:EffectiveLeakageArea - similar to the previous input object but uses a different equation to express the infiltration rate. The DirectIndirectEvapCoolers.idf file contains an example.
ZoneInfiltration:FlowCoefficient - also similar to the ZoneInfiltration:DesignFlowRate input object but uses yet a different equation.The DirectIndirectEvapCoolers.idf file contains an example.
ZoneVentilation:DesignFlowRate - a method to add outside air to a zone with similar inputs to the ZoneInfiltration:DesignFlowRate but this would represent a purposeful introduction of outdoor air into the space. See the 5ZoneNightVent2.idf example file.
ZoneVentilation:WindandStackOpenArea - describes the natural ventilation driven introduction of outdoor air into the zone using a simpler method than an AirflowNetwork model. The inputs include the opening area and effectiveness as well as simple controls based on zone or outdoor temperature or the difference between the two or wind speed. See the VentilationSimpleTest.idf file.
ZoneMixing, ZoneCrossMixing, and ZoneRefrigerationDoorMixing - these three input objects provide simplified treatments of air exchange between zones.
ZoneEarthtube - provides a way to model an earth tube which is a way to draw outdoor into the zone through an underground pipe in order to cool the air in the summer and heat it in the winter. An example of this input object is in the EarthTubeSimpleTest.idf file.
ZoneCoolTower:Shower - models a passive downdraught evaporative cooling tower (sometimes also called a shower cooling tower or a wind tower) using natural ventilation and water evaporation to providing cooling in typically arid climates. See the CooltowerSimpleTestwithVentilation.idf for an example of this input object.
ZoneThermalChimney - models a passive solar driven thermal chimney that utilize the buoyancy of air heated by the sun to provide ventilation. See the file ThermalChimneyTest.idf.
ZoneAirBalance:OutdoorAir - calculates the combined outdoor airflow including the interactions between mechanical ventilation, infiltration, and duct leakage and is usually applied to residential buildings. See the SingleFamilyHouse_TwoSpeed_ZoneAirBalance.idf file for example.
The input objects described in this section are further explained in the InputOutputReference under the heading “Group-Airflow.”
HVAC Templates[LINK]
New users to EnergyPlus need to learn many things to understand how to create detailed input objects for modeling an HVAC system. In order to reduce this initial effort, HVACTemplates were created. Unlike other input objects, the HVACTemplate input objects are not directly processed by EnergyPlus; instead, a preprocessor called ExpandObjects turns these HVACTemplate input objects into the detailed HVAC input objects. This can be used as a learning tool since you can review the .expidf file that contains the detailed input objects or it can be used for long term modeling especially if your focus is not on HVAC related energy efficiency measures. The primary disadvantage of using the HVACTemplate input objects is that only a small subset of possible configurations can be modeled using them; however, the subset of configurations supported by the HVACTemplate input objects was carefully chosen to be some of the most common HVAC configurations. If the HVACTemplate input objects do not support the HVAC configuration you are considering; you need to model it with the detailed HVAC EnergyPlus input objects. When using HVACTemplate input objects, no regular EnergyPlus input objects related to HVAC should be used (see the InputOutputReference for some exceptions to this). The HVACTemplates can model:
Baseboard heating systems with optional hot water boiler
Fan coil systems with boilers and chillers
Packaged terminal air conditioner (PTAC) system with optional hot water boiler
Packaged terminal air-to-air heat pump (PTHP) systems
Water to air heat pumps with boiler and cooling tower
Variable refrigerant flow heat pumps (air-to-air)
Variable refrigerant flow heat pumps (water-to-air) with boiler and cooling tower
Direct-expansion (DX) cooling, package and split systems
Direct-expansion (DX) heat pump systems
Packaged variable air volume system using direct-expansion cooling
Variable air volume systems with boilers and air-cooled chillers
Variable air volume systems with boilers and water-cooled chillers
Constant air volume systems with boilers and water-cooled chillers
Dual-duct systems (constant or variable air volume) with boilers and water-cooled chillers
Dedicated outdoor air systems (DOAS) combined with zonal template systems
The Input Output Reference includes a list of exactly which input objects are needed for each of these configurations
HVACTemplate:Thermostat - describes the heating and cooling setpoints for a thermostat. This input object can be referenced by multiple HVACTemplate:Zone input objects if all the zones have the same setpoints.
