Window Heat Balance Calculation[LINK]
Table: Fortran Variables used in Window Heat Balance Calculations
Mathematical variable|Description|Units||FORTRAN variable ———————|———–|—–||—————- N|Number of glass layers|-|nlayer σ|Stefan-Boltzmann constant||sigma εi|Emissivity of face i|-|emis ki|Conductance of glass layer i|W/m2-K|scon ho, hi|Outside, inside air film convective conductance|W/m2-K|hcout, hcout hj|Conductance of gap j|W/m2-K|hgap To, Ti|Outdoor and indoor air temperatures|K|tout, tin Eo, Ei|Exterior, interior long-wave radiation incident on window|W/m2|outir, rmir θi|Temperature of face i|K|thetas Si|Radiation (short-wave, and long-wave from zone internal sources) absorbed by face i|W/m2|AbsRadGlassFace Iextbm|Exterior beam normal solar irradiance|W/m2|BeamSolarRad Iextdif|Exterior diffuse solar irradiance on glazing|W/m2|- Iintsw|Interior short-wave radiation (from lights and from reflected diffuse solar) incident on glazing from inside|W/m2|QS Iintlw|Long-wave radiation from lights and equipment incident on glazing from inside|W/m2|QL φ|Angle of incidence|radians|- Afj|Front beam solar absorptance of glass layer j|-|- Ajf,dif, Ajb,dif|Front and back diffuse solar absorptance of glass layer j|-|AbsDiff, AbsDiffBack A, B|Matrices used to solve glazing heat balance equations|W/m2, W/m2-K|Aface, Bface hr,i|Radiative conductance for face i|W/m2-K|hr(i) Δθi|Difference in temperature of face i between successive iterations|K|-
The Glazing Heat Balance Equations[LINK]
The window glass face temperatures are determined by solving the heat balance equations on each face every time step. For a window with N glass layers there are 2N faces and therefore 2N equations to solve. Figure 91 shows the variables used for double glazing (N=2).
The following assumptions are made in deriving the heat balance equations:
- The glass layers are thin enough (a few millimeters) that heat storage in the glass can be neglected; therefore, there are no heat capacity terms in the equations.
- The heat flow is perpendicular to the glass faces and is one dimensional. See “Edge of Glass Corrections,” below, for adjustments to the gap conduction in multi-pane glazing to account for 2-D conduction effects across the pane separators at the boundaries of the glazing.
- The glass layers are opaque to IR. This is true for most glass products. For thin plastic suspended films this is not a good assumption, so the heat balance equations would have to be modified to handle this case.
- The glass faces are isothermal. This is generally a good assumption since glass conductivity is very high.
- The short wave radiation absorbed in a glass layer can be apportioned equally to the two faces of the layer.
The four equations for double-glazing are as follows. The equations for single glazing (N=1) and for N=3 and N=4 are analogous and are not shown.
Absorbed Radiation[LINK]
Si in Equations to is the radiation (short-wave and long-wave from zone lights and equipment) absorbed on the ith face. Short-wave radiation (solar and short-wave from lights) is assumed to be absorbed uniformly along a glass layer, so for the purposes of the heat balance calculation it is split equally between the two faces of a layer. Glass layers are assumed to be opaque to IR so that the thermal radiation from lights and equipment is assigned only to the inside (room-side) face of the inside glass layer. For N glass layers Si~~is given by
Here
= exterior beam normal solar irradiance
= exterior diffuse solar incident on glazing from outside
= interior short-wave radiation (from lights and from reflected diffuse solar) incident on glazing from inside
= long-wave radiation from lights and equipment incident on glazing from inside
= emissivity (thermal absorptance) of the room-side face of the inside glass layer
Room-Side Convection[LINK]
The correlation for room-side convection coefficient,
, is from ISO 15099 section 8.3.2.2. (Prior to EnergyPlus version 3.1, the value for
was modeled using the “Detailed” algorithm for opaque surface heat transfer, e.g. for a vertical surface
; see section Detailed Natural Convection Algorithm). The ISO 15099 correlation is for still room air and is determined in terms of the Nusselt number,
, where
where,
is the thermal conductivity of air, and
is the height of the window.
The Rayleigh number based on height,
, is calculated using,
where,
is the density of air
is the acceleration due to gravity,
is the specific heat of air,
is the dynamic viscosity of air, and
is the mean film temperature in Kelvin given by,
There are four cases for the Nusselt correlation that vary by the tilt angle in degrees,
, and are based on heating conditions. For cooling conditions (where
) the tilt angle is complemented so that 
Case A. 
Case B. 
Case C. 
Case D. 
The material properties are evaluated at the mean film temperature. Standard EnergyPlus pyschrometric functions are used for
and
. Thermal conductivity is calculated using,
.
Kinematic viscosity is calculated using,
.
This correlation depends on the surface temperature of the room-side glazing surface and is therefore included inside the window heat balance interation loop.
Solving the Glazing Heat Balance Equations[LINK]
The equations are solved as follows:
- Linearize the equations by defining
. For example, Equation becomes
- Write the equations in the matrix form
- Use previous time step’s values of
as initial values for the current time step. For the first time step of a design day or run period the initial values are estimated by treating the layers as a simple RC network.
- Save the
for use in the next iteration:
- Using
, reevaluate the room-side face surface convection coefficient
- Using the
to evaluate the radiative conductances
- Find the solution
by LU decomposition
- Perform relaxation on the the new
:
- Go to step 4
Repeat steps 4 to 9 until the difference,
, between values of the
in successive iterations is less than some tolerance value. Currently, the test is
If this test does not pass after 100 iterations, the tolerance is increased to 0.2K. If the test still fails the program stops and an error message is issued.
The value of the inside face temperature,
, determined in this way participates in the zone heat balance solution (see Outdoor/Exterior Convection) and thermal comfort calculation (see Occupant Thermal Comfort).
Edge-Of-Glass Effects[LINK]
Table: Fortran Variables used in Edge of Glass calculations
Mathematical variable|Description|Units||FORTRAN variable ———————|———–|—–||—————-
|Area-weighted net conductance of glazing including edge-of-glass effects|W/m2-K|- Acg|Area of center-of-glass region|m2|CenterGlArea Afe|Area of frame edge region|m2|FrameEdgeArea Ade|Area of divider edge region|m2|DividerEdgeArea Atot|Total glazing area|m2|Surface%Area hcg|Conductance of center-of-glass region (without air films)|W/m2-K|- hfe|Conductance of frame edge region (without air films)|W/m2-K|- hde|Conductance of divider edge region (without air films)|W/m2-K|- hck|Convective conductance of gap k|W/m2-K|- hrk|Radiative conductance of gap k|W/m2-K|- η|Area ratio|-|- α|Conductance ratio|-|FrEdgeToCenterGlCondRatio, DivEdgeToCenterGlCondRatio
Because of thermal bridging across the spacer separating the glass layers in multi-pane glazing, the conductance of the glazing near the frame and divider, where the spacers are located, is higher than it is in the center of the glass. The area-weighted net conductance (without inside and outside air films) of the glazing in this case can be written
where
hcg = conductance of center-of-glass region (without air films)
hfe~~= conductance of frame edge region (without air films)
hde = conductance of divider edge region (without air films)
Acg = area of center-of-glass region
Afe = area of frame edge region
Ade = area of divider edge region
Atot = total glazing area = 
The different regions are shown in Figure 92:
Figure 92: Different types of glass regions.
Equation can be rewritten as
where
The conductance ratios
and
are user inputs obtained from Window 5. They depend on the glazing construction as well as the spacer type, gap width, and frame and divider type.
In the EnergyPlus glazing heat balance calculation effective gap convective conductances are used to account for the edge-of-glass effects. These effective conductances are determined as follows for the case with two gaps (triple glazing). The approach for other numbers of gaps is analogous.
Neglecting the very small resistance of the glass layers, the center-of-glass conductance (without inside and outside air films) can be written as
where
convective conductance of the kth^^gap
radiative conductance of the kth^^gap
emissivity of the faces bounding the gap
temperature of faces bounding the gap (K)
Equation then becomes
We can also write
in terms of effective convective conductances of the gaps as
Comparing Eqs. and we obtain
Using
gives
This is the expression used by EnergyPlus for the gap convective conductance when a frame or divider is present.
Apportioning of Absorbed Short-Wave Radiation in Shading Device Layers[LINK]
If a shading device has a non-zero short-wave transmittance then absorption takes place throughout the shading device layer. The following algorithm is used to apportion the absorbed short-wave radiation to the two faces of the layer. Here f1 is the fraction assigned to the face closest to the incident radiation and f2 is the fraction assigned to the face furthest from the incident radiation.
Otherwise
Window Frame and Divider Calculation[LINK]
For the zone heat balance calculation the inside surface temperature of the frame and that of the divider are needed. These temperatures are determined by solving the heat balance equations on the inside and outside surfaces of the frame and divider.
Table: Fortran Variables used in Window/Frame and Divider calculations
Mathematical variable|Description|Units||FORTRAN variable ———————|———–|—–||—————- QExtIR,abs|IR from the exterior surround absorbed by outside frame surfaces|W|- QIR,emitted|IR emitted by outside frame surfaces|W|- Qconv|Convection from outside air to outside frame surfaces|W|- Qcond|Conduction through frame from inside frame surfaces to outside frame surfaces|W|- Qabs|Solar radiation plus outside glass IR absorbed by outside of frame|W|- Qdifabs,sol|Diffuse solar absorbed by outside frame surfaces, per unit frame face area|W/ m2|- Qbmabs,sol|Beam solar absorbed by outside frame surfaces, per unit frame face area|W/ m2|- Idifext|Diffuse solar incident on window|W/ m2|- Ibmext|Direct normal solar irradiance|W/ m2|- αfrsol|Solar absorptance of frame|-|FrameSolAbsorp Rglf,dif|Front diffuse solar reflectance of glazing|-| Rglf,bm|Front beam solar reflectance of glazing|-| cos(βface)|Cosine of angle of incidence of beam solar on frame outside face ||CosIncAng Cos(βh)|Cosine of angle of incidence of beam solar on frame projection parallel to window x-axis|-|CosIncAngHorProj Cos(βv)|Cosine of angle of incidence of beam solar on frame projection parallel to window y-axis|-|CosIncAngVertProj fsunlit|Fraction of window that is sunlit|-|SunlitFrac Af|Area of frame’s outside face (same as area of frame’s inside face)|m2|- Ap1, Ap2|Area of frame’s outside and inside projection faces|m2|- Ff|Form factor of frame’s outside or inside face for IR|-|- Fp1, Fp2|Form factor of frame outside projection for exterior IR; form factor of frame inside projection for interior IR |-|- Eo|Exterior IR incident on window plane|W/m2|outir Ei|Interior IR incident on window plane|W/m2|SurroundIRfromParentZone ε1, ε2|Outside, inside frame surface emissivity|-|FrameEmis θ1, θ2|Frame outside, inside surface temperature|K|FrameTempSurfOut, FrameTempSurfIn To, Ti|Outdoor and indoor air temperatures|K|tout, tin ho,c, hi,c|Frame outside and inside air film convective conductance|W/m2-K|HOutConv, HInConv k|Effective inside-surface to outside-surface conductance of frame per unit area of frame projected onto window plane|W/m2-K|FrameConductance, FrameCon S1|Qabs/Af|W/m2-K|FrameQRadOutAbs S2|Interior short-wave radiation plus interior IR from internal sources absorbed by inside of frame divided by Af|W/m2-K|FrameQRadInAbs η1, η2|Ap1/Af, Ap2/Af|-|- H|Height of glazed portion of window|m|Surface%Height W|Width of glazed portion of window|m|Surface%Width wf, wd|Frame width, divider width|m|FrameWidth, DividerWidth pf1, pf2|Frame outside, inside projection|m|FrameProjectionOut, FrameProjectionIn Nh, Nv|Number of horizontal, vertical dividers|-|HorDividers, VertDividers To,r, Ti,r|Frame outside, inside radiative temperature|K|TOutRadFr, TInRadFr ho,r, hi,r|Frame outside, inside surface radiative conductance|W/m2-K|HOutRad, HInRad A|Intermediate variable in frame heat balance solution|K|Afac C|Intermediate variable in frame heat balance solution|-|Efac B, D|Intermediate variables in frame heat balance solution|-|Bfac, Dfac
Frame Temperature Calculation[LINK]
Figure 93 shows a cross section through a window showing frame and divider. The outside and inside frame and divider surfaces are assumed to be isothermal. The frame and divider profiles are approximated as rectangular since this simplifies calculating heat gains and losses (see “Error Due to Assuming a Rectangular Profile,” below).
Frame Outside Surface Heat Balance[LINK]
The outside surface heat balance equation is
where
= IR from the exterior surround (sky and ground) absorbed by outside frame surfaces
= IR emitted by outside frame surfaces
= convection from outside air to outside frame surfaces
= conduction through frame from inside frame surfaces to outside frame surfaces
= solar radiation (from sun, sky and ground) plus IR from outside window surface absorbed by outside frame surfaces (see “Calculation of Absorbed Solar Radiation,” below).
The first term can be written as the sum of the exterior IR absorbed by the outside face of the frame and the exterior IR absorbed by the frame’s outside projection surfaces.
where ε1 is the outside surface emissivity.
The exterior IR incident on the plane of the window, Eo, is the sum of the IR from the sky, ground and obstructions. For the purposes of the frame heat balance calculation it is assumed to be isotropic. For isotropic incident IR, Ff = 1.0 and Fp1 = 0.5, which gives
The IR emitted by the outside frame surfaces is
The convective heat flow from the outside air to the outside frame surfaces is
The conduction through the frame from inside to outside is
Note that Af is used here since the conductance, k, is, by definition, per unit area of frame projected onto the plane of the window.
Adding these expressions for the Q terms and dividing by Af gives
where S1 = Qabs/Af and
We linearize Eq. as follows.