HVACTemplate:Zone:IdealLoadsAirSystem - provides an idealized system that supplies air to the zone that meets all loads and uses no energy. Best used for load calculations.
HVACTemplate:Zone:BaseboardHeat - allows the simulation of electric or hot water thermostatically controlled baseboard heaters.
HVACTemplate:Zone:FanCoil - describes a four-pipe fan coil system with outdoor air intake.
HVACTemplate:Zone:PTAC - models a packaged terminal air conditioner with either electric, gas or hot water heating coil most commonly used in residential or hotel applications.
HVACTemplate:Zone:PTHP - models a packaged terminal heat pump system most commonly used in residential or hotel applications with either electric or gas supplementary heater.
HVACTemplate:Zone:WaterToAirHeatPump - describes the distributed “terminal” portions of a system which uses a medium temperature loop and heat pumps to provide heating and cooling to the building (also see HVACTemplate:Plant:MixedWaterLoop).
HVACTemplate:Zone:VRF - provides input for variable refrigerant flow terminal units.
HVACTemplate:Zone:Unitary - describes a constant volume direct-expansion system such as a rooftop system or split system. Often paired with a single HVACTemplate:System:Unitary for a single zone system but can also be part of a multizone system.
HVACTemplate:Zone:VAV - simulates the terminal of a variable air volume system with reheat.
HVACTemplate:Zone:VAV:FanPowered - simulates either a parallel or series fan power terminal of a variable air volume system.
HVACTemplate:Zone:VAV:HeatAndCool - simulates the terminal of a variable air volume system.
HVACTemplate:Zone:ConstantVolume - simulates the terminal of a constant air volume system.
HVACTemplate:Zone:DualDuct - simulates the zone portion of a constant volume or variable volume dual-duct HVAC system.
HVACTemplate:System:VRF - simulates the variable refrigerant flow system.
HVACTemplate:System:Unitary - describes the system portion of a rooftop or split DX cooling system with electric, gas or hot water heating.
HVACTemplate:System:UnitaryHeatPump:AirToAir - details the system portion of a rooftop or split DX air-to-air heat pump system.
HVACTemplate:System:UnitarySystem - models the system portion of a rooftop or split system and has more flexibility than the previous two input objects.
HVACTemplate:System:VAV - simulates the system portion of a variable air volume HVAC configuration with chilled water cooling and several different heating options.
HVACTemplate:System:PackagedVAV - describes the system portion of a packaged direct-expansion (DX) based variable air volume HVAC configuration with several different heating options.
HVACTemplate:System:ConstantVolume - provides input for the system portion of a constant air volume HVAC configuration with optional chilled water cooling and several different heating options.
HVACTemplate:System:DualDuct - models the system portion of a constant air volume or variable air volume dual-duct HVAC configuration with optional chilled water cooling and several different heating options.
HVACTemplate:System:DedicatedOutdoorAir - adds a dedicated outdoor air system (DOAS) which can be used with several of the HVACTemplate:Zone input objects and contains heating and cooling coils and heat recovery.
HVACTemplate:Plant:ChilledWaterLoop - models the chilled water loop connecting chillers to chilled water coils as well as the condenser water loop that connects chillers with cooling towers.
HVACTemplate:Plant:Chiller - describes a vapor-compression chiller that provides chilled water to the loop.
HVACTemplate:Plant:Tower - models an evaporative cooling tower used to reject heat from chillers.
HVACTemplate:Plant:HotWaterLoop - models the hot water loop connecting boilers to hot water coils.
HVACTemplate:Plant:Boiler - models a boiler that provides hot water to the loop.
HVACTemplate:Plant:MixedWaterLoop - models the medium temperature loop that serves water-to-air heat pumps as well as cooling towers and boilers.
In addition, this group of input objects includes three plant input objects that allow the referencing of chillers, towers, and boilers respectively so that additional details can be described in those input objects. Example for these are in the ExampleFiles directory and start with the name HVACTempate. All of these are described in the “Input/Output Reference” document under the Group “HVACTemplates” and please note that this group is described in Chapter 2 while most of the other groups of input objects are described in Chapter 1. The expansion process is described in the Auxiliary Programs document under “ExpandObjects.”
Detailed HVAC[LINK]
In buildings, HVAC systems are comprised of components such as fans, pumps, coils, chillers and boilers connected by ducts or pipes and controlled by systems using sensors strategically located in the distribution systems and in the zones. In many respects, EnergyPlus mirrors this topology by having a large number of components and a means to describe their connections with one another and their control systems. Every component in an HVAC system must have an inlet and outlet “node.” In the actual system, a node might be a point in the system at which fluid properties can be measured. In an EnergyPlus simulation, the nodes are points at which fluid properties are evaluated and passed on to subsequent equipment. Components are linked together to form various loops within the simulation. Thus, the output node from one component also serves as the inlet node to the next component. Loops are constructed combining the components as well as input objects the describe the arrangement of the components. The figure below shows a generic example of the loop-node concept. Loop nodes are a key defining feature in EnergyPlus. As a result, it is recommended that one of the first steps taken in defining an HVAC system in EnergyPlus be the definition of a node diagram or map. This is helpful for visualization of the entire system.
So that these loops are manageable and more clearly defined both in the input and in the simulation, four different loop sections can be defined in an EnergyPlus input file. In general, these four types are in essence two pairs of loop sections that make up two distinct types of loops: a zone/air loop and a plant loop.
Air Loop Supply Side: The air loop is defined by the section of the zone/air loop that starts after the zone return streams are combined and continues on until just before any air stream(s) are branched off to individual zones. The starting point of the air loop is fairly straightforward. The ending point is slightly more complex but can be understood with some examples. For instance, in a terminal reheat system, the end of the air loop would typically be considered the node following the cooling coil. In a dual duct system, the air loop would have two ending points that would correspond to the nodes after the cooling coil and after the heating coil/humidifier. In most cases, the air loop has a single starting point and up to two ending points (for a two-deck system). An outdoor air subsystem can be included in the supply side for ventilation and relief air.
Air Loop Zone Equipment: The zone equipment section of the input file is defined as more or less the rest of the zone/air loop (outside air is handled separately as a subset of the air loop). This includes everything from where the ducts are split to serve various zones up through where the return ducts from various zones are mixed into a single return duct. Zone equipment can include dampers and reheat coils as well as zone-specific conditioning systems such as thermostatic baseboard or a window air conditioner. Most control issues are typically dealt with in the zone equipment section of the simulation.
Plant Loop Demand Side: One side of the plant is where energy is “demanded” by various components that make up the air loop or zone equipment. Typically, this is the water side of equipment such as coils, baseboard, radiant heating and cooling, etc. In the case of a condenser loop, energy is typically “demanded” by a chiller condenser or other water source heat pump. The demand side of this loop can also include a splitter, a mixer, and a bypass.
Plant Loop Supply Side: The other side of the plant loop is where energy is “supplied” by various components. The components typically found on the supply side include pumps, boilers, chillers, purchased heating and cooling, ice storage, etc. In the case of a condenser, the components would be a cooling tower, fluid cooler, or ground source heat exchanger, etc. As with the demand side, this loop can also include a splitter, a mixer, and a bypass.