Write the first two terms as
and define a radiative temperature
This gives
which, within a few percent, equals
Defining an outside surface radiative conductance as follows
then gives
The final outside surface heat balance equation in linearized form is then
Frame Inside Surface Heat Balance[LINK]
A similar approach can be used to obtain the following linearized inside surface heat balance equation:
where
and Ei is the interior IR irradiance incident on the plane of the window.
Solving Eqs. and simultaneously gives
with
Calculation of Solar Radiation Absorbed by Frame[LINK]
The frame outside face and outside projections and inside projections absorb beam solar radiation (if sunlight is striking the window) and diffuse solar radiation from the sky and ground. For the outside surfaces of the frame, the absorbed diffuse solar per unit frame face area is
If there is no exterior window shade, Idifext includes the effect of diffuse solar reflecting off of the glazing onto the outside frame projection, i.e.,
The beam solar absorbed by the outside face of the frame, per unit frame face area is
The beam solar absorbed by the frame outside projection parallel to the window x-axis is
Here it is assumed that the sunlit fraction, fsunlit, for the window can be applied to the window frame. Note that at any given time beam solar can strike only one of the two projection surfaces that are parallel to the window x-axis. If there is no exterior window shade, Ibmext includes the effect of beam solar reflecting off of the glazing onto the outside frame projection, i.e.,
The beam solar absorbed by the frame outside projection parallel to the window y-axis is
Using a similar approach, the beam and diffuse solar absorbed by the inside frame projections is calculated, taking the transmittance of the glazing into account.
Error Due to Assuming a Rectangular Profile[LINK]
Assuming that the inside and outside frame profile is rectangular introduces an error in the surface heat transfer calculation if the profile is non-rectangular. The percent error in the calculation of convection and emitted IR is approximately 100
, where Lprofile,rect is the profile length for a rectangular profile (wf + pf1 for outside of frame or wf + pf2 for inside of frame) and Lprofile,actual is the actual profile length. For example, for a circular profile vs a square profile the error is about 22%. The error in the calculation of absorbed beam radiation is close to zero since the beam radiation intercepted by the profile is insensitive to the shape of the profile. The error in the absorbed diffuse radiation and absorbed IR depends on details of the shape of the profile. For example, for a circular profile vs. a square profile the error is about 15%.
Divider Temperature Calculation[LINK]
The divider inside and outside surface temperatures are determined by a heat balance calculation that is analogous to the frame heat balance calculation described above.
Beam Solar Reflection from Window Reveal Surfaces[LINK]
This section describes how beam solar radiation that is reflected from window reveal surfaces is calculated. Reflection from outside reveal surfaces—which are associated with the setback of the glazing from the outside surface of the window’s parent wall—increases the solar gain through the glazing. Reflection from inside reveal surfaces—which are associated with the setback of the glazing from the inside surface of the window’s parent wall—decreases the solar gain to the zone because some of this radiation is reflected back out of the window.
The amount of beam solar reflected from reveal surfaces depends, among other things, on the extent to which reveal surfaces are shadowed by other reveal surfaces. An example of this shadowing is shown in Figure 94. In this case the sun is positioned such that the top reveal surfaces shadow the left and bottom reveal surfaces. And the right reveal surfaces shadow the bottom reveal surfaces. The result is that the left/outside, bottom/outside, left/inside and bottom/inside reveal surfaces each have sunlit areas. Note that the top and right reveal surfaces are facing away from the sun in this example so their sunlit areas are zero.
The size of the shadowed areas, and the size of the corresponding illuminated areas, depends on the following factors:
- The sun position relative to the window
- The height and width of the window
- The depth of the outside and inside reveal surfaces
We will assume that the reveal surfaces are perpendicular to the window plane and that the window is rectangular. Then the above factors determine a unique shadow pattern. From the geometry of the pattern the shadowed areas and corresponding illuminated areas can be determined. This calculation is done in subroutine CalcBeamSolarReflectedFromWinRevealSurface in the SolarShading module. The window reveal input data is specified in the WindowProperty:FrameAndDivider object expect for the depth of the outside reveal, which is determined from the vertex locations of the window and its parent wall.
If an exterior shading device (shade, screen or blind) is in place it is assumed that it blocks beam solar before it reaches outside or inside reveal surfaces. Correspondingly, it is assumed that an interior or between-glass shading device blocks beam solar before it reaches inside reveal surfaces.
Representative shadow patterns are shown in Figure 95 for a window with no shading device, and without and with a frame. The case with a frame has to be considered separately because the frame can cast an additional shadow on the inside reveal surfaces.
The patterns shown apply to both vertical and horizontal reveal surfaces. It is important to keep in mind that, for a window of arbitrary tilt, if the left reveal surfaces are illuminated the right surfaces will not be, and vice versa. And if the bottom reveal surfaces are illuminated the top surfaces will not be, and vice versa. (Of course, for a vertical window, the top reveal surfaces will never be illuminated by beam solar if the reveal surfaces are perpendicular to the glazing, as is being assumed.
For each shadow pattern in Figure 95, equations are given for the shadowed areas
and
of the outside and inside reveal surfaces, respectively. The variables in these equations are the following (see also Figure 96):
= depth of outside reveal, measured from the outside plane of the glazing to the edge of the reveal, plus one half of the glazing thickness.
= depth of inside reveal (or, for illumination on bottom reveal surfaces, inside sill depth), measured from the inside plane of the glazing to the edge of the reveal or the sill, plus one half of the glazing thickness.
= window height for vertical reveal surfaces or window width for horizontal reveal surfaces
= vertical solar profile angle for shadowing on vertical reveal surfaces or horizontal solar profile angle for shadowing on horizontal reveal surfaces.
= distance from outside (inside) surface of frame to glazing midplane.
= depth of shadow cast by top reveal on bottom reveal, or by left reveal on right reveal, or by right reveal on left reveal.
= depth of shadow cast by frame.
For simplicity it is assumed that, for the case without a frame, the shadowed and illuminated areas extend into the glazing region. For this reason,
and
are measured from the midplane of the glazing. For the case with a frame, the beam solar absorbed by the surfaces formed by the frame outside and inside projections perpendicular to the glazing is calculated as described in “Window Frame and Divider Calculation: Calculation of Solar Radiation Absorbed by Frame.”
The following logic gives expressions for the shadowed areas for all possible shadow patterns. Here:
d1 = 
d2 = 
P1 = 
P2 = 
f1 = 
f2 = 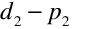
d2prime = 
d2prime2 = 
d12 = 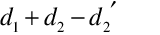
TanAlpha = 
A1sh = 
A2sh = 
L = 
L1 = average distance to frame of illuminated area of outside reveal (used to calculate view factor to frame).
L2 = average distance to frame of illuminated area of inside reveal (used to calculate view factor to frame).
IF(window does not have a frame) THEN
IF(d2prime <= d2) THEN
IF(d12*TanAlpha <= L) THEN
A1sh = 0.5*TanAlpha*d1**2
A2sh = d2prime*L + 0.5*TanAlpha*d12**2 - A1sh
ELSE ! d12*TanAlpha > L
IF(d1*TanAlpha <= L) THEN
A1sh = 0.5*TanAlpha*d1**2
A2sh = d2*L - 0.5*TanAlpha*(L/TanAlpha - d1)**2
ELSE ! d1*TanAlpha > L
A1sh = d1*L - (0.5/TanAlpha)*L**2
A2sh = d2*L
END IF
END IF
ELSE ! d2prime > d2
A2sh = d2*L
IF(d2prime < d1+d2) THEN
IF(d12*TanAlpha <= L) THEN
A1sh = L*(d2prime-d2) + 0.5*TanAlpha*d12**2
ELSE ! d12*TanAlpha > L
A1sh = d1*L - 0.5*L**2/TanAlpha
END IF
ELSE ! d2prime >= d1+d2
A1sh = d1*L
END IF
END IF
ELSE ! Window has a frame
f1 = d1-P1
f2 = d2-P2
d2prime2 = FrameWidth/TanGamma
IF(vertical reveal) THEN ! Vertical reveal
IF(InsReveal+0.5*GlazingThickness <= P2) d2 = P2 + 0.001
ELSE ! Horizontal
IF(bottom reveal surfaces may be illuminated) THEN
! Bottom reveal surfaces may be illuminated
IF(InsSillDepth+0.5*GlazingThickness<=P2) d2= P2 + 0.001
ELSE
! Top reveal surfaces may be illuminated
IF(InsReveal+0.5*GlazingThickness <= P2) d2 = P2 + 0.001
END IF
END IF
IF(d2prime <= f2) THEN
! Shadow from opposing reveal does not go beyond inside ! surface of frame
IF(d12*TanAlpha <= L) THEN
A1sh = 0.5*TanAlpha*f1**2
L1 = f1*(f1*TanAlpha/(6*L)+0.5)
IF(d2-(d2prime+d2prime2+P2) >= 0.) THEN
A2sh = (d2prime+d2prime2)*L + &
0.5*TanAlpha*((d1+d2-d2prime)**2-d1+p2+d2prime2)**2)
L2 = d2prime2 + 0.5*(d2-(d2prime+d2prime2+P2))
ELSE ! d2-(d2prime+d2prime2+P2) < 0.
! Inside reveal is fully shadowed by frame and/or !opposing reveal
A2sh = f2*L
L2 = f2
END IF
ELSE ! d12*TanAlpha >= L
IF((d1+P2)*TanAlpha <= L) THEN
A1sh = 0.5*TanAlpha*f1**2
L1 = f1*((f1*TanAlpha)/(6*L) + 0.5)
IF((d1+P2+d2prime2)*TanAlpha >= L) THEN
A2sh = f2*L
L2 = f2
ELSE ! (d1+P2+d2prime2)*TanAlpha < L
A2sh = f2*L - 0.5*(L-(d1+P2)*TanAlpha)**2/TanAlpha & + d2prime2*(L-(d1+P2+d2prime2/2)*TanAlpha)
L2 = d2prime2 + (L/TanAlpha - (d1+P2+d2prime2))/3
END IF
ELSE ! (d1+P2)*TanAlpha > L
L2 = f2
A2sh = f2*L
IF(f1*TanAlpha <= L) THEN
A1sh = 0.5*TanAlpha*f1**2
L1 = f1*((f1*TanAlpha)/(6*L) + 0.5)
ELSE ! f1*TanAlpha > L
A1sh = f1*L - 0.5*L**2/TanAlpha
L1 = f1-(L/TanAlpha)/3
END IF
END IF
END IF
ELSE ! d2prime > f2 -- Shadow from opposing reveal goes beyond ! inside of frame
A2sh = f2*L
L2 = f2
IF(d2prime >= d1+d2) THEN
A1sh = 0.0
L1 = f1
ELSE ! d2prime < d1+d2
IF(d2prime <= d2+P1) THEN
IF(f1*TanAlpha <= L) THEN
A1sh = 0.5*TanAlpha*f1**2
L1 = f1*((f1*TanAlpha)/(6*L) + 0.5)
ELSE ! f1*TanAlpha > L
A1sh = f1*L - 0.5*L**2/TanAlpha
L1 = f1 - (L/TanAlpha)/3
END IF
ELSE ! d2prime > d2+P1
IF(d12*TanAlpha <= L) THEN
A1sh = L*(d2prime-(d2+P1)) + 0.5*TanAlpha*d12**2
L1 = (L*(f1-d12/2)-d12*TanAlpha* & (f1/2-d12/3))/(L-d12*TanAlpha/2)
ELSE ! d12*TanAlpha > L
A1sh = f1*L - 0.5*L**2/TanAlpha
L1 = f1 - (L/TanAlpha)/3
END IF
END IF
END IF
END IF
FracToGlassOuts = 0.5*(1.0 - ATAN(FrameWidth/L1)/PiOvr2)
FracToGlassIns = 0.5*(1.0 - ATAN(FrameWidth/L2)/PiOvr2)
END IF ! End of check if window has frame
The beam solar reflected from a sunlit region of area
is given by
where
= reflected solar radiation [W]
= beam normal irradiance [W/m2]
= sunlit area [m2]
= beam solar angle of incidence on reveal surface
= solar absorptance of reveal surface
All reflected radiation is assumed to be isotropic diffuse. For outside reveal surfaces it is assumed that
goes toward the window and
goes to the exterior environment. Of the portion that goes toward the window a fraction
goes toward the frame, if present, and
goes toward the glazing.
The view factor
to the frame calculated by assuming that the illuminated area can be considered to be a line source. Then the area-weighted average distance,
, of the source to the frame is calculated from the shape of the illuminated area (see above psuedo-code). Then
is related as follows to the average angle subtended by the frame of width
:
For the portion going towards the frame,
is absorbed by the frame (where
is the solar absorptance of the frame) and contributes to the frame heat conduction calculation. The rest,
, is assumed to be reflected to the exterior environment.
If the glazing has diffuse transmittance
, diffuse front reflectance
, and layer front absorptance
, then, of the portion,
, that goes toward the glazing,
is transmitted to the zone,
is absorbed in glass layer
and contributes to the glazing heat balance calculation, and
is reflected to the exterior environment.
The beam solar absorbed by an outside reveal surface is added to the other solar radiation absorbed by the outside of the window’s parent wall.
For inside reveal surfaces it is assumed that
goes towards the window and
goes into the zone. Of the portion that goes toward the window a fraction
goes toward the frame, if present, and
goes toward the glazing (
is calculated using a method analogous to that used for
). For the portion going towards the frame,
is absorbed by the frame and contributes to the frame heat conduction calculation. The rest,
, is assumed to be reflected back into the zone.
If the glazing has diffuse back reflectance
, and layer back absorptance
, then, of the portion
that goes toward the glazing,
is transmitted back out the glazing,
is absorbed in glass layer
and contributes to the glazing heat balance calculation, and
is reflected into the zone.
The beam solar absorbed by an inside reveal surface is added to the other solar radiation absorbed by the inside of the window’s parent wall.