The following is a list of groups of input objects related to specifying detailed HVAC systems in EnergyPlus related to zone equipment and secondary systems:
HVAC Design Objects - describes input objects related to how EnergyPlus performs autosizing for air terminals, zone equipment, systems, and plant components as well as for outdoor air systems.
Node-Branch Management - used to describe some of the topological features of EnergyPlus such as nodes, pipes, and ducts as well as branches (pieces of loops) and connectors.
Air Distribution - describes the arrangement of the components in an air distribution system includes the outdoor air system, splitters, mixers, and plenums.
Zone HVAC Controls and Thermostats - input objects related to thermostats and humidistats used to control the conditions in a zone.
Zone HVAC Forced Air Units - defines input related to zone forced air equipment like window air conditioners, packaged terminal air conditions (PTAC), unit heaters, fan coil systems, and outdoor air units as well as other related input objects.
Zone HVAC Radiative/Convective Units - models baseboard systems, low- and high-temperature radiant systems, and active portion of ventilated slabs.
Zone HVAC Air Loop Terminal Units - describes air terminals including constant volume, variable volume, series and parallel powered induction units, and duel duct terminals.
Zone HVAC Equipment Connections - used to describe the HVAC equipment connections at the zone level.
Fans - describes constant volume, variable volume, exhaust fans as well as more system and component model fans.
Coils - contains a long list of input objects to model heating and cooling water coils; heating and cooling DX coils including two-, multiple-, and variable-speed units; variable refrigerant coils; fuel and gas coils; desuperheater coils; air to water heat pump coils; and other coil input objects.
Evaporative Coolers - describes direct and indirect evaporative coolers.
Humidifiers and Dehumidifiers - for electric and gas steam humidifiers as well as desiccant dehumidifiers.
Heat Recovery - models for air-to-air flat plate and combined sensible and latent heat exchangers as well as heat exchangers coupled with desiccants.
Unitary Equipment - describes unitary input objects that are generally placed in the primary air loop and includes heating only, heating and cooling, and air-to-air heat pump input objects.
Variable Refrigerant Flow Equipment - input objects to describe variable refrigerant flow (VRF) equipment as well as the controls.
The following is a list of control systems in EnergyPlus related to HVAC
Controllers - input objects for simple controllers that look at a single node and compare it with the setpoint and includes controllers for water coils, outdoor air, and mechanical ventilation.
System Availability Managers - these input objects can take an input from any node and control whether an entire portion of the HVAC system is active and can be based on temperature, differential temperature, schedules, night cycle, and ventilation.
Setpoint Managers - these take input from any node or nodes and calculate a setpoint at another node and include controls for single zone heating, cooling, or reheat; humidity control; mixed air; warmest or coldest; and many other scenarios.
Plant-Condenser Control - provides control for the plant loop primarily controlling the operation of the loop and which equipment is available and includes control based on heating or cooling load and in reference to outdoor conditions such as dry-bulb or wet-bulb temperature.
Plant-Condenser Flow Control - describes the TemperingValve input object for the special case of flow control with thermal storage systems.
The following is a list of input objects related to primary systems and equipment:
Pumps - describes constant speed and variable speed pumps and headered multiple pump systems.
Plant-Condenser Loops - describes the supply and demand side of the loops the operating temperatures and flow rates.
Plant Heating and Cooling Equipment - used to input the central plant equipment such as steam and hot water boilers; electric, absorption, engine driven, and turbine chillers; and water-to-water heat pumps; as well as connections to district heating and cooling sources.
Condenser Equipment and Heat Exchangers - describes single-, two, and variable speed cooling towers; single and two speed evaporative and non-evaporative fluid coolers; vertical, surface, trench and slinky ground heat exchangers; and fluid-to-fluid heat exchangers.
Non-Zone Equipment - describes the LoadProfile:Plant input object that allows the load on the plant to be specified by schedule if already known.