Shading Device Thermal Model[LINK]
Shading devices in EnergyPlus can be on the exterior or interior sides of the window or between glass layers. The window shading device thermal model accounts for the thermal interactions between the shading layer (shade, screen or blind) and the adjacent glass, and between the shading layer and the room (for interior shading) or the shading layer and the outside surround (for exterior shading).
An important feature of the shading device thermal model is calculating the natural convection airflow between the shading device and glass. This flow affects the temperature of the shading device and glazing and, for interior shading, is a determinant of the convective heat gain from the shading layer and glazing to the zone air. The airflow model is based on one described in the ISO Standard 15099, “Thermal Performance of Windows, Doors and Shading Devices—Detailed Calculations” [ISO15099, 2001]. (Between-glass forced airflow is also modeled; see “Airflow Windows.”)
The following effects are considered by the shading device thermal model:
- For interior and exterior shading device: Long-wave radiation (IR) from the surround absorbed by shading device, or transmitted by the shading device and absorbed by the adjacent glass. For interior shading the surround consists of the other zone surfaces. For exterior shading the surround is the sky and ground plus exterior shadowing surfaces and exterior building surfaces “seen” by the window.
- Inter-reflection of IR between the shading device and adjacent glass.
- Direct and diffuse solar radiation absorbed by the shading device.
- Inter-reflection of solar radiation between shading layer and glass layers.
- Convection from shading layer and glass to the air in the gap (or, for between-glass shading, gaps) between the shading layer and adjacent glass, and convection from interior shading layer to zone air or from exterior shading layer to outside air.
- Natural convection airflow in the gap (or, for between-glass shading, gaps) between shading layer and adjacent glass induced by buoyancy effects, and the effect of this flow on the shading-to-gap and glass-to-gap convection coefficients.
- For interior shading, convective gain (or loss) to zone air from gap airflow.
In the following it is assumed that the shading device, when in place, covers the glazed part of the window (and dividers, if present) and is parallel to the glazing. For interior and exterior shading devices it is assumed that the shading layer is separated from the glazing by an air gap. A between-glass shading layer is assumed to be centered between two glass layers and separated from the adjacent glass layers by gaps that is filled with the same gas. If the window has a frame, it is assumed that the shading device does not cover the frame.
Heat Balance Equations for Shading Device and Adjacent Glass[LINK]
If a window shading device is deployed the heat balance equations for the glass surfaces facing the shading layer are modified, and two new equations, one for each face of the shading layer, are added. Figure 97 illustrates the case of double glazing with an interior shading device.
The heat balance equation for the glass surface facing the gap between glass and shading layer (called in the following, “gap”) is
where
τsh = IR diffuse transmittance of shading device
εsh = diffuse emissivity of shading device
ρsh = IR diffuse reflectance of shading device ( = 1 - ( τsh + εsh))
θ5 = temperature of the surface of the shading layer that faces the gap (K).
The term 1 – ρ4 ρsh accounts for the inter-reflection of IR radiation between glass and shading layer.
The convective heat transfer from glass layer #2 to the air in the gap is
where
Tgap = effective mean temperature of the gap air (K).
hcv = convective heat transfer coefficient from glass or shading layer to gap air (W/m2K).
The corresponding heat transfer from shading layer to gap air is
The convective heat transfer coefficient is given by
where
hc = surface-to-surface heat transfer coefficient for non-vented (closed) cavities (W/m2K)
v = mean air velocity in the gap (m/s).
The quantities hcv and Tgap depend on the airflow velocity in the gap, which in turn depends on several factors, including height of shading layer, glass/shading layer separation (gap depth), zone air temperature for interior shading or outside air temperature for exterior shading, and shading layer and glass face temperatures. The calculation of hcv and Tgap is described in the following sections.
The heat balance equation for the **shading layer surface facing the gap is
where
ksh = shading layer conductance (W/m2K).
θ6 = temperature of shading layer surface facing the zone air (K).
Ssh,1 = solar radiation plus short-wave radiation from lights plus IR radiation from lights and zone equipment absorbed by the gap-side face of the shading layer (W/m2K).
The heat balance equation for the shading layer surface facing the zone air is
where
Ssh,2 = solar radiation plus short-wave radiation from lights plus IR radiation from lights and zone equipment absorbed by the zone-side face of the shading layer (W/m2K).
Solving for Gap Airflow and Temperature[LINK]
For interior and exterior shading devices a pressure-balance equation is used to determine gap air velocity, gap air mean equivalent temperature and gap outlet air temperature given values of zone air temperature (or outside temperature for exterior shading), shading layer face temperatures and gap geometry. The pressure balance equates the buoyancy pressure acting on the gap air to the pressure losses associated with gap airflow between gap inlet and outlet [ISO15099, 2001]. The variables used in the following analysis of the interior shading case are shown in Figure 98.
Pressure Balance Equation[LINK]
The pressure balance equation for airflow through the gap is
Here, ΔpT is the driving pressure difference between room air and gap air. It is given by
where
ρ0 = density of air at temperature T0 (kg/m3)
T0 = reference temperature (283K)
g = acceleration due to gravity (m/s2)
H = height of shading layer (m)
φ = tilt angle of window (vertical = 90o)
Tgap~~= effective mean temperature of the gap air (K)
Tgap,in = gap inlet temperature ( = zone air temperature for interior shading) (K)
The ΔpB term is due to the acceleration of air to velocity v (Bernoulli’s law). It is given by
where ρ is the gap air density evaluated at Tgap (kg/m3).
The ΔpHP term represents the pressure drop due to friction with the shading layer and glass surfaces as the air moves through the gap. Assuming steady laminar flow, it is given by the Hagen-Poiseuille law for flow between parallel plates [Munson et al. 1998]:
where μ is the viscosity of air at temperature Tgap (Pa-s).
The ΔpZ term is the sum of the pressure drops at the inlet and outlet openings:
Here, the inlet pressure drop factor, Zin, and the outlet pressure drop factor, Zout, are given by
where
Aeq,in = equivalent inlet opening area (m2)
Aeq,out = equivalent outlet opening area (m2)
Agap = cross-sectional area of the gap = sW (m2)
If Tgap > Tgap,in
If Tgap ≤ Tgap,in
Here, the area of the openings through which airflow occurs (see Figure 98 and Figure 99) are defined as follows:
Abot = area of the bottom opening (m2)
Atop = area of the top opening (m2)
Al = area of the left-side opening (m2)
Ar= area of the right-side opening (m2)
Ah = air permeability of the shading device expressed as the total area of openings (“holes”) in the shade surface (these openings are assumed to be uniformly distributed over the shade) (m2)
Figure 99 shows examples of Abot, Atop, Al and Ar for different shading device configurations. These areas range from zero to a maximum value equal to the associated shade/screen/blind-to-glass cross-sectional area; i.e., Abot and Atop ≤ sW, Al and Ar ≤ sH.
Expression for the Gap Air Velocity
Expressing Equation in terms of v yields the following quadratic equation:
Solving this gives
The choice of the root of the quadratic equation is dictated by the requirement that v = 0 if Tgap,in = Tgap.
Gap Outlet Temperature and Equivalent Mean Air Temperature
The temperature of air in the gap as a function of distance, h, from the gap inlet (Figure 100) is
where
is the average temperature of the glass and shading layer surfaces facing the gap (K).
H0 = characteristic height (m), given by
where Cp is the heat capacity of air.
The gap outlet temperature is given by
The thermal equivalent mean temperature of the gap air is
Solution Sequence for Gap Air Velocity and Outlet Temperature
The routine WinShadeGapFlow is called within the glazing heat balance iterative loop in SolveForWindowTemperatures to determine v and Tgap,out. The solution sequence in WinShadeGapFlow is as follows:
At start of iteration, guess Tgap as ((Tgl + Tsh)/2 + Tgap,in)/2. Thereafter use value from previous iteration.
Get still-air conductance, hc, by calling WindowGasConductance and NusseltNumber.
Get v from Equation
Get hcv from Equation
Get Tave from Equation
Get Tgap,out from Equation
Get new value of Tgap from Equation
The values of hcv and Tgap so determined are then used in the window heat balance equations to find new values of the face temperatures of the glass and shading layers. These temperatures are used in turn to get new values of hcv and Tgap until the whole iterative process converges.
Convective Heat Gain to Zone from Gap Airflow
The heat added (or removed) from the air as it passes through the gap produces a convective gain (or loss) to the zone air given by
This can also be expressed as
where the air mass flow rate in the gap is given by
Heat Balance Equations for Between-Glass Shading Device[LINK]
In EnergyPlus shading devices are allowed between the two glass panes of double glazing and between the two inner glass panes of triple glazing. Figure 101 shows the case of a between-glass shading device in double glazing.
The heat balance equations for the two glass surfaces facing the shading device are the following.
For face #2:
where
effective mean air temperature in gap 1 (K)
convective heat transfer coefficient from glass or shading layer to gas in gap 1 (W/m2K)
For face #3:
where
effective mean air temperature in gap 2 (K)
convective heat transfer coefficient from glass or shading layer to gas in gap 2 (W/m2K)
The heat balance equations for the shading layer faces are:
For face #5:
For face #6:
The convective heat transfer coefficients are given by
where
surface-to-surface heat transfer coefficients for gap #1 and #2, respectively, when these gaps are non-vented (closed).
air velocity in the gaps (m/s). It is assumed that the gap widths are equal, so that the velocity of flow in the gaps is equal and opposite, i.e., when the airflow is upward in gap #1 it is downward in gap #2 and vice-versa.
In analogy to the interior or exterior shading device case, the air velocity is determined by solving the following pressure balance equation:
where the driving pressure difference between gap #1 and #2 is
The pressure drops on the right-hand side of this equation are:
where i = gap number (1 or 2).
It can be shown that
. Then, inserting these pressure drop expressions into , we obtain the following expression for the airflow velocity:
The choice of the sign of the square root term is dictated by the requirement that
if
, i.e.,
.
Given
we can now calculate
and
, which gives
. The procedure is as follows. We have
where
and
with
. Since
this gives:
Similarly,
Solving these simultaneous equations gives:
Using these in
gives
with
Similarly, from
we get
The overall solution sequence is as follows.
At start of iteration guess
and
. Then
- Get
using
.
- Get still-air conductances
by calling WindowGasConductance and NusseltNumber.
- Get
from Equation
- Get
from Equation
- Get
- Get Ho,1, Ho,2,
and
.
- Get
,
from Equations and
The values
and
are then used in the face heat balance equations to find new values of the face temperatures
and
. These are used in turn to get new values of
and
until the whole iterative process converges.
Airflow Windows[LINK]
In airflow windows forced air flows in the gap between adjacent layers of glass. Such windows are also known as “heat-extract windows” and “climate windows.”
Five configurations of airflow windows are modeled (Figure 102) that depend on the source and destination of forced air. The allowed combinations of Airflow Source and Airflow Destination are:
InsideAir OutsideAir
InsideAir InsideAir
InsideAir ReturnAir
OutsideAir InsideAir
OutsideAir OutsideAir
A common application of airflow windows is to reduce the zone cooling load by exhausting indoor air through the window, thereby picking up and rejecting heat from the glazing (Figure 102).
Figure 103 shows the variables used in the heat balance equations for forced airflow in a double-glazed window.
The heat balance equation for the left-hand glass surface facing the gap in Figure 103 is:
The corresponding equation for the right-hand glass surface facing the gap is:
Here,
Tgap~~= effective mean temperature of the gap air (K)
hcv = convective heat transfer coefficient from glass to gap air (W/m2K).
The convective heat transfer coefficient is given by
where
hc = glass-to-glass heat transfer coefficient for non-vented (closed) cavity (W/m2K)
v = mean air velocity in the gap (m/s).
The air velocity is determined by the gap cross-sectional area in the flow direction and the air flow rate, which is an input value that is constant or can vary according to a user-specified schedule:
where
F = airflow rate (m3/s)
Agap = gap cross-sectional area in direction of flow (m2)
It is assumed that the airflow is uniform across the width of the window.
The mean temperature of the gap air is given by the following expression, whose derivation follows that for for the case of an interior shading device:
where
H = glazing height (m)
Tgap,in~~= gap air inlet temperature (Ti if the airflow source is indoor air, To if the airflow source is outside air) (K)
The outlet air temperature is given by
The equations for glass face #1 and #4 are the same as those for no airflow in the gap (Equations and ).
The convective heat gain to the zone air due to the gap airflow when the airflow destination is indoor air is
where
Cp,i~~= heat capacity of the indoor air (J/kg-K)
Cp,out= heat capacity of the gap outlet air (J/kg-K)
and where the air mass flow rate in the gap is
The fan energy used to move air through the gap is very small and is ignored.
Airflow Window with Between-Glass Shading Device[LINK]
Figure 104 shows the case of a double-glazed airflow window with a between glass shading device. The heat balance equations in this case are the same as those for the between-glass shading device with natural convection (Figure 101 and following equations) except that now
where Agap = sW is the cross-sectional area of the gap on either side of the shading device. It is assumed that the shading device is centered between the two panes of glass so that the airflow, F, is divided equally between the two gaps.
The convective heat gain to the zone air due to the airflow through the two gaps when the airflow destination is indoor air is
where the average temperature of the two outlet air streams is
and
Cp,ave,out~~= heat capacity of the outlet air evaluated at Tgap,ave,out (J/kg-K)
Evacuated Glazing Unit (EGU)[LINK]
Evacuated glazing Units (EGU) are an emerging technology, developed as a concept some 20-30 years ago, but only now approaching wide-spread commercialization and adoption.
Evacuated glazing unit (EGU): cavity thermal conductance[LINK]
Thermal Conductance of the space in an evacuated glazing unit (EGU) is the sum of the conductance of the low pressure gas (air) and radiation conductance.
Conductance of the low-pressure gas
Conductance of low pressure gasses is calculated using formula by Corrucini (Corruccini, R. (1959)).
Where:
= Accommodation coefficients of the gas molecules with the two surfaces. These values depend on the temperature, surface conditions, etc. For the present configuration and conditions, it is expected that a is approximately 0.5. If conservative value is needed than value of 1.0 could be used. With = 0.5, a = 0.333
= Specific heat ratio, air = 1.40. Table 2 lists specific heat ratios for other gasses.
R= Universal gas constant, R = 8,314.462175 J/mol·K
M= Molecular Weight, Mair = 28.97 [mol/g]
T= (T1 + T2)/2 [K]
P= Pressure of the gas [N/m2]
From the paper Collins and Robinson (Collins, R., & Robinson, S. (1991)), B is set at approximately 50 for Air, if pressure is given in torr. Therefore according to Collins and Robinson, for air and approximate conditions of EGU:
CCOND ≈ 50·P
Where P is in torr (i.e., mm Hg).
Note: Conversion from Pa to torr is accomplished by multiplying value in torr by 133.28.
Using formula 2 and assuming T1 to be 20 ºC and T2 to be -18 ºC (expected temperatures of glass surfaces in EGU, if one glass surface is low-e and unit is exposed to NFRC standard environmental conditions), and using SI system of units, the B is calculated as 54.4, which is very close to the value of 50, proposed by Collins and Robinson
CCOND ≈ 54.4·P
We will use exact value, calculated by the formula, so values of will be input into the calculations, which enables more flexible model that can account for special treatment of glass surfaces.
Radiation conductance[LINK]
Radiation conductance for the two parallel plates is given by:
Where:
1= emissivity of the first facing glass surface, [ - ]
2= emissivity of the second facing glass surface, [ - ]
= Stefan-Boltzmann Constant, 5.67 x 10-8, [W/(m2·K4)]
T1= Temperature of the first facing glass surface, [K]
T2= Temperature of the second facing glass surface. [K]
Assuming glass surface temperatures of 20 ºC and -18 ºC, respectively, the following radiation conductances are obtained for the three different glass emissivities:
Clear Glass (1 = 2 = 0.84): CRAD = 3.4 W/m2K
Hard Coat Low-e (1 or 2 = 0.15): CRAD = 0.68 W/m2K
Soft Coat Low-e (1 or 2 = 0.04): CRAD = 0.19 W/m2K
Note: CRAD of 0.09 is theoretically possible using best low-e technology today (i.e., 1 or 2 = 0.02).
Note: Low-e values above are typical values, which will vary by manufacturer. Some more recent hard coat low-e values are at or below 0.1.
It should also be noted that values above are based on the fix set of temperatures, while in reality temperatures will depend on the environmental conditions and surface emissivities (e.g., it cannot be expected that clear glass will have same T1 and T2 as low-e glass).
Equation is precise formulation for two parallel plates at the constant temperature. Simplified equation under these conditions is given in the form of:
Where:
Tm =mean temperature, [K]
Calculation of the U-factor
Where:
tglass = glass thickness; [m]
kglass = glass conductivity; kglass = 1 W/(m·K)
Rglass = 0.003 m2K/W (for 3 mm glass pane)
Ro ≈ 0.033 m2K/W
Ri ≈ 0.14 m2K/W
U-factor of EGU without any pillars (pretending that this is possible) would be calculated using CRAD only. From above radiation conductance calculations:
Clear Glass: U = 2.64 W/(m2·K) [0.464 Btu/(hr·ft2·ºF)]
Hard Coat Low-e: U = 0.62 W/(m2·K) [0.109 Btu/(hr·ft2·ºF)]
Soft Coat Low-e:U = 0.19 W/(m2·K) [0.034 Btu/(hr·ft2·ºF)]
Adding conductance of the air at 0.001 torr (CCOND = 0.08 W/(m2·K), these values become:
Clear Glass: U = 2.66 W/(m2·K) [0.468 Btu/(hr·ft2·ºF)]
Hard Coat Low-e: U = 0.68 W/(m2·K) [0.120 Btu/(hr·ft2·ºF)]
Soft Coat Low-e:U = 0.27 W/(m2·K) [0.048 Btu/(hr·ft2·ºF)]
In contrast, the U-factor of the same configuration with the air at atmospheric pressure will be (For the space width of 50 m, CCOND ≈ 450 W/m2K):
Clear Glass: U = 5.52 W/(m2·K) [0.468 Btu/(hr·ft2·ºF)]
Hard Coat Low-e: U = 5.52 W/(m2·K) [0.120 Btu/(hr·ft2·ºF)]
Soft Coat Low-e:U = 5.52 W/(m2·K) [0.048 Btu/(hr·ft2·ºF)]
It is clear that emissivity of the glass surface makes no difference, because of the dominant conductance of the air space. Also, it is worth noting that the U-factor of such configuration is very close to the U-factor of single glazing.
Evacuated glazing unit (EGU): Glass support element thermal conductance[LINK]
Glass panes in the EGU are separated by an array of small support elements. Typically, these support elements have a cylindrical shape and are often referred to as “pillars.” Typical geometry of the pillar is 0.5-1.0 mm diameter and 0.05 mm (50 m) height. They are typically spaced 1-2 in. apart in a form of square or staggered matrix.
Calculation of the U-factor[LINK]
The conductance of these elements can be measured or numerically modeled to determine accurate thermal performance. Approximate method also exists and is based on the combination of modeling and analytical work for the conduction through small cylinders in contact with infinite parallel plates with thickness much larger than cylinder height.
The following formula can be used to determine conductance of the single pillar, Cp (Collins and Fisher-Cripps 1991):
Where:
k= conductivity of glass, W/(m·K)
a= radius of the pillar (m)
h= pillar height, m
For the square array of support pillars (Collins and Fischer-Cripps 1991) proposes the following formula for their conductance, Cpa:
Where:
= pillar spacing, m
This formula is approximate and does not include effect of the conductivity of the pillar, but it gives good approximation for common materials used in this technology, since conductivity of the pillar does not play substantial role for non-insulating pillars (where “non-insulating” would mean that conductivity of the pillar is equal or higher than the conductivity of the glass pane.
The U-factor of the EGU with support pillars is then:
Where:
Collins, R., & Fischer-Cripps, A. 1991. “Design of Support Pillar Arrays in Flat Evacuated Windows.”. Aust. J. Phys.
Collins, R., & Robinson, S. 1991. “Evacuated Glazing”. Solar Energy. Vol. 47, No. 1, pp. 27-38.
Corruccini, R. 1959. “Gaseous Heat Conduction at Low Pressures and Temperatures”. Vacuum. Vol. 7-8, pp.19-29.
Deflection of insulated glazing unit (IGU) can result in thermal performance degradation or improvement due to the reduction or increase of gap space width. Convection of the gas fill is affected by changed gap space and due to modified convection pattern and shorter or longer thermal path at the center of the glazing unit can result in increased or decreased thermal performance. For the most part, U-factor is mostly affected as a direct result of changed thermal performance; however note that solar heat gain through the window (SHGC) can also be affected because of the effect of inward flowing fraction of absorbed solar radiation, which is affected by thermal performance of the IGU.
Deflection in sealed IGU is caused by the difference in gas pressure in IGU gap vs. outdoor/indoor pressure. Indoor and outdoor pressure can be considered equal, since indoor building environment is in pretty good contact with outdoor environment. We will call this pressure an atmospheric pressure, Pa. The differences in pressure between atmospheric and gap pressure is due to several factors, listed here:
- Difference in atmospheric pressure between IGU fabrication location and end use location
- Difference in temperature during fabrication and actual operating conditions for the glazing. It should be noted that initial temperature can be higher than ambient temperature during fabrication process, due to elevated sealant temperatures, which can raise local temperatures within the IGU.
- Unbalanced gas fill leakage through the sealants, resulting in lower gap pressure and inward deflection.
- Wind or static load pressure
Effects 1 and 2 will be modeled using equations presented below, while effect 3 does not have credible mathematical model. However, cumulative deflection, resulting from all three effects can be measured in the field and its effect on thermal performance can be modeled by specifying center glazing deflection.
Wind or static load pressure effects on deflection is not included in this model at this time, but will be considered for future versions.
Recognizing that indoor and outdoor air pressure could be different, such as in hot box test environment, future plans for the extension of the model will include option to specify different values for indoor and outdoor pressure. Another future improvement to the model will also include linking certain air gaps with indoor or outdoor environment, meaning that respective pressures in linked spaces will be set to equal.
Mathematical Model[LINK]
Mathematical model described in detail here is based on the research work by Bernier and Bourret (1997) and Timoshenko and Woinowsky-Krieger (1959). Bernier and Bourret (1997) of the Ecole Polytechnique Montréal adopted Timoshenko and Woinowsky-Krieger (1959) model for calculating flat plate deflection subjected to the differential pressure field (static), while their original contribution was to develop correlations for changes in thermal performance, based on IGU deflection at the center of glazing location. In addition to adopting Bernier and Bourret (1997) model here, we have also developed model for calculating change in thermal performance of deflected units when this deflection is measured in the field. Therefore, the mathematical formulation, presented here is divided into two sections; 1) calculation of the deflection and resulting thermal performance caused by pressure and temperature effects and 2) calculation of the thermal performance of the IGU when the deflection is measured.
If coordinate system is set as shown in Figure 105 and Figure 106, it is possible to calculate deflection distribution at each point of pane by using following equation:
Where,
Where,
E = Young’s modulus (7.2 x 1010) [Force per unit Area; SI: Pa, IP: psi]
t = thickness of glazing pane [Length; SI: m, IP: in.]
= poison’s ratio (0.22 for glass) [Non-Dimensional]
ΔPi = Pgap(i) - Pgap(i-1) (for i-th pane) [Force per unit Area; SI: Pa, IP: psi]
ΔPi = Pgap(1) - Pa (first pane) [Force per unit Area; SI: Pa, IP: psi]
ΔPi = Pa - Pgap(n-1)(last pane) [Force per unit Area; SI: Pa, IP: psi]
Where,
Pa = atmospheric pressure. [Force per unit Area; SI: Pa, IP: psi]
Where,
Pini = Initial pressure. Applies to all gaps as a single value (input data - measured or otherwise) [Force per unit Area; SI: Pa, IP: psi]
Tini = Initial temperature. Applies to all gaps as a single value (input data - measured or otherwise) [Degree Temperature; SI: K, IP: R]
Vini(i) = Initial volume for i-th gap. [Length*Length*Length; SI: m3, IP: in3]
Where,
Li = non-deflected glazing gap width (for i-th gap) [Length; SI: m, IP: in.]
W = IGU width [Length; SI: m, IP: in.]
H = IGU height [Length; SI: m, IP: in.]
Tgap(i) = temperature of the gap between two glass panes (calculated using center of glazing thermal calculation algorithm, as described in ISO 15099 (ISO 2003). This value is first calculated using non-deflected state and is recalculated after the resulting deflection is calculated. This process is repeated until temperature at next iteration does not differ by more than 0.1 ºC
Vgap(i) = volume of the IGU gap in deflected state [Lentgh*Length*Length; SI: m3, IP: in3]
Where,
is mean deflection value for i-th pane. [Length; SI: m, IP: in.]
Deflection of each pane can be positive or negative and is done solely to establish reference. Current frame of reference is that positive deflection means that pane is deflecting towards left side, while negative deflection means that pane is deflecting towards right side . Whether the deflection is in the direction of reducing the gap width or increasing it, it will be the result of pressure difference, as described in . When pressure in the glazing unit is higher than surrounding environmental pressure, the deflection will be towards increasing gap width (i.e., ballooning), while the opposite situation will result in decreasing gap width (i.e., vacuuming)
The important part of calculating deflection of the IGU is to determine mean deflection value for each glazing pane. Mean deflection value is used to calculate gap volume in deflected state . Mean deflection of glazing pane can be calculated by integrating :
Which is identical with the following expression:
and because integral of sin(x) is equal with –cos(x), above equation will become:
Finally, because
and
values are always equal to -1 for the given range of m and n, above equation will became:
After calculating mean pane deflection the following equation is used to calculate mean gap width:
Where,
Lr(i) = Mean gap “i” width after incorporating glazing deflection. This mean gap width is used to recalculate thermal performance of deflected IGU.
*****= mean glazing deflection for each pane “i”.*
Calculation of the deflection at the center of glazing and mean glazing deflection for each pane is an iterative process, where the initial temperature distribution is calculated for non-deflected state, then deflection is calculated based on this temperature distribution, new temperature distribution is calculated for this deflected state, then temperatures from previous iteration are compared to the current iteration and the process is repeated until the difference is no larger than 0.1 ºC.
At the end of calculations, program will calculate and return maximum deflection value for each pane (i.e., center of glazing deflection). If we label maximum deflection of each pane as LD(i),max, we can calculate this value by substituting x=W/2 and y=H/2 in equation to determine deflection at the center point. Therefore,
For glazing systems with more than two glazing layers, meaning multiple gas filled gaps, the deflection will be calculated for each glazing pane assuming that the pressure in a gap is independent from each other and calculated separately, unless spaces are “linked” together (e.g., stretched film middle glazing that has hole for equalizing pressure).
Non-Linked Gaps in 3 or more glazing layer system:[LINK]
The procedure shown above generally applies to the 3 or more layer glazing system, with the exception that neighboring pressures are no longer Pa, but rather could be Pa on one side and Pgap on the other, or have Pgap on both sides, as shown in Figure 107 for gap “i”. Center of glazing thermal calculation will determine new temperature distribution, after deflection is calculated for each glazing and will be used to determine new Pgap, as per the procedure above.
Linked Gaps in 3 or more glazing layer system:[LINK]
When one or more gaps are linked together, their pressure is assumed to be identical (e.g., in triple glazing IGU Pgap,1 = Pgap,2.) This pressure is calculated from temperatures of bounding glazing for linked gaps (e.g., for triple glazing IGU, glazing 1 and 3) and using neighboring pressures outside of those bounding glazing (e.g., for triple glazed IGU, Pa on both sides).
Note: This feature is not implemented in WINDOW 7.1. It is considered for future enhancements to the program.
Gap(s) Linked to Indoor or Outdoor Environment:[LINK]
If one or more glazing gaps are linked to either indoor or outdoor environment its pressure is fixed to Pa. In combination situations, such as two or more gaps linked together with one of them being linked to indoor or outdoor environment, they will all have fixed pressure of Pa.