User Defined HVAC and Plant Component Models - a group that allows the user to define custom models for zonal systems, air terminals, coils, and plant equipment.
The input object groups described in this section are further explained in the InputOutputReference.
Output Reporting[LINK]
The primary goal of modeling is seeing the results of the model contained in the output reporting. EnergyPlus has several different types of outputs, but initially the most important to understand are the tabular output reports that summarize the results of the simulation. The Output:Table:SummaryReports and OutputControl:Table:Style input objects described below are the only two necessary to start generating the tabular output reports:
Output:Table:SummaryReports - allows the specification of different tabular reports but usually just specifying AllSummary is necessary. Additional reports can be shown by specifying AllSummaryAndMonthly, AllSummaryMonthlyAndSizingPeriod.
OutputControl:Table:Style - specifying the output format for the tabular reports which is most commonly HTML but a comma, tab, fixed width, and XML options are also available. Depending on what is specified the output reports can have different file extensions and the file name usually has the word “Table” or “tbl” in it.
You can also create your own custom tabular reports by using one of the following input objects:
Output:Table:TimeBins - shows the amount of time in hours that occurs in different bins for the single specific output variable or meter specified
Output:Table:Monthly - shows a series of output variables or output meters on a monthly basis using different aggregation schemes. For output variables that reoccur for each zone or other input objects, the monthly report will be repeated for each one.
Output:Table:Annual - shows a series of output variables or output meters on an annual basis using different aggregation schemes. For output variables that reoccur for each zone or other input objects, additional rows of results will be displayed.
Output:VariableDictionary - provides a list of available output variables for use with these custom tabular reports as well as the time step reporting described next. The list of output variables that are available for specific simulation appear in a file with a .rdd extension, and the output meters appear in a file with a .mdd extension.
When you need to dive deeper into the results for a specific output variable or output meters, time step outputs allow you to see the values of an output variable for each timestep or other time periods. By looking at multiple output variables and seeing how they change together over time, a deeper understanding of the system and control operation can be gained.
Output:Variable - these input objects are added one for each output variable desired. Usually, an asterisk is used for the “key value” field so that all instances of the output variable are included. The output shows up in the .eso file which is generally converted to a .csv file for use with a spreadsheet.
Output:Meter and Output:Meter:MeterFileOnly - these input objects specify the output meters (think of them as very detailed submeters). The output from these input objects show up in the .mtr file which is generally converted to a Meter.csv file for use with a spreadsheet. Also, note that the .mtd file shows the exact relationship between specific end-use output report variables and each output meter.
Output:SQLite - use this input object if you want to output in the SQLite database format. Not only can the output variables and meters be in SQLite format but the tabular reports are also included.
EnergyPlus also includes a number of special reports that usually appear in different output files or in the .eio output file
Output:Surfaces:List - provides a report on all the surfaces in a file and the output appears in the .eio and .sln output files.
Output:Surfaces:Drawing - provides a DXF drawing that can be opened in some CAD programs .
OutputControl:SurfaceColorScheme - controls the colors used in the DXF file.
Output:Schedules - provides a summary of the schedules in the input file and appears as part of the file with the .eio extension.
Output:Constructions - provides a summary of constructions in the input file and appears as part of the file with the .eio extension.
Output:EnergyManagementSystem - creates a list of detailed output related to the energy management system in a file with the .edd extension.
OutputControl:ReportingTolerances - provides more control over the amount of time reported for the setpoints not being met.
Output:Diagnostics - provides additional detail in the output messages in the .err file . Normally this extra detail is not shown to reduce confusion for new users.
Output:DebuggingData - provides an additional detailed output related to HVAC nodes in a file with a .dbg extension.
Environmental reporting adds new meters showing the emissions related to the building and is triggered by the use of the following three input objects. See the 5ZoneTDV.idf file for examples.
Output:EnvironmentalImpactFactors - specifies the frequency of the output variables related to emissions.