When deflection is measured, it is normally measured at the point of maximum deflection. Maximum deflection occurs at center of the IGU (at W/2 and H/2).
Measured value is typically gap width at the point of maximum deflection, which we can label LG(i). For i-th measured gap the width is equal to:
If we label ratio of mean deflection and maximum deflection as R(i), then:
Important thing to note is that ratios (
) for all gaps in glazing system are equal.
Replacing and into the following equation is obtained:
Combining with we get the following expression for the mean gap width:
Number of equations given in expression is equal to n-1, where n is number of panes. Therefore, we need one more equation to complete the system of equations that would allow us to solve for all independent variables. To get the last equation we can rewrite in slightly different manner:
Where coefficient K combines all constant terms, while
is given by and
is calculated by, and . Summing over all deflections,
the following equation is obtained:
Note that sum of all
is equal to zero since outside pressure is equal to inside. Therefore, the remaining equation that completes the set of equations is:
Solving system of equations[LINK]
In order to solve system of equations we will present in slightly different manner:
Which in developed form will look like this:
In order to express each
as dependence from
(deflection of inside/last pane) we will need to make sum from first to last, then from second to last, third to last and so on. This procedure will create following set of equations:
Now replacing this set of equations back to :
Which solving by
leads to the following equation:
Calculating
value from this equation and substituting it in will enable calculation of the deflection of remaining panes.
Arasteh, D.K., J.C. Kohler and B.T. Griffith. Draft 2009. Modeling Windows in EnergyPlus with only U, SHGC, and optionally VT. LBNL report. Full reference to be determined.
Arasteh, D. J. 2009. Modeling Windows in EnergyPlus with only U, SHGC, and optionally VT. Lawrence Berkeley National Laboratory.
Arasteh, D.K., M.S. Reilly and M.D. Rubin. 1989. A versatile procedure for calculating heat transfer through windows. American Society of Heating, Refrigeration and Air-Conditioning Engineers, ASHRAE Transactions, Vol. 95, Pt. 2.
Bernier, M., & Bourret, B. January 1997. “Effects of Glass Plate Curvature on the U-Factor of Sealed Insulated Glazing Units”. Atlanta, GA: ASHRAE Transactions. Vol. 103, Pt. 1. American Society for Heating, Refrigerating and Air-Conditioning Engineers.
Collins, R., & Fischer-Cripps, A. 1991. “Design of Support Pillar Arrays in Flat Evacuated Windows.”. Aust. J. Phys.
Collins, R., & Robinson, S. 1991. “Evacuated Glazing”. Solar Energy. Vol. 47, No. 1, pp. 27-38.
Corruccini, R. (1959). “Gaseous Heat Conduction at Low Pressures and Temperatures”. Vacuum. Vol. 7-8, pp.19-29.
Finlayson, E.U., D.K. Arasteh, C. Huizenga, M.D. Rubin and M.S. Reilly. 1993. WINDOW 4.0: documentation of calculation procedures. Lawrence Berkeley National Laboratory report no. LBL-33943.
ISO. 2003. ISO 15099:2003. Thermal performance of windows, doors, and shading devices – Detailed calculations. International Organization for Standardization.
Klems, J. H. 1994A. “A New Method for Predicting the Solar Heat Gain of Complex Fenestration Systems: I. Overview and Derivation of the Matrix Layer Calculation.”. ASHRAE Transactions. 100 (pt.1): 1073-1086.
Klems, J. H. 1994B. “A New Method for Predicting the Solar Heat Gain of Complex Fenestration Systems: II. Detailed Description of the Matrix Layer Calculation.”. ASHRAE Transactions. 100 (pt.1): 1073-1086.
Klems, J. H. 1995. “Measurements of Bidirectional Optical Properties of Complex Shading Devices.”. ASHRAE Transactions. 101 (pt 1; Symposium Paper CH-95-8-1 (RP-548)): 791-801.
Klems, J. H. 1996. “A Comparison between Calculated and Measured SHGC for Complex Glazing Systems.”. ASHRAE Transactions. 102 (Pt. 1; Symposium Paper AT-96-16-1): 931-939.
Klems, J. H. 1996. “Calorimetric Measurements of Inward-Flowing Fraction for Complex Glazing and Shading Systems.”. ASHRAE Trans. 102(Pt. 1; Symposium Paper AT-96-16-3): 947-954.
Munson, B.R, D.F. Young and T.H. Okiishi. 1998. “Fundamentals of Fluid Mechanics,” Third Edition Update, John Wiley & Sons, Inc.
Papamichael, K. J. 1998. “Determination and Application of Bidirectional Solar-Optical Properties of Fenestration Systems.”. Cambridge, MA: 13th National Passive Solar Conference.
Simmler, H., U. Fischer and F. Winkelmann. 1996. Solar-Thermal Window Blind Model for DOE-2. Lawrence Berkeley National Laboratory, Simulation Research Group internal report, (unpublished).
Timoshenko, S., & Kreiger-Woinowsky, S. 1959. “Theory of Plates and Shells” 2nd Edition. McGraw-Hill Company.
Window Heat Balance Calculation[LINK]
Table: Fortran Variables used in Window Heat Balance Calculations
Mathematical variable|Description|Units||FORTRAN variable ———————|———–|—–||—————- N|Number of glass layers|-|nlayer σ|Stefan-Boltzmann constant||sigma εi|Emissivity of face i|-|emis ki|Conductance of glass layer i|W/m2-K|scon ho, hi|Outside, inside air film convective conductance|W/m2-K|hcout, hcout hj|Conductance of gap j|W/m2-K|hgap To, Ti|Outdoor and indoor air temperatures|K|tout, tin Eo, Ei|Exterior, interior long-wave radiation incident on window|W/m2|outir, rmir θi|Temperature of face i|K|thetas Si|Radiation (short-wave, and long-wave from zone internal sources) absorbed by face i|W/m2|AbsRadGlassFace Iextbm|Exterior beam normal solar irradiance|W/m2|BeamSolarRad Iextdif|Exterior diffuse solar irradiance on glazing|W/m2|- Iintsw|Interior short-wave radiation (from lights and from reflected diffuse solar) incident on glazing from inside|W/m2|QS Iintlw|Long-wave radiation from lights and equipment incident on glazing from inside|W/m2|QL φ|Angle of incidence|radians|- Afj|Front beam solar absorptance of glass layer j|-|- Ajf,dif, Ajb,dif|Front and back diffuse solar absorptance of glass layer j|-|AbsDiff, AbsDiffBack A, B|Matrices used to solve glazing heat balance equations|W/m2, W/m2-K|Aface, Bface hr,i|Radiative conductance for face i|W/m2-K|hr(i) Δθi|Difference in temperature of face i between successive iterations|K|-
The Glazing Heat Balance Equations[LINK]
The window glass face temperatures are determined by solving the heat balance equations on each face every time step. For a window with N glass layers there are 2N faces and therefore 2N equations to solve. Figure 91 shows the variables used for double glazing (N=2).
The following assumptions are made in deriving the heat balance equations:
The four equations for double-glazing are as follows. The equations for single glazing (N=1) and for N=3 and N=4 are analogous and are not shown.
Absorbed Radiation[LINK]
Si in Equations to is the radiation (short-wave and long-wave from zone lights and equipment) absorbed on the ith face. Short-wave radiation (solar and short-wave from lights) is assumed to be absorbed uniformly along a glass layer, so for the purposes of the heat balance calculation it is split equally between the two faces of a layer. Glass layers are assumed to be opaque to IR so that the thermal radiation from lights and equipment is assigned only to the inside (room-side) face of the inside glass layer. For N glass layers Si~~is given by
Here
Room-Side Convection[LINK]
The correlation for room-side convection coefficient,
, is from ISO 15099 section 8.3.2.2. (Prior to EnergyPlus version 3.1, the value for
was modeled using the “Detailed” algorithm for opaque surface heat transfer, e.g. for a vertical surface
; see section Detailed Natural Convection Algorithm). The ISO 15099 correlation is for still room air and is determined in terms of the Nusselt number,
, where
where,
The Rayleigh number based on height,
, is calculated using,
where,
There are four cases for the Nusselt correlation that vary by the tilt angle in degrees,
, and are based on heating conditions. For cooling conditions (where
) the tilt angle is complemented so that 
Case A.
Case B.
Case C.
Case D.
The material properties are evaluated at the mean film temperature. Standard EnergyPlus pyschrometric functions are used for
and
. Thermal conductivity is calculated using,
Kinematic viscosity is calculated using,
This correlation depends on the surface temperature of the room-side glazing surface and is therefore included inside the window heat balance interation loop.
Solving the Glazing Heat Balance Equations[LINK]
The equations are solved as follows:
Repeat steps 4 to 9 until the difference,
, between values of the
in successive iterations is less than some tolerance value. Currently, the test is
If this test does not pass after 100 iterations, the tolerance is increased to 0.2K. If the test still fails the program stops and an error message is issued.
The value of the inside face temperature,
, determined in this way participates in the zone heat balance solution (see Outdoor/Exterior Convection) and thermal comfort calculation (see Occupant Thermal Comfort).
Edge-Of-Glass Effects[LINK]
Table: Fortran Variables used in Edge of Glass calculations
Mathematical variable|Description|Units||FORTRAN variable ———————|———–|—–||—————-
|Area-weighted net conductance of glazing including edge-of-glass effects|W/m2-K|- Acg|Area of center-of-glass region|m2|CenterGlArea Afe|Area of frame edge region|m2|FrameEdgeArea Ade|Area of divider edge region|m2|DividerEdgeArea Atot|Total glazing area|m2|Surface%Area hcg|Conductance of center-of-glass region (without air films)|W/m2-K|- hfe|Conductance of frame edge region (without air films)|W/m2-K|- hde|Conductance of divider edge region (without air films)|W/m2-K|- hck|Convective conductance of gap k|W/m2-K|- hrk|Radiative conductance of gap k|W/m2-K|- η|Area ratio|-|- α|Conductance ratio|-|FrEdgeToCenterGlCondRatio, DivEdgeToCenterGlCondRatio
Because of thermal bridging across the spacer separating the glass layers in multi-pane glazing, the conductance of the glazing near the frame and divider, where the spacers are located, is higher than it is in the center of the glass. The area-weighted net conductance (without inside and outside air films) of the glazing in this case can be written
where
hcg = conductance of center-of-glass region (without air films)
hfe~~= conductance of frame edge region (without air films)
hde = conductance of divider edge region (without air films)
Acg = area of center-of-glass region
Afe = area of frame edge region
Ade = area of divider edge region
Atot = total glazing area =
The different regions are shown in Figure 92:
Figure 92: Different types of glass regions.
Equation can be rewritten as
where
The conductance ratios
and
are user inputs obtained from Window 5. They depend on the glazing construction as well as the spacer type, gap width, and frame and divider type.
In the EnergyPlus glazing heat balance calculation effective gap convective conductances are used to account for the edge-of-glass effects. These effective conductances are determined as follows for the case with two gaps (triple glazing). The approach for other numbers of gaps is analogous.
Neglecting the very small resistance of the glass layers, the center-of-glass conductance (without inside and outside air films) can be written as
where
Equation then becomes
We can also write
in terms of effective convective conductances of the gaps as
Comparing Eqs. and we obtain
Using
gives
This is the expression used by EnergyPlus for the gap convective conductance when a frame or divider is present.
Apportioning of Absorbed Short-Wave Radiation in Shading Device Layers[LINK]
If a shading device has a non-zero short-wave transmittance then absorption takes place throughout the shading device layer. The following algorithm is used to apportion the absorbed short-wave radiation to the two faces of the layer. Here f1 is the fraction assigned to the face closest to the incident radiation and f2 is the fraction assigned to the face furthest from the incident radiation.
Otherwise
Window Frame and Divider Calculation[LINK]
For the zone heat balance calculation the inside surface temperature of the frame and that of the divider are needed. These temperatures are determined by solving the heat balance equations on the inside and outside surfaces of the frame and divider.
Table: Fortran Variables used in Window/Frame and Divider calculations
Mathematical variable|Description|Units||FORTRAN variable ———————|———–|—–||—————- QExtIR,abs|IR from the exterior surround absorbed by outside frame surfaces|W|- QIR,emitted|IR emitted by outside frame surfaces|W|- Qconv|Convection from outside air to outside frame surfaces|W|- Qcond|Conduction through frame from inside frame surfaces to outside frame surfaces|W|- Qabs|Solar radiation plus outside glass IR absorbed by outside of frame|W|- Qdifabs,sol|Diffuse solar absorbed by outside frame surfaces, per unit frame face area|W/ m2|- Qbmabs,sol|Beam solar absorbed by outside frame surfaces, per unit frame face area|W/ m2|- Idifext|Diffuse solar incident on window|W/ m2|- Ibmext|Direct normal solar irradiance|W/ m2|- αfrsol|Solar absorptance of frame|-|FrameSolAbsorp Rglf,dif|Front diffuse solar reflectance of glazing|-| Rglf,bm|Front beam solar reflectance of glazing|-| cos(βface)|Cosine of angle of incidence of beam solar on frame outside face ||CosIncAng Cos(βh)|Cosine of angle of incidence of beam solar on frame projection parallel to window x-axis|-|CosIncAngHorProj Cos(βv)|Cosine of angle of incidence of beam solar on frame projection parallel to window y-axis|-|CosIncAngVertProj fsunlit|Fraction of window that is sunlit|-|SunlitFrac Af|Area of frame’s outside face (same as area of frame’s inside face)|m2|- Ap1, Ap2|Area of frame’s outside and inside projection faces|m2|- Ff|Form factor of frame’s outside or inside face for IR|-|- Fp1, Fp2|Form factor of frame outside projection for exterior IR; form factor of frame inside projection for interior IR |-|- Eo|Exterior IR incident on window plane|W/m2|outir Ei|Interior IR incident on window plane|W/m2|SurroundIRfromParentZone ε1, ε2|Outside, inside frame surface emissivity|-|FrameEmis θ1, θ2|Frame outside, inside surface temperature|K|FrameTempSurfOut, FrameTempSurfIn To, Ti|Outdoor and indoor air temperatures|K|tout, tin ho,c, hi,c|Frame outside and inside air film convective conductance|W/m2-K|HOutConv, HInConv k|Effective inside-surface to outside-surface conductance of frame per unit area of frame projected onto window plane|W/m2-K|FrameConductance, FrameCon S1|Qabs/Af|W/m2-K|FrameQRadOutAbs S2|Interior short-wave radiation plus interior IR from internal sources absorbed by inside of frame divided by Af|W/m2-K|FrameQRadInAbs η1, η2|Ap1/Af, Ap2/Af|-|- H|Height of glazed portion of window|m|Surface%Height W|Width of glazed portion of window|m|Surface%Width wf, wd|Frame width, divider width|m|FrameWidth, DividerWidth pf1, pf2|Frame outside, inside projection|m|FrameProjectionOut, FrameProjectionIn Nh, Nv|Number of horizontal, vertical dividers|-|HorDividers, VertDividers To,r, Ti,r|Frame outside, inside radiative temperature|K|TOutRadFr, TInRadFr ho,r, hi,r|Frame outside, inside surface radiative conductance|W/m2-K|HOutRad, HInRad A|Intermediate variable in frame heat balance solution|K|Afac C|Intermediate variable in frame heat balance solution|-|Efac B, D|Intermediate variables in frame heat balance solution|-|Bfac, Dfac
Frame Temperature Calculation[LINK]
Figure 93 shows a cross section through a window showing frame and divider. The outside and inside frame and divider surfaces are assumed to be isothermal. The frame and divider profiles are approximated as rectangular since this simplifies calculating heat gains and losses (see “Error Due to Assuming a Rectangular Profile,” below).