EnvironmentalImpactFactors - specifies the efficiency of district heating and cooling systems as well as the carbon equivalent emission factors for N20, CH4, and CO2.
FuelFactors - for each type of energy resource (electricity, natural gas, etc..) provides a way to enter factors related to source energy and emissions of CO2, CO, CH4, NOx, N20, SO2, PM, NH3, NMVOC, Hg, Pb, and other factors.
Other input objects in this group allow the accumulation of metered results, the combination of output variables or meters to create custom meters, and a method for preprocessors to include error messages in the normal error file. Many example files contain some of these input objects. All of these are described in the “Input/Output Reference” but note that this group is described in Chapter 5 “Input for Output” and Chapter 7 “Standard Output Reports” while most of the other groups of input objects are described in Chapter 1. The OutputDetailsAndExamples documentation provides even more details on the outputs created by each of these input objects. Several other output related input objects appear in other areas such as Output:DaylightFactors input object in the Daylighting group.
Economics[LINK]
EnergyPlus contains several input objects that allow economic analysis to be performed. When these input objects are included in the input file, new tabular output reports are automatically generated. The input objects used by EnergyPlus for cost estimating calculations are as follows:
ComponentCost:LineItem - provides inputs related to determining the construction cost and can be associated with several different input objects and the cost estimate is based on factors such as cost per area or cost per unit of output capacity. It has not been applied to all types of input objects so for many scenarios; construction costing would need to be performed outside of EnergyPlus.
ComponentCost:Adjustments - allows the specification of adjustments including miscellaneous costs per conditioned area, design and engineering fees, contractor fees, contingency, permitting, bonding, and insurance as well as commissioning and regional adjustment fees.
ComponentCost:Reference - entry of reference building costs so that the current model can be compared to the reference building.
For many building projects, while energy estimates are important, the computation of estimated utility bills provides an understanding of how much money is going to be saved to help offset possibly higher initial costs of a high-performance building. Due to the many different utility companies and regulatory agencies, the approach used to compute monthly utility bills has become widely varied and, at times, quite complicated depending not only on energy and demand but the timing of each and the relationship between the two. Overall, the goals of the UtilityCost input objects of EnergyPlus are to make simple tariffs easy to model and complex tariffs possible to model. The 5ZoneEconomicsTariffAndLifeCycleCosts.idf example file provides several different example tariffs. The input objects used by EnergyPlus for the calculation of monthly and annual utility bills are as follows:
UtilityCost:Tariff - sets the parameters for the overall tariff such as associated output meter, conversion factors, demand computation, monthly charges, and minimum charges, and schedule names for the time of use periods, seasons, billing cycle, and real-time pricing.
UtilityCost:Qualify - provides a method to qualify if a tariff applies to the building being modeled since utilities provide limits usually based on peak demand or energy consumption for each tariff.
UtilityCost:Charge:Simple - defines cost per unit value for a charge based on energy or demand or other charges for a specific season. The charges are arranged in a hierarchy shown in Figure X Hierarchy of Economic Charges.
UtilityCost:Charge:Block - defines a more complicated but common type of charge for energy or demand where the costs are defined in the tariff with blocks of charges (i.e., the first 1000 kWh is one cost per kWh, the next 5000 kWh is a second cost, and remaining kWh is a third cost). Like UtilityCost:Charge:Simple, the charges use the same hierarchy.
UtilityCost:Ratchet - some utilities charge not only for the current month’s demand but also compensate for the highest demand in recent months, and this input object allows the specification of such a structure.
The following two input objects are uncommon to use:
UtilityCost:Variable - allows the specific specification of a monthly variable to be used in the calculation of the tariff.
UtilityCost:Computation - provides the step-by-step specification of the steps needed to compute the tariff. The output report tariff summary includes the default computation steps for the input objects specified.