Frame Outside Surface Heat Balance[LINK]
The outside surface heat balance equation is
where
The first term can be written as the sum of the exterior IR absorbed by the outside face of the frame and the exterior IR absorbed by the frame’s outside projection surfaces.
where ε1 is the outside surface emissivity.
The exterior IR incident on the plane of the window, Eo, is the sum of the IR from the sky, ground and obstructions. For the purposes of the frame heat balance calculation it is assumed to be isotropic. For isotropic incident IR, Ff = 1.0 and Fp1 = 0.5, which gives
The IR emitted by the outside frame surfaces is
The convective heat flow from the outside air to the outside frame surfaces is
The conduction through the frame from inside to outside is
Note that Af is used here since the conductance, k, is, by definition, per unit area of frame projected onto the plane of the window.
Adding these expressions for the Q terms and dividing by Af gives
where S1 = Qabs/Af and
We linearize Eq. as follows.
Write the first two terms as
and define a radiative temperature
This gives
which, within a few percent, equals
Defining an outside surface radiative conductance as follows
then gives
The final outside surface heat balance equation in linearized form is then
Frame Inside Surface Heat Balance[LINK]
A similar approach can be used to obtain the following linearized inside surface heat balance equation:
where
and Ei is the interior IR irradiance incident on the plane of the window.
Solving Eqs. and simultaneously gives
with
Calculation of Solar Radiation Absorbed by Frame[LINK]
The frame outside face and outside projections and inside projections absorb beam solar radiation (if sunlight is striking the window) and diffuse solar radiation from the sky and ground. For the outside surfaces of the frame, the absorbed diffuse solar per unit frame face area is
If there is no exterior window shade, Idifext includes the effect of diffuse solar reflecting off of the glazing onto the outside frame projection, i.e.,
The beam solar absorbed by the outside face of the frame, per unit frame face area is
The beam solar absorbed by the frame outside projection parallel to the window x-axis is
Here it is assumed that the sunlit fraction, fsunlit, for the window can be applied to the window frame. Note that at any given time beam solar can strike only one of the two projection surfaces that are parallel to the window x-axis. If there is no exterior window shade, Ibmext includes the effect of beam solar reflecting off of the glazing onto the outside frame projection, i.e.,
The beam solar absorbed by the frame outside projection parallel to the window y-axis is
Using a similar approach, the beam and diffuse solar absorbed by the inside frame projections is calculated, taking the transmittance of the glazing into account.
Error Due to Assuming a Rectangular Profile[LINK]
Assuming that the inside and outside frame profile is rectangular introduces an error in the surface heat transfer calculation if the profile is non-rectangular. The percent error in the calculation of convection and emitted IR is approximately 100
, where Lprofile,rect is the profile length for a rectangular profile (wf + pf1 for outside of frame or wf + pf2 for inside of frame) and Lprofile,actual is the actual profile length. For example, for a circular profile vs a square profile the error is about 22%. The error in the calculation of absorbed beam radiation is close to zero since the beam radiation intercepted by the profile is insensitive to the shape of the profile. The error in the absorbed diffuse radiation and absorbed IR depends on details of the shape of the profile. For example, for a circular profile vs. a square profile the error is about 15%.
Divider Temperature Calculation[LINK]
The divider inside and outside surface temperatures are determined by a heat balance calculation that is analogous to the frame heat balance calculation described above.
Beam Solar Reflection from Window Reveal Surfaces[LINK]
This section describes how beam solar radiation that is reflected from window reveal surfaces is calculated. Reflection from outside reveal surfaces—which are associated with the setback of the glazing from the outside surface of the window’s parent wall—increases the solar gain through the glazing. Reflection from inside reveal surfaces—which are associated with the setback of the glazing from the inside surface of the window’s parent wall—decreases the solar gain to the zone because some of this radiation is reflected back out of the window.
The amount of beam solar reflected from reveal surfaces depends, among other things, on the extent to which reveal surfaces are shadowed by other reveal surfaces. An example of this shadowing is shown in Figure 94. In this case the sun is positioned such that the top reveal surfaces shadow the left and bottom reveal surfaces. And the right reveal surfaces shadow the bottom reveal surfaces. The result is that the left/outside, bottom/outside, left/inside and bottom/inside reveal surfaces each have sunlit areas. Note that the top and right reveal surfaces are facing away from the sun in this example so their sunlit areas are zero.
The size of the shadowed areas, and the size of the corresponding illuminated areas, depends on the following factors:
We will assume that the reveal surfaces are perpendicular to the window plane and that the window is rectangular. Then the above factors determine a unique shadow pattern. From the geometry of the pattern the shadowed areas and corresponding illuminated areas can be determined. This calculation is done in subroutine CalcBeamSolarReflectedFromWinRevealSurface in the SolarShading module. The window reveal input data is specified in the WindowProperty:FrameAndDivider object expect for the depth of the outside reveal, which is determined from the vertex locations of the window and its parent wall.
If an exterior shading device (shade, screen or blind) is in place it is assumed that it blocks beam solar before it reaches outside or inside reveal surfaces. Correspondingly, it is assumed that an interior or between-glass shading device blocks beam solar before it reaches inside reveal surfaces.
Representative shadow patterns are shown in Figure 95 for a window with no shading device, and without and with a frame. The case with a frame has to be considered separately because the frame can cast an additional shadow on the inside reveal surfaces.
The patterns shown apply to both vertical and horizontal reveal surfaces. It is important to keep in mind that, for a window of arbitrary tilt, if the left reveal surfaces are illuminated the right surfaces will not be, and vice versa. And if the bottom reveal surfaces are illuminated the top surfaces will not be, and vice versa. (Of course, for a vertical window, the top reveal surfaces will never be illuminated by beam solar if the reveal surfaces are perpendicular to the glazing, as is being assumed.
For each shadow pattern in Figure 95, equations are given for the shadowed areas
and
of the outside and inside reveal surfaces, respectively. The variables in these equations are the following (see also Figure 96):
For simplicity it is assumed that, for the case without a frame, the shadowed and illuminated areas extend into the glazing region. For this reason,
and
are measured from the midplane of the glazing. For the case with a frame, the beam solar absorbed by the surfaces formed by the frame outside and inside projections perpendicular to the glazing is calculated as described in “Window Frame and Divider Calculation: Calculation of Solar Radiation Absorbed by Frame.”
The following logic gives expressions for the shadowed areas for all possible shadow patterns. Here:
d1 =
d2 =
P1 =
P2 =
f1 =
f2 =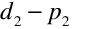
d2prime =
d2prime2 =
d12 =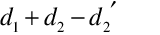
TanAlpha =
A1sh =
A2sh =
L =
L1 = average distance to frame of illuminated area of outside reveal (used to calculate view factor to frame).
L2 = average distance to frame of illuminated area of inside reveal (used to calculate view factor to frame).
The beam solar reflected from a sunlit region of area
is given by
where
All reflected radiation is assumed to be isotropic diffuse. For outside reveal surfaces it is assumed that
goes toward the window and
goes to the exterior environment. Of the portion that goes toward the window a fraction
goes toward the frame, if present, and
goes toward the glazing.
The view factor
to the frame calculated by assuming that the illuminated area can be considered to be a line source. Then the area-weighted average distance,
, of the source to the frame is calculated from the shape of the illuminated area (see above psuedo-code). Then
is related as follows to the average angle subtended by the frame of width
:
For the portion going towards the frame,
is absorbed by the frame (where
is the solar absorptance of the frame) and contributes to the frame heat conduction calculation. The rest,
, is assumed to be reflected to the exterior environment.
If the glazing has diffuse transmittance
, diffuse front reflectance
, and layer front absorptance
, then, of the portion,
, that goes toward the glazing,
is transmitted to the zone,
is absorbed in glass layer
and contributes to the glazing heat balance calculation, and
is reflected to the exterior environment.
The beam solar absorbed by an outside reveal surface is added to the other solar radiation absorbed by the outside of the window’s parent wall.
For inside reveal surfaces it is assumed that
goes towards the window and
goes into the zone. Of the portion that goes toward the window a fraction
goes toward the frame, if present, and
goes toward the glazing (
is calculated using a method analogous to that used for
). For the portion going towards the frame,
is absorbed by the frame and contributes to the frame heat conduction calculation. The rest,
, is assumed to be reflected back into the zone.
If the glazing has diffuse back reflectance
, and layer back absorptance
, then, of the portion
that goes toward the glazing,
is transmitted back out the glazing,
is absorbed in glass layer
and contributes to the glazing heat balance calculation, and
is reflected into the zone.
The beam solar absorbed by an inside reveal surface is added to the other solar radiation absorbed by the inside of the window’s parent wall.
Shading Device Thermal Model[LINK]
Shading devices in EnergyPlus can be on the exterior or interior sides of the window or between glass layers. The window shading device thermal model accounts for the thermal interactions between the shading layer (shade, screen or blind) and the adjacent glass, and between the shading layer and the room (for interior shading) or the shading layer and the outside surround (for exterior shading).
An important feature of the shading device thermal model is calculating the natural convection airflow between the shading device and glass. This flow affects the temperature of the shading device and glazing and, for interior shading, is a determinant of the convective heat gain from the shading layer and glazing to the zone air. The airflow model is based on one described in the ISO Standard 15099, “Thermal Performance of Windows, Doors and Shading Devices—Detailed Calculations” [ISO15099, 2001]. (Between-glass forced airflow is also modeled; see “Airflow Windows.”)
The following effects are considered by the shading device thermal model:
In the following it is assumed that the shading device, when in place, covers the glazed part of the window (and dividers, if present) and is parallel to the glazing. For interior and exterior shading devices it is assumed that the shading layer is separated from the glazing by an air gap. A between-glass shading layer is assumed to be centered between two glass layers and separated from the adjacent glass layers by gaps that is filled with the same gas. If the window has a frame, it is assumed that the shading device does not cover the frame.
Heat Balance Equations for Shading Device and Adjacent Glass[LINK]
If a window shading device is deployed the heat balance equations for the glass surfaces facing the shading layer are modified, and two new equations, one for each face of the shading layer, are added. Figure 97 illustrates the case of double glazing with an interior shading device.
The heat balance equation for the glass surface facing the gap between glass and shading layer (called in the following, “gap”) is
where
τsh = IR diffuse transmittance of shading device
εsh = diffuse emissivity of shading device
ρsh = IR diffuse reflectance of shading device ( = 1 - ( τsh + εsh))
θ5 = temperature of the surface of the shading layer that faces the gap (K).
The term 1 – ρ4 ρsh accounts for the inter-reflection of IR radiation between glass and shading layer.
The convective heat transfer from glass layer #2 to the air in the gap is
where
Tgap = effective mean temperature of the gap air (K).
hcv = convective heat transfer coefficient from glass or shading layer to gap air (W/m2K).
The corresponding heat transfer from shading layer to gap air is
The convective heat transfer coefficient is given by
where
hc = surface-to-surface heat transfer coefficient for non-vented (closed) cavities (W/m2K)
v = mean air velocity in the gap (m/s).
The quantities hcv and Tgap depend on the airflow velocity in the gap, which in turn depends on several factors, including height of shading layer, glass/shading layer separation (gap depth), zone air temperature for interior shading or outside air temperature for exterior shading, and shading layer and glass face temperatures. The calculation of hcv and Tgap is described in the following sections.
The heat balance equation for the **shading layer surface facing the gap is
where
ksh = shading layer conductance (W/m2K).
θ6 = temperature of shading layer surface facing the zone air (K).
Ssh,1 = solar radiation plus short-wave radiation from lights plus IR radiation from lights and zone equipment absorbed by the gap-side face of the shading layer (W/m2K).
The heat balance equation for the shading layer surface facing the zone air is
where
Ssh,2 = solar radiation plus short-wave radiation from lights plus IR radiation from lights and zone equipment absorbed by the zone-side face of the shading layer (W/m2K).
Solving for Gap Airflow and Temperature[LINK]
For interior and exterior shading devices a pressure-balance equation is used to determine gap air velocity, gap air mean equivalent temperature and gap outlet air temperature given values of zone air temperature (or outside temperature for exterior shading), shading layer face temperatures and gap geometry. The pressure balance equates the buoyancy pressure acting on the gap air to the pressure losses associated with gap airflow between gap inlet and outlet [ISO15099, 2001]. The variables used in the following analysis of the interior shading case are shown in Figure 98.
Pressure Balance Equation[LINK]
The pressure balance equation for airflow through the gap is
Here, ΔpT is the driving pressure difference between room air and gap air. It is given by
where
ρ0 = density of air at temperature T0 (kg/m3)
T0 = reference temperature (283K)
g = acceleration due to gravity (m/s2)
H = height of shading layer (m)
φ = tilt angle of window (vertical = 90o)
Tgap~~= effective mean temperature of the gap air (K)
Tgap,in = gap inlet temperature ( = zone air temperature for interior shading) (K)
The ΔpB term is due to the acceleration of air to velocity v (Bernoulli’s law). It is given by
where ρ is the gap air density evaluated at Tgap (kg/m3).
The ΔpHP term represents the pressure drop due to friction with the shading layer and glass surfaces as the air moves through the gap. Assuming steady laminar flow, it is given by the Hagen-Poiseuille law for flow between parallel plates [Munson et al. 1998]:
where μ is the viscosity of air at temperature Tgap (Pa-s).
The ΔpZ term is the sum of the pressure drops at the inlet and outlet openings:
Here, the inlet pressure drop factor, Zin, and the outlet pressure drop factor, Zout, are given by
where
Aeq,in = equivalent inlet opening area (m2)
Aeq,out = equivalent outlet opening area (m2)
Agap = cross-sectional area of the gap = sW (m2)
If Tgap > Tgap,in
If Tgap ≤ Tgap,in
Here, the area of the openings through which airflow occurs (see Figure 98 and Figure 99) are defined as follows:
Abot = area of the bottom opening (m2)
Atop = area of the top opening (m2)
Al = area of the left-side opening (m2)
Ar= area of the right-side opening (m2)
Ah = air permeability of the shading device expressed as the total area of openings (“holes”) in the shade surface (these openings are assumed to be uniformly distributed over the shade) (m2)
Figure 99 shows examples of Abot, Atop, Al and Ar for different shading device configurations. These areas range from zero to a maximum value equal to the associated shade/screen/blind-to-glass cross-sectional area; i.e., Abot and Atop ≤ sW, Al and Ar ≤ sH.
Expression for the Gap Air Velocity
Expressing Equation in terms of v yields the following quadratic equation:
Solving this gives
The choice of the root of the quadratic equation is dictated by the requirement that v = 0 if Tgap,in = Tgap.
Gap Outlet Temperature and Equivalent Mean Air Temperature
The temperature of air in the gap as a function of distance, h, from the gap inlet (Figure 100) is
where
is the average temperature of the glass and shading layer surfaces facing the gap (K).
H0 = characteristic height (m), given by
where Cp is the heat capacity of air.
The gap outlet temperature is given by
The thermal equivalent mean temperature of the gap air is
Solution Sequence for Gap Air Velocity and Outlet Temperature
The routine WinShadeGapFlow is called within the glazing heat balance iterative loop in SolveForWindowTemperatures to determine v and Tgap,out. The solution sequence in WinShadeGapFlow is as follows:
At start of iteration, guess Tgap as ((Tgl + Tsh)/2 + Tgap,in)/2. Thereafter use value from previous iteration.
Get still-air conductance, hc, by calling WindowGasConductance and NusseltNumber.
Get v from Equation
Get hcv from Equation
Get Tave from Equation
Get Tgap,out from Equation
Get new value of Tgap from Equation
The values of hcv and Tgap so determined are then used in the window heat balance equations to find new values of the face temperatures of the glass and shading layers. These temperatures are used in turn to get new values of hcv and Tgap until the whole iterative process converges.
Convective Heat Gain to Zone from Gap Airflow
The heat added (or removed) from the air as it passes through the gap produces a convective gain (or loss) to the zone air given by
This can also be expressed as
where the air mass flow rate in the gap is given by
Heat Balance Equations for Between-Glass Shading Device[LINK]
In EnergyPlus shading devices are allowed between the two glass panes of double glazing and between the two inner glass panes of triple glazing. Figure 101 shows the case of a between-glass shading device in double glazing.
The heat balance equations for the two glass surfaces facing the shading device are the following.
For face #2:
where
For face #3:
where
The heat balance equations for the shading layer faces are:
For face #5:
For face #6:
The convective heat transfer coefficients are given by
where
In analogy to the interior or exterior shading device case, the air velocity is determined by solving the following pressure balance equation:
where the driving pressure difference between gap #1 and #2 is
The pressure drops on the right-hand side of this equation are:
where i = gap number (1 or 2).
It can be shown that
. Then, inserting these pressure drop expressions into , we obtain the following expression for the airflow velocity:
The choice of the sign of the square root term is dictated by the requirement that
if
, i.e.,
.
Given
we can now calculate
and
, which gives
. The procedure is as follows. We have
where
and
with
. Since
this gives:
Similarly,
Solving these simultaneous equations gives:
Using these in
gives
with
Similarly, from
we get
The overall solution sequence is as follows.
At start of iteration guess
and
. Then
The values
and
are then used in the face heat balance equations to find new values of the face temperatures
and
. These are used in turn to get new values of
and
until the whole iterative process converges.
Airflow Windows[LINK]
In airflow windows forced air flows in the gap between adjacent layers of glass. Such windows are also known as “heat-extract windows” and “climate windows.”
Five configurations of airflow windows are modeled (Figure 102) that depend on the source and destination of forced air. The allowed combinations of Airflow Source and Airflow Destination are:
InsideAir OutsideAir
InsideAir InsideAir
InsideAir ReturnAir
OutsideAir InsideAir
OutsideAir OutsideAir
A common application of airflow windows is to reduce the zone cooling load by exhausting indoor air through the window, thereby picking up and rejecting heat from the glazing (Figure 102).
Figure 103 shows the variables used in the heat balance equations for forced airflow in a double-glazed window.
The heat balance equation for the left-hand glass surface facing the gap in Figure 103 is:
The corresponding equation for the right-hand glass surface facing the gap is:
Here,
Tgap~~= effective mean temperature of the gap air (K)
hcv = convective heat transfer coefficient from glass to gap air (W/m2K).
The convective heat transfer coefficient is given by
where
hc = glass-to-glass heat transfer coefficient for non-vented (closed) cavity (W/m2K)
v = mean air velocity in the gap (m/s).
The air velocity is determined by the gap cross-sectional area in the flow direction and the air flow rate, which is an input value that is constant or can vary according to a user-specified schedule:
where
F = airflow rate (m3/s)
Agap = gap cross-sectional area in direction of flow (m2)
It is assumed that the airflow is uniform across the width of the window.
The mean temperature of the gap air is given by the following expression, whose derivation follows that for for the case of an interior shading device:
where
H = glazing height (m)
Tgap,in~~= gap air inlet temperature (Ti if the airflow source is indoor air, To if the airflow source is outside air) (K)
The outlet air temperature is given by
The equations for glass face #1 and #4 are the same as those for no airflow in the gap (Equations and ).
The convective heat gain to the zone air due to the gap airflow when the airflow destination is indoor air is
where
Cp,i~~= heat capacity of the indoor air (J/kg-K)
Cp,out= heat capacity of the gap outlet air (J/kg-K)
and where the air mass flow rate in the gap is
Fan Energy[LINK]
The fan energy used to move air through the gap is very small and is ignored.
Airflow Window with Between-Glass Shading Device[LINK]
Figure 104 shows the case of a double-glazed airflow window with a between glass shading device. The heat balance equations in this case are the same as those for the between-glass shading device with natural convection (Figure 101 and following equations) except that now
where Agap = sW is the cross-sectional area of the gap on either side of the shading device. It is assumed that the shading device is centered between the two panes of glass so that the airflow, F, is divided equally between the two gaps.
The convective heat gain to the zone air due to the airflow through the two gaps when the airflow destination is indoor air is
where the average temperature of the two outlet air streams is
and
Cp,ave,out~~= heat capacity of the outlet air evaluated at Tgap,ave,out (J/kg-K)
Evacuated Glazing Unit (EGU)[LINK]
Evacuated glazing Units (EGU) are an emerging technology, developed as a concept some 20-30 years ago, but only now approaching wide-spread commercialization and adoption.
Evacuated glazing unit (EGU): cavity thermal conductance[LINK]
Thermal Conductance of the space in an evacuated glazing unit (EGU) is the sum of the conductance of the low pressure gas (air) and radiation conductance.
Conductance of the low-pressure gas
Conductance of low pressure gasses is calculated using formula by Corrucini (Corruccini, R. (1959)).
Where:
= Accommodation coefficients of the gas molecules with the two surfaces. These values depend on the temperature, surface conditions, etc. For the present configuration and conditions, it is expected that a is approximately 0.5. If conservative value is needed than value of 1.0 could be used. With = 0.5, a = 0.333
= Specific heat ratio, air = 1.40. Table 2 lists specific heat ratios for other gasses.
R= Universal gas constant, R = 8,314.462175 J/mol·K
M= Molecular Weight, Mair = 28.97 [mol/g]
T= (T1 + T2)/2 [K]
P= Pressure of the gas [N/m2]
From the paper Collins and Robinson (Collins, R., & Robinson, S. (1991)), B is set at approximately 50 for Air, if pressure is given in torr. Therefore according to Collins and Robinson, for air and approximate conditions of EGU:
CCOND ≈ 50·P
Where P is in torr (i.e., mm Hg).
Note: Conversion from Pa to torr is accomplished by multiplying value in torr by 133.28.
Using formula 2 and assuming T1 to be 20 ºC and T2 to be -18 ºC (expected temperatures of glass surfaces in EGU, if one glass surface is low-e and unit is exposed to NFRC standard environmental conditions), and using SI system of units, the B is calculated as 54.4, which is very close to the value of 50, proposed by Collins and Robinson
CCOND ≈ 54.4·P
We will use exact value, calculated by the formula, so values of will be input into the calculations, which enables more flexible model that can account for special treatment of glass surfaces.
Radiation conductance[LINK]
Radiation conductance for the two parallel plates is given by:
Where:
1= emissivity of the first facing glass surface, [ - ]
2= emissivity of the second facing glass surface, [ - ]
= Stefan-Boltzmann Constant, 5.67 x 10-8, [W/(m2·K4)]
T1= Temperature of the first facing glass surface, [K]
T2= Temperature of the second facing glass surface. [K]
Assuming glass surface temperatures of 20 ºC and -18 ºC, respectively, the following radiation conductances are obtained for the three different glass emissivities:
Clear Glass (1 = 2 = 0.84): CRAD = 3.4 W/m2K
Hard Coat Low-e (1 or 2 = 0.15): CRAD = 0.68 W/m2K
Soft Coat Low-e (1 or 2 = 0.04): CRAD = 0.19 W/m2K
Note: CRAD of 0.09 is theoretically possible using best low-e technology today (i.e., 1 or 2 = 0.02).
Note: Low-e values above are typical values, which will vary by manufacturer. Some more recent hard coat low-e values are at or below 0.1.
It should also be noted that values above are based on the fix set of temperatures, while in reality temperatures will depend on the environmental conditions and surface emissivities (e.g., it cannot be expected that clear glass will have same T1 and T2 as low-e glass).
Equation is precise formulation for two parallel plates at the constant temperature. Simplified equation under these conditions is given in the form of:
Where:
Tm =mean temperature, [K]
Calculation of the U-factor
Where:
tglass = glass thickness; [m]
kglass = glass conductivity; kglass = 1 W/(m·K)
Rglass = 0.003 m2K/W (for 3 mm glass pane)
Ro ≈ 0.033 m2K/W
Ri ≈ 0.14 m2K/W
U-factor of EGU without any pillars (pretending that this is possible) would be calculated using CRAD only. From above radiation conductance calculations:
Clear Glass: U = 2.64 W/(m2·K) [0.464 Btu/(hr·ft2·ºF)]
Hard Coat Low-e: U = 0.62 W/(m2·K) [0.109 Btu/(hr·ft2·ºF)]
Soft Coat Low-e:U = 0.19 W/(m2·K) [0.034 Btu/(hr·ft2·ºF)]
Adding conductance of the air at 0.001 torr (CCOND = 0.08 W/(m2·K), these values become:
Clear Glass: U = 2.66 W/(m2·K) [0.468 Btu/(hr·ft2·ºF)]
Hard Coat Low-e: U = 0.68 W/(m2·K) [0.120 Btu/(hr·ft2·ºF)]
Soft Coat Low-e:U = 0.27 W/(m2·K) [0.048 Btu/(hr·ft2·ºF)]
In contrast, the U-factor of the same configuration with the air at atmospheric pressure will be (For the space width of 50 m, CCOND ≈ 450 W/m2K):
Clear Glass: U = 5.52 W/(m2·K) [0.468 Btu/(hr·ft2·ºF)]
Hard Coat Low-e: U = 5.52 W/(m2·K) [0.120 Btu/(hr·ft2·ºF)]
Soft Coat Low-e:U = 5.52 W/(m2·K) [0.048 Btu/(hr·ft2·ºF)]
It is clear that emissivity of the glass surface makes no difference, because of the dominant conductance of the air space. Also, it is worth noting that the U-factor of such configuration is very close to the U-factor of single glazing.
Evacuated glazing unit (EGU): Glass support element thermal conductance[LINK]
Glass panes in the EGU are separated by an array of small support elements. Typically, these support elements have a cylindrical shape and are often referred to as “pillars.” Typical geometry of the pillar is 0.5-1.0 mm diameter and 0.05 mm (50 m) height. They are typically spaced 1-2 in. apart in a form of square or staggered matrix.
Calculation of the U-factor[LINK]
The conductance of these elements can be measured or numerically modeled to determine accurate thermal performance. Approximate method also exists and is based on the combination of modeling and analytical work for the conduction through small cylinders in contact with infinite parallel plates with thickness much larger than cylinder height.