Life-cycle costing allows the combination of initial and future costs (typically energy bills) to be understood using a single metric so that multiple building energy models can be compared even if they all have different initial and future costs. The input objects used for performing a life-cycle cost analysis are:
LifeCycleCost:Parameters - describes the discount, tax, and inflation rates, the approach used for inflation and discounting, as well as the base date and length of the study period and other parameters related to life-cycle costing.
LifeCycleCost:RecurringCosts - used to enter reoccurring costs other than costs related to energy and water usage since those are included automatically.
LifeCycleCost:NonrecurringCost - used to enter costs that occur only once during the study period.
LifeCycleCost:UsePriceEscalation - specifies the annual escalation of energy costs in future years and is generally based on government predictions. The increases in energy costs for future years are assuming they change differently than inflation. A file that is updated each year begins with the name LCCusePriceEscalationDataSet is included in the DataSets directory and is based on supplements to the NIST 135 handbook.
Two less commonly used input objects are
LifeCycleCost:UseAdjustment - allows manual adjustment of energy or water costs in future years.
CurrencyType - specifies the currency symbol of the monetary unit. If it is not included a dollar sign ‘$’ is used in all reports.
All of these are described in the “Input/Output Reference” but note that this group is described in Chapter 3 “EnergyPlus Economics” while most of the other groups of input objects are described in Chapter 1. The OutputDetailsAndExamples documentation provides even more details on the tabular outputs created in the section labeled “eplustbl.<ext>”.
Other Groups of Input Objects[LINK]
The previous sections describe major groups of input objects. This section briefly covers some of the remaining input object groups.
Detailed Ground Heat Transfer - provides an alternative way of describing ground heat transfer through basement walls and floors and slabs using input objects that are then processed by the SLAB and BASEMENT programs and is also documented in AuxiliaryPrograms.
Energy Management System (EMS) - a high-level control method that connects sensors and actuators with a simple control programming language and is also documented in the EMSApplicationGuide.
External Interface - allows the connection of EnergyPlus using co-simulation by the import of Functional Mockup Units (FMUs) and is also documented in the ExternalInterfacesApplicationGuide.
Operational Faults - provides for the modeling of operation problems in sensors, controllers, meters, equipment, and systems and is commonly used with existing buildings.
General Data Entry - contains the Matrix:TwoDimension input object used with the Construction:ComplexFenestrationState input object.
Performance Curves - allows the specification of polynomial curves used to characterize the performance of HVAC equipment.
Performance Tables - allows the specification of tables used to characterize the performance of HVAC equipment.
Fluid Properties - describes the detailed properties of refrigerants and glycols.
Demand Limiting Controls - provides a way of implementing management of the systems of the building to regulate the peak demand.
Natural Ventilation and Duct Leakage - provides a way to model multizone airflows driven by wind and forced air systems (shown under Group-Airflow Network in the InputOutputReference).
Room Air Models - allows the description of non-uniform room air temperatures (not fully mixed).
Compliance Objects - provides an input object that allows rotation of the building when used for compliance purposes.
Parametrics - allows for simple parametric cases to be defined within an input file using input objects. Makes use of the ParametricPreprocessor as described in the AuxiliaryPrograms document.
Refrigeration - describes supermarket and warehouse refrigeration systems.
Electric Load Center-Generator Specifications - allows the specification of fuel and photovoltaic generators and controls on when they should be used to provide power to the facility.
Water Systems - contains input objects to describe the use of water in the building including from wells, rain, and storage.
Solar Collectors - describes various systems that convert solar energy into thermal energy including those that are integrated with photovoltaic systems.
Water Heaters and Thermal Storage - describes systems that provide water heating and storage as well as ice and chilled water storage.
Documentation content copyright © 1996-2020 The Board of Trustees of the University of Illinois and the Regents of the University of California through the Ernest Orlando Lawrence Berkeley National Laboratory. All rights reserved. EnergyPlus is a trademark of the US Department of Energy.
This documentation is made available under the EnergyPlus Open Source License v1.0.