The following formula can be used to determine conductance of the single pillar, Cp (Collins and Fisher-Cripps 1991):
Where:
k= conductivity of glass, W/(m·K)
a= radius of the pillar (m)
h= pillar height, m
For the square array of support pillars (Collins and Fischer-Cripps 1991) proposes the following formula for their conductance, Cpa:
Where:
= pillar spacing, m
This formula is approximate and does not include effect of the conductivity of the pillar, but it gives good approximation for common materials used in this technology, since conductivity of the pillar does not play substantial role for non-insulating pillars (where “non-insulating” would mean that conductivity of the pillar is equal or higher than the conductivity of the glass pane.
The U-factor of the EGU with support pillars is then:
Where:
References[LINK]
Collins, R., & Fischer-Cripps, A. 1991. “Design of Support Pillar Arrays in Flat Evacuated Windows.”. Aust. J. Phys.
Collins, R., & Robinson, S. 1991. “Evacuated Glazing”. Solar Energy. Vol. 47, No. 1, pp. 27-38.
Corruccini, R. 1959. “Gaseous Heat Conduction at Low Pressures and Temperatures”. Vacuum. Vol. 7-8, pp.19-29.
Thermal Performance of Deflected Insulated Glazing Unit (IGU)[LINK]
Introduction[LINK]
Deflection of insulated glazing unit (IGU) can result in thermal performance degradation or improvement due to the reduction or increase of gap space width. Convection of the gas fill is affected by changed gap space and due to modified convection pattern and shorter or longer thermal path at the center of the glazing unit can result in increased or decreased thermal performance. For the most part, U-factor is mostly affected as a direct result of changed thermal performance; however note that solar heat gain through the window (SHGC) can also be affected because of the effect of inward flowing fraction of absorbed solar radiation, which is affected by thermal performance of the IGU.
Deflection in sealed IGU is caused by the difference in gas pressure in IGU gap vs. outdoor/indoor pressure. Indoor and outdoor pressure can be considered equal, since indoor building environment is in pretty good contact with outdoor environment. We will call this pressure an atmospheric pressure, Pa. The differences in pressure between atmospheric and gap pressure is due to several factors, listed here:
Effects 1 and 2 will be modeled using equations presented below, while effect 3 does not have credible mathematical model. However, cumulative deflection, resulting from all three effects can be measured in the field and its effect on thermal performance can be modeled by specifying center glazing deflection.
Wind or static load pressure effects on deflection is not included in this model at this time, but will be considered for future versions.
Recognizing that indoor and outdoor air pressure could be different, such as in hot box test environment, future plans for the extension of the model will include option to specify different values for indoor and outdoor pressure. Another future improvement to the model will also include linking certain air gaps with indoor or outdoor environment, meaning that respective pressures in linked spaces will be set to equal.
Mathematical Model[LINK]
Mathematical model described in detail here is based on the research work by Bernier and Bourret (1997) and Timoshenko and Woinowsky-Krieger (1959). Bernier and Bourret (1997) of the Ecole Polytechnique Montréal adopted Timoshenko and Woinowsky-Krieger (1959) model for calculating flat plate deflection subjected to the differential pressure field (static), while their original contribution was to develop correlations for changes in thermal performance, based on IGU deflection at the center of glazing location. In addition to adopting Bernier and Bourret (1997) model here, we have also developed model for calculating change in thermal performance of deflected units when this deflection is measured in the field. Therefore, the mathematical formulation, presented here is divided into two sections; 1) calculation of the deflection and resulting thermal performance caused by pressure and temperature effects and 2) calculation of the thermal performance of the IGU when the deflection is measured.
Calculation of the deflection and thermal performance caused by pressure and temperature effects[LINK]
If coordinate system is set as shown in Figure 105 and Figure 106, it is possible to calculate deflection distribution at each point of pane by using following equation:
Where,
Where,
E = Young’s modulus (7.2 x 1010) [Force per unit Area; SI: Pa, IP: psi]
t = thickness of glazing pane [Length; SI: m, IP: in.]
= poison’s ratio (0.22 for glass) [Non-Dimensional]
ΔPi = Pgap(i) - Pgap(i-1) (for i-th pane) [Force per unit Area; SI: Pa, IP: psi]
ΔPi = Pgap(1) - Pa (first pane) [Force per unit Area; SI: Pa, IP: psi]
ΔPi = Pa - Pgap(n-1)(last pane) [Force per unit Area; SI: Pa, IP: psi]
Where,
Pa = atmospheric pressure. [Force per unit Area; SI: Pa, IP: psi]
Where,
Pini = Initial pressure. Applies to all gaps as a single value (input data - measured or otherwise) [Force per unit Area; SI: Pa, IP: psi]
Tini = Initial temperature. Applies to all gaps as a single value (input data - measured or otherwise) [Degree Temperature; SI: K, IP: R]
Vini(i) = Initial volume for i-th gap. [Length*Length*Length; SI: m3, IP: in3]
Where,
Li = non-deflected glazing gap width (for i-th gap) [Length; SI: m, IP: in.]
W = IGU width [Length; SI: m, IP: in.]
H = IGU height [Length; SI: m, IP: in.]
Tgap(i) = temperature of the gap between two glass panes (calculated using center of glazing thermal calculation algorithm, as described in ISO 15099 (ISO 2003). This value is first calculated using non-deflected state and is recalculated after the resulting deflection is calculated. This process is repeated until temperature at next iteration does not differ by more than 0.1 ºC
Vgap(i) = volume of the IGU gap in deflected state [Lentgh*Length*Length; SI: m3, IP: in3]
Where,
Deflection of each pane can be positive or negative and is done solely to establish reference. Current frame of reference is that positive deflection means that pane is deflecting towards left side, while negative deflection means that pane is deflecting towards right side . Whether the deflection is in the direction of reducing the gap width or increasing it, it will be the result of pressure difference, as described in . When pressure in the glazing unit is higher than surrounding environmental pressure, the deflection will be towards increasing gap width (i.e., ballooning), while the opposite situation will result in decreasing gap width (i.e., vacuuming)
The important part of calculating deflection of the IGU is to determine mean deflection value for each glazing pane. Mean deflection value is used to calculate gap volume in deflected state . Mean deflection of glazing pane can be calculated by integrating :
Which is identical with the following expression:
and because integral of sin(x) is equal with –cos(x), above equation will become:
Finally, because
and
values are always equal to -1 for the given range of m and n, above equation will became:
After calculating mean pane deflection the following equation is used to calculate mean gap width:
Where,
Lr(i) = Mean gap “i” width after incorporating glazing deflection. This mean gap width is used to recalculate thermal performance of deflected IGU.
Calculation of the deflection at the center of glazing and mean glazing deflection for each pane is an iterative process, where the initial temperature distribution is calculated for non-deflected state, then deflection is calculated based on this temperature distribution, new temperature distribution is calculated for this deflected state, then temperatures from previous iteration are compared to the current iteration and the process is repeated until the difference is no larger than 0.1 ºC.
At the end of calculations, program will calculate and return maximum deflection value for each pane (i.e., center of glazing deflection). If we label maximum deflection of each pane as LD(i),max, we can calculate this value by substituting x=W/2 and y=H/2 in equation to determine deflection at the center point. Therefore,
For glazing systems with more than two glazing layers, meaning multiple gas filled gaps, the deflection will be calculated for each glazing pane assuming that the pressure in a gap is independent from each other and calculated separately, unless spaces are “linked” together (e.g., stretched film middle glazing that has hole for equalizing pressure).
Non-Linked Gaps in 3 or more glazing layer system:[LINK]
The procedure shown above generally applies to the 3 or more layer glazing system, with the exception that neighboring pressures are no longer Pa, but rather could be Pa on one side and Pgap on the other, or have Pgap on both sides, as shown in Figure 107 for gap “i”. Center of glazing thermal calculation will determine new temperature distribution, after deflection is calculated for each glazing and will be used to determine new Pgap, as per the procedure above.
Linked Gaps in 3 or more glazing layer system:[LINK]
When one or more gaps are linked together, their pressure is assumed to be identical (e.g., in triple glazing IGU Pgap,1 = Pgap,2.) This pressure is calculated from temperatures of bounding glazing for linked gaps (e.g., for triple glazing IGU, glazing 1 and 3) and using neighboring pressures outside of those bounding glazing (e.g., for triple glazed IGU, Pa on both sides).
Note: This feature is not implemented in WINDOW 7.1. It is considered for future enhancements to the program.
Gap(s) Linked to Indoor or Outdoor Environment:[LINK]
If one or more glazing gaps are linked to either indoor or outdoor environment its pressure is fixed to Pa. In combination situations, such as two or more gaps linked together with one of them being linked to indoor or outdoor environment, they will all have fixed pressure of Pa.
Calculation of the thermal performance caused by measured deflection[LINK]
When deflection is measured, it is normally measured at the point of maximum deflection. Maximum deflection occurs at center of the IGU (at W/2 and H/2).
Measured value is typically gap width at the point of maximum deflection, which we can label LG(i). For i-th measured gap the width is equal to:
If we label ratio of mean deflection and maximum deflection as R(i), then:
Replacing and into the following equation is obtained:
Combining with we get the following expression for the mean gap width:
Number of equations given in expression is equal to n-1, where n is number of panes. Therefore, we need one more equation to complete the system of equations that would allow us to solve for all independent variables. To get the last equation we can rewrite in slightly different manner:
Where coefficient K combines all constant terms, while
is given by and
is calculated by, and . Summing over all deflections,
the following equation is obtained:
Note that sum of all
is equal to zero since outside pressure is equal to inside. Therefore, the remaining equation that completes the set of equations is:
Solving system of equations[LINK]
In order to solve system of equations we will present in slightly different manner:
Which in developed form will look like this:
In order to express each
as dependence from
(deflection of inside/last pane) we will need to make sum from first to last, then from second to last, third to last and so on. This procedure will create following set of equations:
Now replacing this set of equations back to :
Which solving by
leads to the following equation:
Calculating
value from this equation and substituting it in will enable calculation of the deflection of remaining panes.
References[LINK]
Arasteh, D.K., J.C. Kohler and B.T. Griffith. Draft 2009. Modeling Windows in EnergyPlus with only U, SHGC, and optionally VT. LBNL report. Full reference to be determined.
Arasteh, D. J. 2009. Modeling Windows in EnergyPlus with only U, SHGC, and optionally VT. Lawrence Berkeley National Laboratory.
Arasteh, D.K., M.S. Reilly and M.D. Rubin. 1989. A versatile procedure for calculating heat transfer through windows. American Society of Heating, Refrigeration and Air-Conditioning Engineers, ASHRAE Transactions, Vol. 95, Pt. 2.
Bernier, M., & Bourret, B. January 1997. “Effects of Glass Plate Curvature on the U-Factor of Sealed Insulated Glazing Units”. Atlanta, GA: ASHRAE Transactions. Vol. 103, Pt. 1. American Society for Heating, Refrigerating and Air-Conditioning Engineers.
Collins, R., & Fischer-Cripps, A. 1991. “Design of Support Pillar Arrays in Flat Evacuated Windows.”. Aust. J. Phys.
Collins, R., & Robinson, S. 1991. “Evacuated Glazing”. Solar Energy. Vol. 47, No. 1, pp. 27-38.
Corruccini, R. (1959). “Gaseous Heat Conduction at Low Pressures and Temperatures”. Vacuum. Vol. 7-8, pp.19-29.
Finlayson, E.U., D.K. Arasteh, C. Huizenga, M.D. Rubin and M.S. Reilly. 1993. WINDOW 4.0: documentation of calculation procedures. Lawrence Berkeley National Laboratory report no. LBL-33943.
ISO. 2003. ISO 15099:2003. Thermal performance of windows, doors, and shading devices – Detailed calculations. International Organization for Standardization.
Klems, J. H. 1994A. “A New Method for Predicting the Solar Heat Gain of Complex Fenestration Systems: I. Overview and Derivation of the Matrix Layer Calculation.”. ASHRAE Transactions. 100 (pt.1): 1073-1086.
Klems, J. H. 1994B. “A New Method for Predicting the Solar Heat Gain of Complex Fenestration Systems: II. Detailed Description of the Matrix Layer Calculation.”. ASHRAE Transactions. 100 (pt.1): 1073-1086.
Klems, J. H. 1995. “Measurements of Bidirectional Optical Properties of Complex Shading Devices.”. ASHRAE Transactions. 101 (pt 1; Symposium Paper CH-95-8-1 (RP-548)): 791-801.
Klems, J. H. 1996. “A Comparison between Calculated and Measured SHGC for Complex Glazing Systems.”. ASHRAE Transactions. 102 (Pt. 1; Symposium Paper AT-96-16-1): 931-939.
Klems, J. H. 1996. “Calorimetric Measurements of Inward-Flowing Fraction for Complex Glazing and Shading Systems.”. ASHRAE Trans. 102(Pt. 1; Symposium Paper AT-96-16-3): 947-954.
Munson, B.R, D.F. Young and T.H. Okiishi. 1998. “Fundamentals of Fluid Mechanics,” Third Edition Update, John Wiley & Sons, Inc.
Papamichael, K. J. 1998. “Determination and Application of Bidirectional Solar-Optical Properties of Fenestration Systems.”. Cambridge, MA: 13th National Passive Solar Conference.
Simmler, H., U. Fischer and F. Winkelmann. 1996. Solar-Thermal Window Blind Model for DOE-2. Lawrence Berkeley National Laboratory, Simulation Research Group internal report, (unpublished).
Timoshenko, S., & Kreiger-Woinowsky, S. 1959. “Theory of Plates and Shells” 2nd Edition. McGraw-Hill Company.
Documentation content copyright © 1996-2014 The Board of Trustees of the University of Illinois and the Regents of the University of California through the Ernest Orlando Lawrence Berkeley National Laboratory. All rights reserved. EnergyPlus is a trademark of the US Department of Energy.
This documentation is made available under the EnergyPlus Open Source License v1.0.